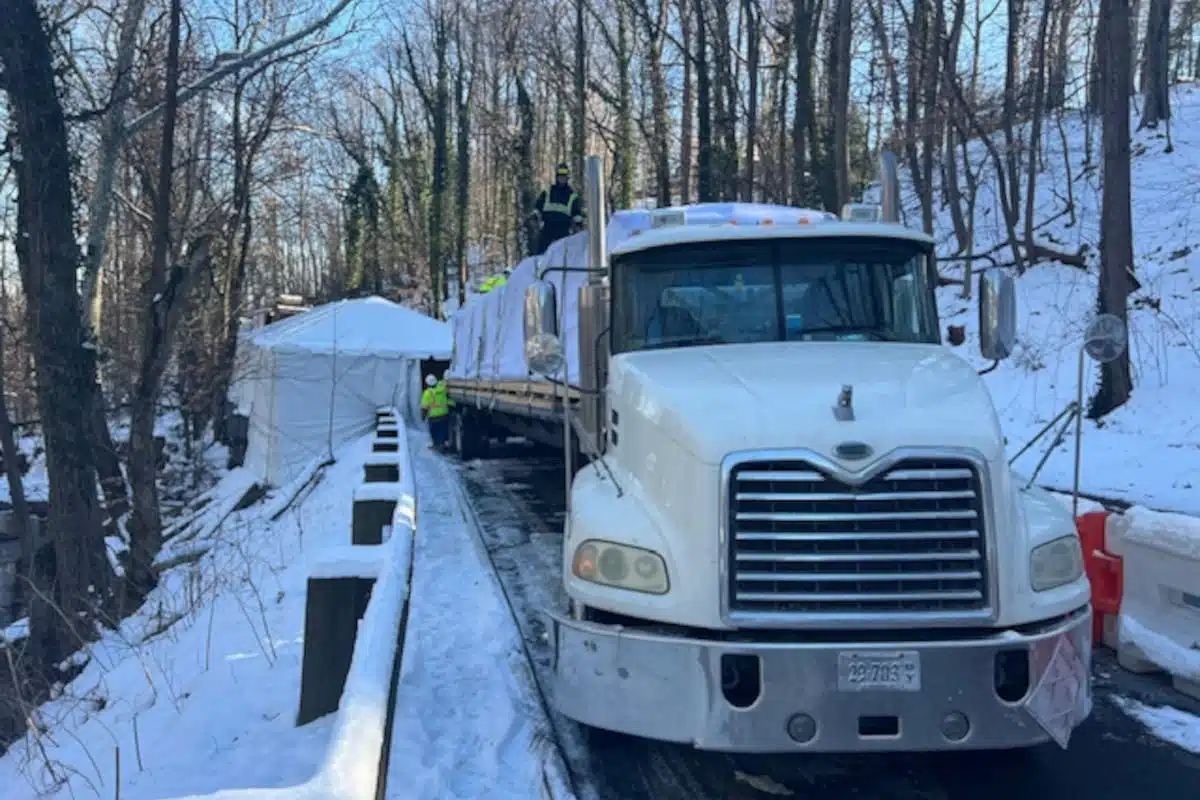
Spout Run CIPP Project Proves with Proper Planning Anything Is Achievable
Arlington, Virginia’s track record for maintaining its critical underground infrastructure is well documented, as is its use of trenchless technologies to do so. So, when it was decided that a 33-in. concrete sewer from Spout Run Parkway to N. Nash Street should be repaired, cured-in-place pipe (CIPP) lining was the chosen method.
It was first learned that the pipe needed attention during a routine inspection in 2019. The sewer showed signs of corrosion, indicated by exposed aggregate, exposed reinforcing steel, infiltration at the pipe joints and small cracks.
The project is part of the County’s program to rehabilitate critical large sewers, which are part of Arlington’s 465-mile sanitary sewage system. With the defects from the 2019 video inspection known, Arlington County wanted to take a proactive approach to rehabilitate these pipes especially with the depth of the pipes reaching 115 ft.
The challenges facing Arlington County, and the contractor lucky enough to win the project, included access to the pipe. In addition to several 100-plus ft deep manholes in neighborhoods, some were on National Park Service (NPS) lands and in Virginia DOT (VDOT) right of way – both of which would require special permitting and variances. None of this gets into dealing with the heavy amounts of traffic related to working so close to Washington, D.C.
With these scenarios, taking an open-cut approach was out of the question – if not close to impossible – and made other trenchless methods unfeasible. This prompted Arlington County to use CIPP, according to Hisham Wahdan, a construction manager, water-sewer-streets, Arlington County Department of Environmental Services.
“This pipe carries a significant amount of flow from, and on federally protected land, and along Langston Boulevard and Interstate-66, with the pipe reaching depths up to 115 ft below ground,” Wahdan says. Adding that CIPP’s benefits included, “The cost of trenchless CIPP vs. replacement with new pipe by digging or other methods was less. And the duration of the project and impact to residence and community using CIPP was much less than other methods the County looked into.”
A plan was put in place and the project was put to bid in early 2023, though the project received attention from several trenchless contracting firms, only two submitted bids. The winning bidder on the project was AM-Liner East Inc., of Berryville, Virginia.
AM-Liner is no stranger to working in Arlington. However, because this wasn’t the typical lining project, the contractor pulled out all the stops to make sure the project could be done.
Can It be Done?
The first challenge AM-Liner faced happened before the bid was submitted; making sure that Premier Pipe USA’s glass reinforced Tech Liner, manufactured by Applied Felts, could be manufactured in a 33-in. diameter for a single 2,400-ft shot and withstand the internal pressures placed on the liner during installation. With proper planning, safety measures in place and close monitoring during the installation, it was determined that the liner could be installed, it wouldn’t be easy, but AM-Liner assembled a team of experts to ensure the project’s success.
That group included Mel Willett, Micheal Wadding, Robert Samuels, Jeff Geiger and Jimmy Peterson from AM-Liner East; Jim and Jacob Mortell, from Premier Pipe USA; and Mark Chandler and Alex Johnson from Applied Felts (now United Felts). Additional advising came from Steve Leffler and Pat Anderson.
According to Mel Willet, vice president of AM-Liner, it was a project that many said couldn’t be done. “This project certainly was not for the faint of heart, but we were determined to figure it out,” he says.
Tackling the Challenges
When it came time to start working, AM-Liner had much-needed support from the County and its subcontractors – Triangle Construction, United Rentals, Mobile Dredging & Video Pipe and Traffic Engineering Services.
The first hurdle that the County helped facilitate was making sure AM-Liner received the proper NPS and VDOT permits to proceed, including making sure work in the NPS areas did not disturb the habitat, mating and migration of an endangered bat. The latter delayed the project’s start for three months.
Then came the challenges of the bypass.
It essentially would need to start and then immediately climb 100 ft. The sewer under Spout Run Parkway was only 25-ft deep; however, the pick-up manhole, which was in Spout Run creek bed, was only 6 ft deep. To complicate things, the manhole was down a 40-ft embankment off Spout Run Parkway.
Michael Wadding, senior project manager for AM-Liner, jokes that executing the bypass was more difficult than the lining itself. He adds that two bypass pumping companies turned down the project because of the challenges.
“By the time the pumps would get the necessary head to push the fluids up that 100-ft hillside embankment, that manhole would have overflowed,” he says. “You couldn’t accumulate enough pressure in the pumps for the 40-ft lift from the stream bed and the 100-ft push up the hillside. That was a problem.”
AM-Liner, working with United Rentals, determined that the best course of action would be building a temporary silo over the pick-up manhole to build enough pressure for a successful bypass. Since it was in Spout Run, Triangle Construction built AM-Liner an OSHA compliant bridge to access the pick-up manhole from Spout Run Parkway. Then came the challenge of getting the bypass up the hillside for the remainder of the project.
The bypass work took place from October to January and used five 8-in. pumps, capable of pumping 10 million gallons per day, and approximately 5,500 ft of HDPE discharge piping running through parks, residential areas, bike paths and VDOT highways. “The bypass was an endeavor. We had to get NPS permits, construct six road crossings, two of which were VDOT roads and two bike path crossings,” says Wadding. “The County helped facilitate all of the permitting.”
Lining Commences
The 3,300 ft project was completed in three shots. First was the 2,400-ft shot from Spout Run Parkway to the median on I-66, a 938-ft shot from Nash Street to the I-66 median and a final 30-ft shot from Spout Run Parkway running upstream.
“This project required that wet-out and inversion happened on site due to the length of the liner,” says Wadding. “We could not haul a wet-out liner on a tractor trailer for the 2,400-ft shot. We discussed splicing two 1,200-ft pieces, but we were too concerned with the volatility of the resins to do that.”
Willet adds that inverting a liner down 100-plus ft deep manholes was also out of the question, as was completing the 2,400-ft installation from the I-66 median. So, the work needed to take place on Spout Run Parkway by closing off one of the northbound lanes to traffic and using the available berm between the road and the embankment. However, to achieve a successful over-the-hole installation required leveling the insertion area with gabion baskets and timbers per NPS permitting.
“One of the things that is important to emphasize is that on that liner, if that liner grew in excess of 2 in., we were afraid and unsure that it would not rupture and cause a catastrophic failure in that line,” says Jim Mortell, owner of Premier Pipe USA. “We had countless meetings until we didn’t want to talk about it anymore of how to properly support these liners, 115 ft down with over 40 ft of head on the line. We couldn’t find anyone else in the industry that has done this to reference off, so we were charting brand new territory in the riskiest situation possible, and we were trying to limit the risk through our planning.”
Because of this concern, AM-Liner developed a plan for the liner to span three open manholes, as well as a fourth abandoned manhole that was under an apartment complex that had a more than 2-in. gap between the bottom of the manhole and the crown of the pipe.
For the latter, since there wasn’t a way to access the manhole from above, Wadding came up with the idea to install a permanent sectional sleeve that spanned the bottom of the manhole. Mobile Dredging & Video Pipe was called in to complete that portion of the work.
For the other manholes that could be accessed, AM-Liner designed a temporary wire mesh, chain link fence and ratchet-strapped bridge to span the 10-ft wide manhole. The plan, once the liner was cured, was to cut these spans out and hoist them back up the manholes.
The lining process took about five weeks from January to the end of February and even though there were some sleepless nights along the way, all three installations were successful and without incident. All involved chalk up the successes to planning, planning and more planning, as well as teamwork and open lines of communication between all entities involved.
Applauding the Team
“Nothing was normal on the project. It was an all-inclusive team effort to deal with all the challenges,” says Willet.
“We had an awesome team of subcontractors. And I want to make sure our site superintendent Jeff Geiger and our operations manager Jimmy Peterson, who was there during the lining operation, get kudos. I can’t say enough about them,” says Wadding. “Jeff was the driving force, he was there every day, he made sure our subs were on their A-game. He knew every element of the job. He communicated with VDOT every day. He was the boots on the ground that made the whole job happen. “
He adds, “At the end of the day it’s the guys who are out there getting dirty, cutting the trenches, putting the liner in, building the bypass, that’s who gets this work done.”
Mike Kezdi is the managing editor of Trenchless Technology.