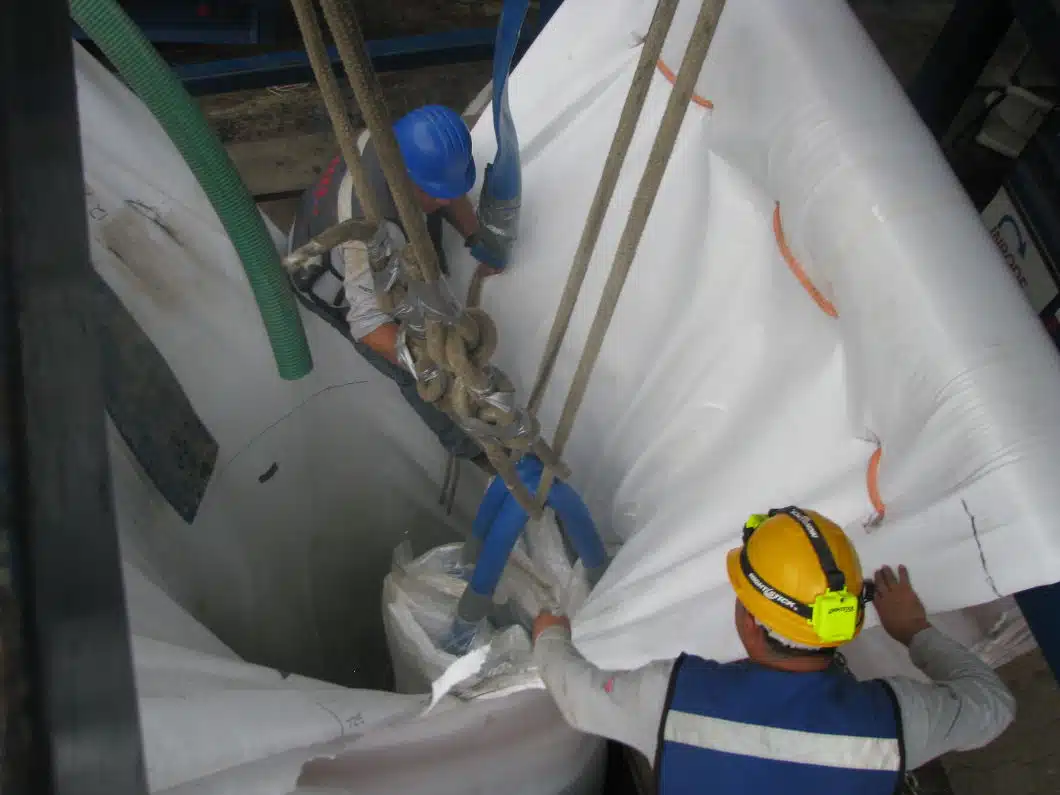
Tech Forum: Resin Considerations for Your CIPP Project
Cured-in-place Pipe (CIPP) is one of the more commonly used tools in the Trenchless Toolbox when it comes to rehabilitating deteriorated pipelines. However, how do you go about picking the right tool? After all, a 3/8-in. wrench is not going to do you a lot of good if you really need a 7/8-in. wrench.
CIPP covers a wide spectrum of products. There are variations in resins, liner materials, and curing methods. While all play important roles in the overall construction, we will focus primarily on resin for this article.
Resin systems have become quite diverse, but for CIPP, they will typically be a thermosetting resin. This broad category encompasses many variations, including polyesters, vinyl esters, epoxies and silicate resins.
When choosing the proper system, one of the first things to consider is the application. On typical sanitary or stormwater mainlines, a polyester is generally used as it will often be the most economical system that still meets the requirements outlined in the various ASTM tests associated with CIPP. However, some rehabilitations may require a more specialized resin.
Styrene-free systems are available if that is a requirement. If the environment is more corrosive or has higher heat requirements, such as in an industrial setting, a vinyl ester or epoxy may need to be considered. In cases of potable water, an epoxy or specially modified vinyl ester may be the system of choice. These systems also tend to be well suited for pressure applications since they are often designed for superior fatigue resistance and give a synergistic relationship with the reinforced liners required for elevated pressures. When minimal shrinkage is needed, an epoxy or silicate system may be the proper starting point.
Once the application is known, it is important to consider how the liner will be cured. Resins will normally have a curing agent or initiator added (sometimes called a catalyst). The most common systems are designed to be cured with hot water or hot air.
Considerations should be given to the size of the liner, making certain the equipment available can provide enough energy to give a proper cure. Occasionally, the initiator level may need to be adjusted to give the contractor enough time to install a liner. Sometimes the installer may choose to use an ambient cure system, designed to cure at lower temperatures. These systems will have limited working time, so are typically reserved for smaller liners such as lateral lines or point repairs.
Another energy source that is becoming more widely used is ultraviolet (UV) light or LED light. These systems use similar resins as their heat cured counterparts, but have initiators designed to cure when exposed to specific wavelengths of light. It is therefore very important to ensure the resin selected is designed to be cured at the same wavelength at which the light train is operating.
We are often asked to explain why an enhanced (often called filled) resin may be used instead of a neat (non-filled) resin. As with most things, there are several variables to consider. The enhanced systems tend to have slightly higher flexural modulus properties, which are key values used in design equations. This could result in a thinner liner which is still capable of meeting the required design parameters. A thinner liner may result in a slightly larger pipe volume and possibly a lower cost, since less resin is needed to obtain similar properties.
However, the enhanced systems tend to be more dense (higher weight), often have lower exotherms (which can be positive or negative, depending on specific circumstances), and do not wet out reinforced liners as well as their neat counterparts. Enhanced systems do not perform as well with UV curing methods since the “filler” limits the depth to which the UV light can penetrate, and thus cure, the liner.
One final thing to consider is customer support. Resin suppliers can often work with you to help determine which resin may work best for a particular application. They should be able to supply various testing results that will help the engineer with their design.
Although testing requirements may vary depending on the environment or application, some of the more common testing requirements are long-term corrosion and creep retention. While it is important to have representative data on the system being used, consideration should also be given to the time required to complete this testing, especially long-term testing. Working together is the best method to make sure all the requirements are addressed.
So, next time you go to that trenchless toolbox, make sure you grab the correct tool (including resin) for the particular job.
Jason Schiro is the business manager-pipeline remediation polymers at Interplastic Corp.