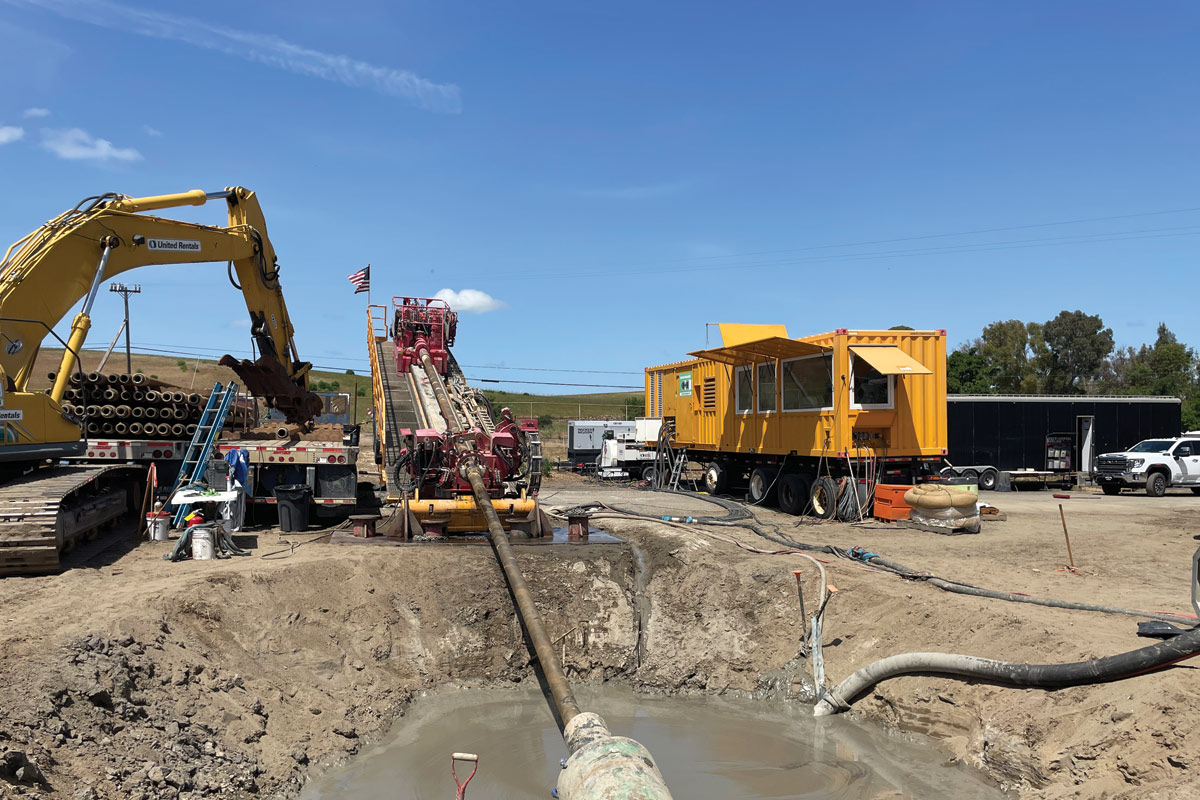
How To Match HDD Fluids to Soil Conditions
Professionals in the horizontal directional drilling (HDD) industry know the importance of matching drilling fluid to soil conditions is paramount to success.
A November 2008 study completed by Digital Control Inc. (DCI) and the University of Texas Arlington corroborate this. They completed two HDD bores installing two 4-in. fused PVC pipes on each bore in identical soil conditions.
The first bore was completed using only water as a drilling fluid and the maximum pullback force was 19,815 lbs and annular pressure was 67 psi. The second installation was completed using a drilling fluid that was appropriately matched to the soil conditions and the maximum pullback force was 4,425 lbs and annular pressures were 18 psi (Caswell, 2008).
This study reinforces the fact that water does not suspend and transport drill cuttings out of the bore path. Water does not provide borehole stability in coarse soil conditions, and water does not control reactive clay.
Having the ability to match drilling fluid to whatever soil conditions are encountered is paramount to a successful horizontal directional contractor.
Soil identification is the first step in matching not only the drilling fluid to the soil conditions, but the drill fluids pumping rates as well. Fortunately, matching drilling fluids to soil conditions is quite simple.
Identifying the Soil
There are two categories of soil:
- Coarse soils/non-reactive soils (sand, gravel, cobble and anything other than clay) – problems include heavy solids to suspend and borehole stability/borehole collapsing.
- Fine/reactive clay soils – problems include clay sticking, swelling, and balling up on downhole tooling.
Soil identification sounds simple, but it is amazing how often contractors get it wrong.
To be 100 percent sure of how the soil is going to react while drilling, go to the entry pit, exit pit or pothole excavation, get a representative soil sample, and stir it into a clear container of water.
Plastic spoons and 16-oz. clear cups are great for this, but if not available, cut the top off a plastic water bottle and use a stick or screwdriver.
Reactive clay will thicken the water and stick to the stirring implement. Coarse non-reactive soil will quickly settle to the bottom, and you will hear sand or rock grinding on bottom while stirring.
When matching HDD fluids to soil conditions, the key functions one must focus on are:
- Gel strength (suspending and transporting drill cuttings out of the bore path)
- Fluid loss/borehole stability
- Controlling reactive clays
We must also address these three functions while minimizing viscosity. The word viscosity is defined as the resistance of a fluid to flow. Therefore, the higher the viscosity, the higher the pumping pressure required to move the drilling fluid out of the borehole.
Inadvertent returns occur when drilling fluid pressures downhole exceeds what the formation can withstand. Fortunately, contractors have a wealth of polymers and additives available today that are designed to help control downhole conditions while minimizing viscosity.
HDD Fluid Gel Strength
Gel strength — the ability to suspend and transport cuttings from the borehole — is the most important function for HDD fluid.
To make a hole in the ground, soil must be removed, and drilling fluid is the means to transport soil/drill cuttings away from the bit or reamer and out of the borehole (even in clay soil conditions). Inadequate gel strength leads to a slower penetration rate, excessive wear on downhole tooling, and stuck or damaged product lines.
Gel strength is the starting point for correctly matching drilling fluids to soil conditions. If a multitude of soil conditions are encountered on a bore, the gel strength must be capable of suspending the largest of drill cuttings encountered in the bore.
There are two ways to increase the gel strength of drilling fluid:
- Add more bentonite, which increases the viscosity of drilling fluid
- Use a gel strength enhancing polymer (xanthan gum) that dramatically increases gel strength while minimizing viscosity.
Xanthan gum is a natural biodegradable polymer that is safe to use. Do not just assume that the gel strength of a drilling fluid mix is adequate. Test it by getting a sample of the drilling fluid mix and stirring in a representative sample of the soil and let it set for 10 minutes or more.
If the material settles, then the gel strength must be increased. In extreme coarse soil conditions such as cobble, mixed metal oxide (MMO) based drilling fluids can be used to convey large heavy cuttings out of the borehole with minimal down-hole pressures and are compatible with drilling fluids recycling systems.
Borehole Stability and Reactive Clays
To maintain borehole stability in coarse soil conditions a drilling fluid must be capable of creating an impermeable barrier between the soil and drilling fluid and positive hydrostatic head pressure from keeping the borehole full of fluid must be applied against the surface of the impermeable barrier.
A sodium Wyoming bentonite drilling fluid utilizes the microscopic bentonite platelets to create this barrier/filter cake, while a polymer-based drilling fluid creates a polymer gel membrane as a barrier. Poly anionic cellulose (PAC) polymer, a modified natural polymer, is used to greatly enhance fluid loss control while minimizing viscosity.
PAC Polymer comes in liquid or dry form and is available in low viscosity (referred to as XL or Xtra Low) versions to help manage viscosity and annular pressures. PAC polymers are also compatible with drilling fluids recycling systems and can also help in combating reactive clays.
Synthetic polymer is most often used to control reactive clays. Clay must absorb water to stick and swell, and a clay-inhibiting synthetic polymer will encapsulate clay particles and delay the hydration of clays long enough to remove the clay from the borehole.
Long chain/high molecular weight synthetic polymers will greatly increase the viscosity of drilling fluids and are not compatible with drilling fluids recycling systems. Low molecular weight/short chain (XL or Xtra Low) synthetic polymers will control reactive clays without a significant increase in viscosity and are compatible with drilling fluids recycling systems.
Synthetic polymers that break clay down work well for smaller HDD projects where the contractor is not using a drilling fluids recycling system, but this type of product should not be used with recycling systems because the clay particles are too small to be removed by the screening equipment and will contaminate drilling fluid.
Final Thoughts
Like drilling fluids, mud pumping requirements vary depending on soil conditions. Coarse soils such as sand will require two to three times the soil displacement while reactive clays will require three to five times the soil displacement.
Monitoring the return flow, especially on back-reams and pullback, provides valuable information on how the drilling fluid interacts with soil conditions and help prevent out-running the drilling fluid, and identify unexpected changes in soil conditions.
As previously mentioned, having the ability to match HDD fluid to what the soil conditions are encountered is paramount to a successful project.
Cup testing to identify soil conditions to see how the drilling fluid mix will interact with the soil takes the guesswork out of matching drilling fluids to soil conditions.
And finally, constantly monitor the return flow. Return flow provides real-time data on how the drilling fluid reacts with the soil encountered. It indicates if the drilling fluid pumping rates are adequate for the speed at which the bit or reamer is cutting.
George M. Dugan is technical sales manager with CETCO Products.