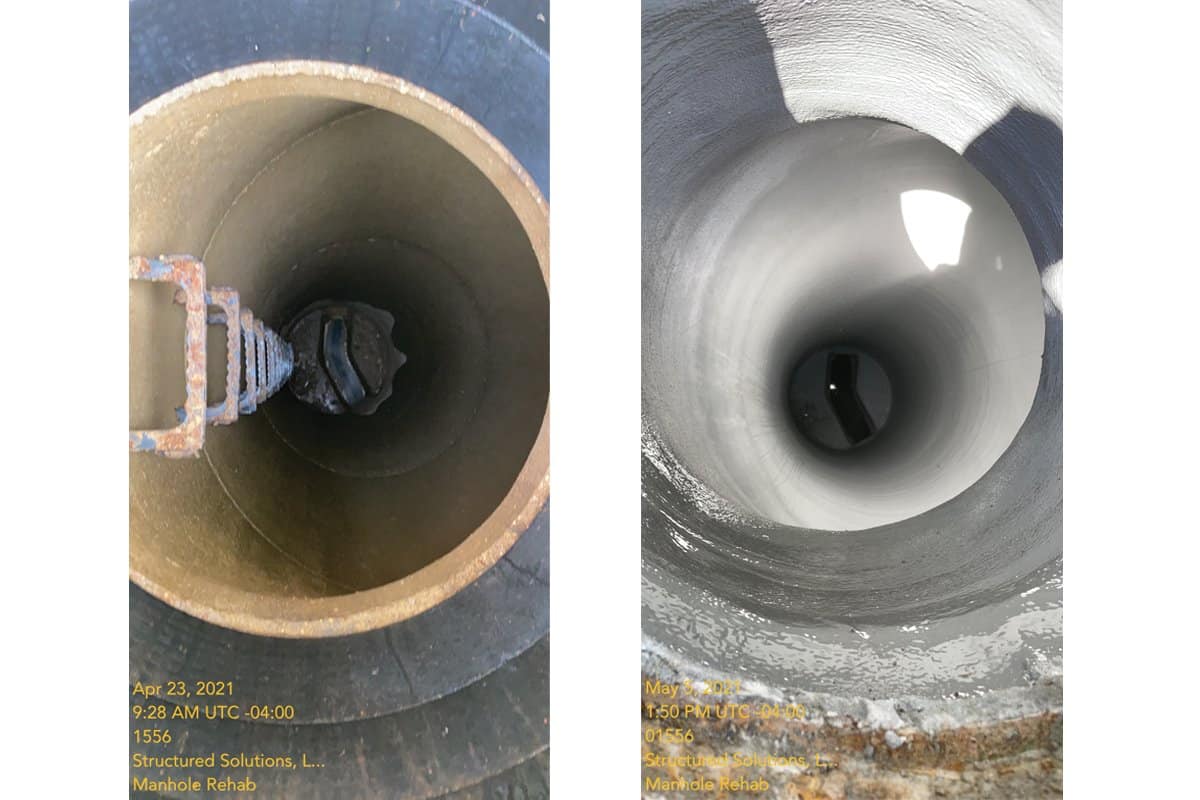
Single-Leg Solution – Mobile Manhole Rehab in the Bluegrass State
Like many cities with centuries of history, Frankfort, Kentucky, has manholes both off the beaten path and right in the heart of the action. These manholes, found in backyards, remote wooded areas, and near farmers’ fields, reflect both the municipality’s legacy of infrastructure and its growth as a capital city.
After serving the community for a range of decades, around 175 bare concrete manholes in the Frankfort Sewer Department (FSD) required rehabilitation. The FSD, responsible for managing water and wastewater, treats nearly 10 million gallons daily, making this upkeep essential.
Many manholes in the sewer system were at critical stages in their lifespan due to the absence of protective linings. The concrete structures faced corrosion from high concentrations of hydrogen sulfide (H2S), a toxic gas produced by microbial decomposition of organic material in sewers. There were manholes compromised by laminar sanitary flow, a slow-moving, consistent stream of wastewater in areas with high water tables that leads to the buildup of sewer gases.
As the team went on, it found additional deterioration from inflow and infiltration (I&I) issues, where rain or groundwater can breach the concrete and directly enter the wastewater stream.
All of these destructive forces can lead to accelerated concrete corrosion and significantly shorter life expectancies for concrete than originally designed.
To seal the compromised manholes — and extend their service lives — the FSD designed a manhole rehabilitation project. Structured Solutions LLC, a Union City, Indiana, firm that specializes in restoring infrastructure assets, was awarded the project and was excited to put the company’s expertise into repairing Frankfort’s sewer system.
“We found some with just a couple of leaks, while others had substrate damage or bench walls that were falling apart,” said Structured Solutions president Ben Price. “This was the first time any type of rehabilitation or sealing work had been done on them.”
An Ease-of-Use Epoxy
Manhole accessibility varied widely across the project, with many of the assets requiring the crew to manually transport equipment.
Drawn to using a single-leg sprayer, Structured Solutions decided to reline each manhole using Dura-Plate 6000 (Figure 1), a high-strength, reinforced epoxy that offers the choice of spraying with either single-leg or plural-component equipment and can also be hand-applied. The lining was also chosen for its high build characteristics, low permeability and fast return to service.
“It really makes doing easement structures easier because of the single-leg capability,” said Structured Solutions vice president Jon Moore. “We were all too happy to eliminate the need to haul bulky plural-component equipment to difficult-to-access locations.”
The two-component, high-build, high-strength, reinforced epoxy lining with 100 percent solids has become part of Structured Solutions’ regular manhole repair treatment arsenal for severe service assets.
Figure 2. Corroded manhole steps (left) are removed during restoration, which prevents workers from entering the confined space without safety equipment.
Concrete Challenge
Across the United States, aging sewer infrastructure and rising waste levels are causing more frequent and severe chemical reactions that damage these systems. Built-up concentrations of H2S leads to microbial-induced corrosion (MIC), where bacteria transform H2S into sulfuric acid, which then erodes the concrete, making it more prone to degradation and spalling.
Concrete has a significant vulnerability – its alkaline nature leaves it highly susceptible to acid attacks. This weakness is particularly problematic in sewer systems where biogenic sulfide corrosion is prevalent.
Increased waste loads and prolonged exposure to harmful substances can accelerate the deterioration of critical structures. Plus, manholes that aren’t watertight allow stormwater and abrasive surface materials like soil and gravel into sewers. That can ultimately accelerate wear on sewer infrastructure — and raise the cost of treating sewer contents — in both rural and urban areas.
In Frankfort, the expansive project — which began in 2021 and will continue through 2025 — requires crews to pre-plan staging and make on-site adjustments based on the specific conditions of each manhole.
“Each manhole we encounter is unique,” said Moore. “But we want to restore them all to the same level of excellence.”
Teamwork in Tight Spaces
In many cases, the routing of the sewer system in Frankfort happened before homes were built, hence the seemingly random siting of many manholes.
Using hand-pulled carts or all-terrain vehicles, the Structured Solutions team transported a single-leg pump to each job site. “Instead of trying to back up a box truck in somebody’s backyard,” said Price, “we wheel single-leg pumps to the structure and still have the same application as you would with a plural-component pump that would be operated from a trailer.”
For the manhole rehabilitations, the crew first removed rusting manhole steps (Figure 2) and degraded concrete. They then cleaned the existing cement with a high-pressure washer at 5,000 PSI to remove any laitance or contaminants from the substrate.
The application team then manually applied new layers of a microsilica mortar material in stages to rebuild the manhole structure, ensuring it had the necessary tensile strength. Where infiltration was present, they used a combination of hydraulic cement and injection grout to seal leaks and allow the coating system to be applied. Then, microsilica mortar was applied at thicknesses up to 1 inch to bring the concrete back to its original plane (Figure 3).
“Once the surface is prepped and we begin the application of the epoxy, it’s a pretty fluid process,” said Moore. “It looks a lot like how you would picture somebody who’s painting a car.”
Crewmembers applied Dura-Plate 6000 to ensure complete coverage and strong adhesion. Applicators were able to build the lining to a 125-mil dry film thickness (DFT) or higher in one coat.
“It makes our jobs easier to have a high-build coating with great chemical resistance that can work in remote areas – without the need for a plural-component pump,” said Price.
Without their single-leg approach, applicators would have to hand-apply materials, including hand-mixing cement and manually applying coatings, due to the inaccessibility of the manholes.
The team was also drawn to the lining’s durability, as it contains reinforcing glass flakes that stack on top of each other and prevent moisture from reaching the substrate.
Newly lined assets are returned to service quickly, enhancing efficiency — in about 10 hours after application, while “the average product return-to-service can be up to 48 hours,” said Price.
Figure 3. Steps can also be a weak point in the structure when dealing with I&I issues; removing the steps ensures a monolithic liner, eliminating weak points.
Invisible Touch
Post-application inspections include visual checks, measuring thicknesses with a wet mil gauge and performing holiday detections to spot and treat defects.
With most manholes, the team is able to restore an impressive 40 to 50 vertical feet a day for easements, even those in the most corroded condition. This efficiency can be attributed, in part, to the applicator’s familiarity with products from Sherwin-Williams Protective & Marine.
Structured Solutions is a member of the coating manufacturer’s Certified Applicator Program, which requires extensive qualified training and means the restoration specialist “can be trusted to meet high-quality standards,” said Price.
The certification program reassures municipalities and engineers of the applicators’ qualifications and allows for additional warranties to be offered on their work.
The team anticipates the manholes in Frankfort may not need additional service until much beyond the work’s 10-year warranty — especially given the coating’s design life of 50 years. It may also be fair to assume many in the town were hardly aware of the application crew’s presence in the first place.
“We pride ourselves on creating as little disruption as possible – in being quiet and stealthy,” said Moore. “Using the single-leg sprayer has been a great advantage. We can just focus on getting the job done right.”
Brian Huffman is business development manager water infrastructure, Ben Fouch is a protective and marine coatings sales representative; Chris Gross is a protective coatings specialist; and Jesse Skinner is a coatings specialist – water infrastructure, from Sherwin-Williams Protective & Marine.