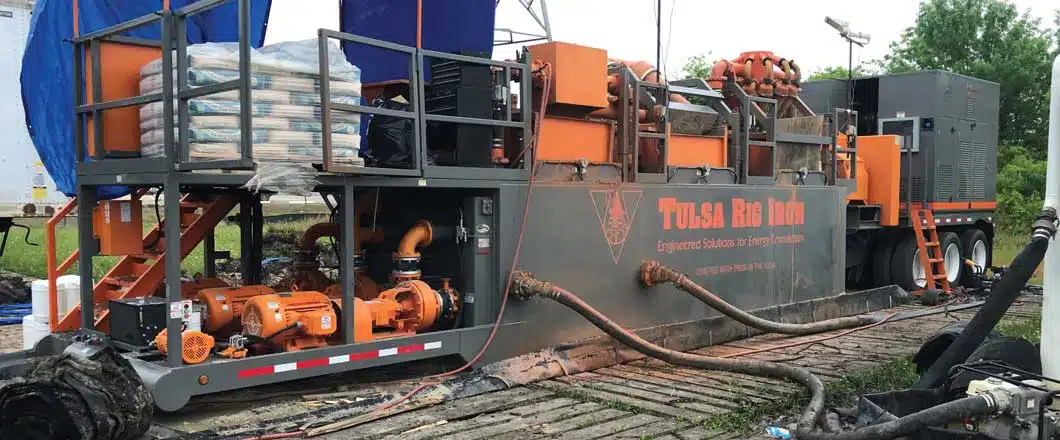
A Tale of Two Drills: Why a Mud Engineer Is Critical
As many of you know, our industry is typically required to have a qualified drilling fluid engineer on site. Their primary job, as a third party, is to ensure the contractor is utilizing mud techniques that align with the current soil conditions. On most sites, there comes a time when the drilling fluid engineer must adapt to changing soil conditions.
Mud plays a vital role from start to finish. Whether it’s 2,000 or 6,000 ft, the mud consistency is crucial to ensure the driller can have a successful job rate. Your mud engineer can typically tell what needs to be added in order to keep the mud properly distributed through the shaker. A detailed mud test takes around an hour, and depending on the outcome a qualified drilling fluid engineer can specify what needs to take place.
RELATED: Are You Making These Drilling Fluid Mistakes?
What Do Drilling Fluid Engineers Do?
They monitor critical properties of your fluids, including dissolved solids, suspension, gel strengths, fluid loss, pH, alkalinities, weight, and viscosity. Every ground condition is different, and you would want different properties for different soils. They also monitor the fluid hydraulics of the project. As a hole gets bigger, regardless if it is the same pump rate, the annular velocity slows down. Annular velocity is the speed that the mud is moving, as it travels up the bore hole. If you have insufficient properties for the reamer pass, you will have bedding which can lead to a plug off and will become an inadvertent return.
Comparing the Two Drills
In 2019, Drilling Fluids Solutions was brought on as a subcontractor for a project going along the Houston Ship Channel. The horizontal directional drilling contractor was awarded the project, which had two similar drilling distances of roughly 5,800 ft and placing 20-in. steel pipe in compromised ground conditions. Our biggest concern was frac out mitigation due to the uncertainty within the ship channel, and the HDD was not allowed to intersect with two drills on opposite ends. Our company was brought on for the second drill, after problems with the first. At that time the general contractor made it a requirement that a drilling fluids engineer be onsite for the second drill.
The first drill had sandy soils, brackish groundwater, high viscosities and a vicinity that displayed a high probability of frac outs. The project took about eight weeks to complete. Due to the plant, and general contractor, there were strict frac out policies. If a frac out occurred, site shut down was required until it was cleaned up. As you can imagine, this resulted in unforeseen costs from downtime with no production.
The 18-in. reamer was completed in five days. At which point, the drill was stepped up to a 30-in. reamer. The 30-in. reamer was completed in seven days, after which a swab was completed.
RELATED: How to Plan and Mix Your Best HDD Drilling Fluid
Second Drill
The second drill had similar ground conditions and parameters. It was about 50 ft — roughly the width of a NBA basketball court — north of the first drill. This drill had viscosities that were maintained at lower points. Our hopes were to have less annular pressures on the compromised formation. However, that means more testing, minimum of every two hours, due to the potential of: contamination, mud suspension, solids content, fluid loss and weight.
By providing the contractor a detailed mud test, he was assured to have consistent soil conditions that reduced the second drill to three weeks instead of eight. The second drill had one inadvertent return, which healed overnight, during the course of the entire project. Full returns were maintained to the rig, overall lowering costs on man hours, overhead and mud costs. After 22 days on the jobsite, the pipe was finally pulled.
“Mud is by far the most essential aspect for an HDD job. Every time Bridger [Cottle] is here, there is never a problem he can’t solve,” said Direct Tech Drilling superintendent Brandon Brown.
Difference of the Two Drills
Now, what was the difference between the two drills?
The first drill had multiple issues with inadvertent returns (IRs). The IRs caused multiple weeks of downtime, not to mention the costs to vacuum trucks with plant access to maintain the IRs. In addition to losing returns, which caused multiple trip outs, the contractor essentially swabbed the hole with the reamer. Again, adding man hours and additional overhead to the overall project.
RELATED: Meet the Experts – Horizontal Directional Drilling (HDD)
In comparison, the second drill only had one IR that healed overnight.
By maximizing the design qualities of the drilling fluid, a drilling fluid engineer can manage annular pressures, at the lowest possible viscosity. In addition, maintain mud properties based on key drilling hydraulic parameters. A good example of this is having an adequate suspension based on the reamer size in conjunction with annular velocity.
Let mud engineers monitor critical properties such as: fluid volume, dissolved solids, suspension, gel strengths, fluid loss, pH, alkalinities, weight and viscosity. Every ground condition is different, and you would want different properties for different soils.
Mud engineers also monitor fluid hydraulics of each project. If you have insufficient properties for the reamer pass; you will have bedding which can lead to a plug off and inadvertent return. All these combined skills are what makes mud engineers the technical expertise to see a project efficiently through to completion.
Bridger Cottle is engineering manager at Drilling Fluids Solutions.