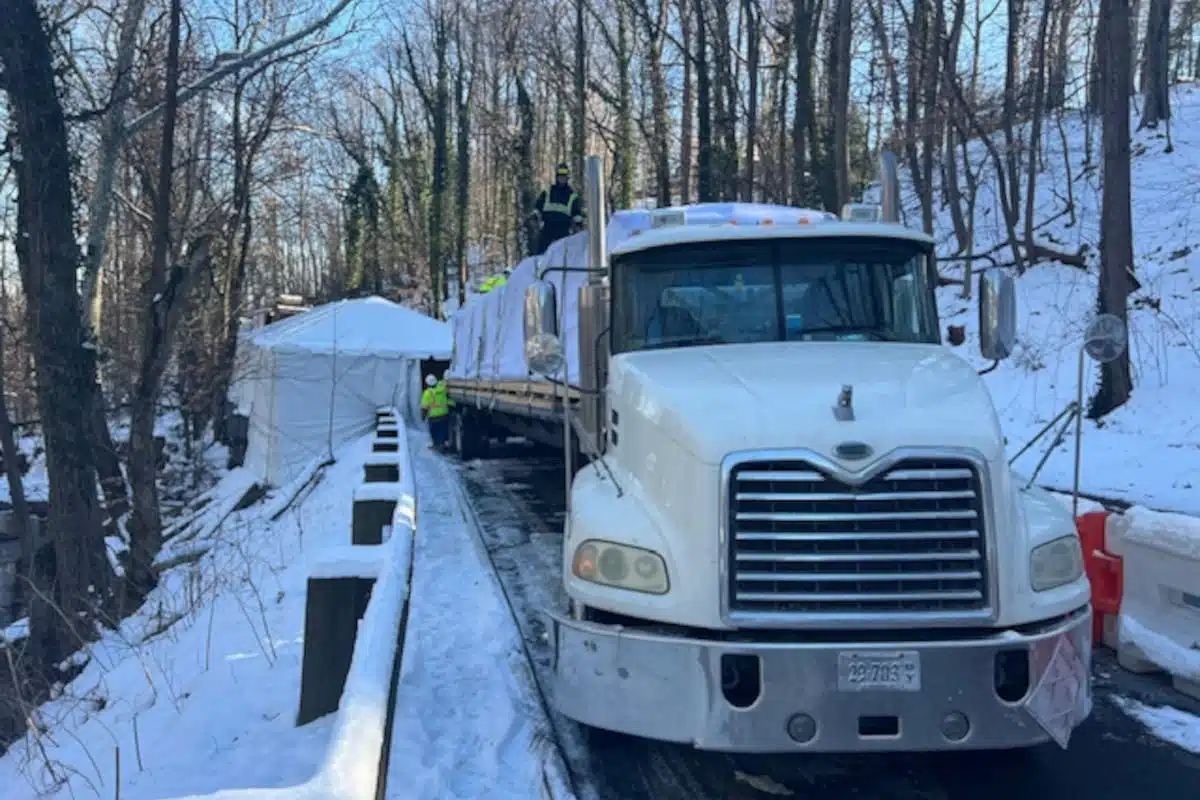
2024 Trenchless Technology Project of the Year Rehabilitation Honorable Mention – Spout Run 3,300-ft. CIPP Pipe Rehab Project
A combination of technical expertise, out of the box thinking, and teamwork turns an improbable cured-in-place pipe (CIPP) lining project in Arlington County, Virginia into a rousing success.
Beyond Arlington’s historical significance, it’s packed with parks, forests, waterfalls, mountains, etc. that make it a wonderful place for people to bike and hike and horseback ride.
As a resident or tourist, this is quite appealing. But when it comes to restoring aging infrastructure, this type of landscape presents extreme challenges.
After a routine inspection in 2019 a 3,300 ft. section of 33-in. sewer that ran from N. Nash Street, through a mountain, to Spout Run Parkway, showed significant signs of degradation, the County wanted to take preventative steps to avoid a possible collapse. Due to the location of the sewer line in addition to Arlington County, the National Park Service, V-DOT and military had a say in the project
There were of eight segments, five of which included deep manholes. Since the Spout Run sewer ran through a mountain three of them were over 100 ft deep (the deepest at 117 ft), one was buried 40 ft below grade, and another had been closed off and backfilled. There was also a manhole located beneath I-66 that runs adjacent to Spout Run Parkway. Both heavily used commuter routes to and from Washington, D.C.
From an installation perspective, due to limited access, depth of manholes, location of the sewer line, the diameter and length of the CIPP liner segments would present its own set of challenges.
Bypass operations always present a challenge and would need to run up a hill, through residential areas, along paths, crossing roads, and over a bridge. It would require special permitting from both the National Park Service and V-DOT. In all 5,500-plus ft of HDPE pipe and five 8-in. pumps would be needed.
The winning bidder on the Spout Run project was AM-Liner East Inc., of Berryville, Virginia.
Why This Project Is Outstanding
The first challenge AM-Liner faced happened before submitting the bid; making sure that Premier Pipe USA’s glass reinforced Tech Liner, manufactured by Applied Felts (now United Felts), could be manufactured in a 33-in. diameter for a single 2,400-ft shot and withstand the internal pressures placed on the liner during installation.
With proper planning, safety measures in place and close monitoring during the installation, it was determined that the liner could be installed, it wouldn’t be easy, but AM-Liner assembled a team of experts to ensure the project’s success.
That group included Mel Willett, Michael Wadding, Robert Samuels, Jeff Geiger and Jimmy Peterson from AM-Liner East; Jim and Jacob Mortell, from Premier Pipe USA; and Mark Chandler and Alex Johnson from Applied Felts (now United Felts). Additional advising came from Steve Leffler and Pat Anderson.
The next challenge arose shortly after the project was awarded. The National Park Service put a pause on the project to allow a protected species of bat to migrate from the park in the project’s path. This delayed the project’s start by three months.
Then came the challenge of the bypass. Since the pick-up line was in a 6-ft manhole, in the middle of a creek bed, a 20-ft above-ground manhole tower was constructed to create enough head pressure for the sewage to immediately be pumped more than 100 ft uphill to the discharge manhole.
The sewer depth required walkie-talkies for two-way comms, 24/7 air quality monitoring, extra lighting and longer winch lines. The crew also met with the fire department, on call throughout, to establish a safety plan.
Producing a liner to the length required had never been done before by the manufacturer. Due to manhole accessibility, only three liner segments were produced: 30 ft, 1,000 ft and 2,400 ft (2.5 x the norm). Also, a wet-out facility had to be set up onsite to impregnate the 2,400-ft liner.
Due to the extra hydrostatic pressure needed to invert the liner throughout the long run, there were concerns of a rupture if it could not be contained while passing through a manhole, unsupported allowing the liner to freely expand radially. After many meetings and calls the team came up with a novel solution. For the inaccessible, buried, manhole a fiberglass CIPP sectional liner was used. To span the accessible manholes, welded wire mesh and chain link fence sleeves were made contain the liner.
None of this would have been accomplished without all parties and entities working together to make this project a success.