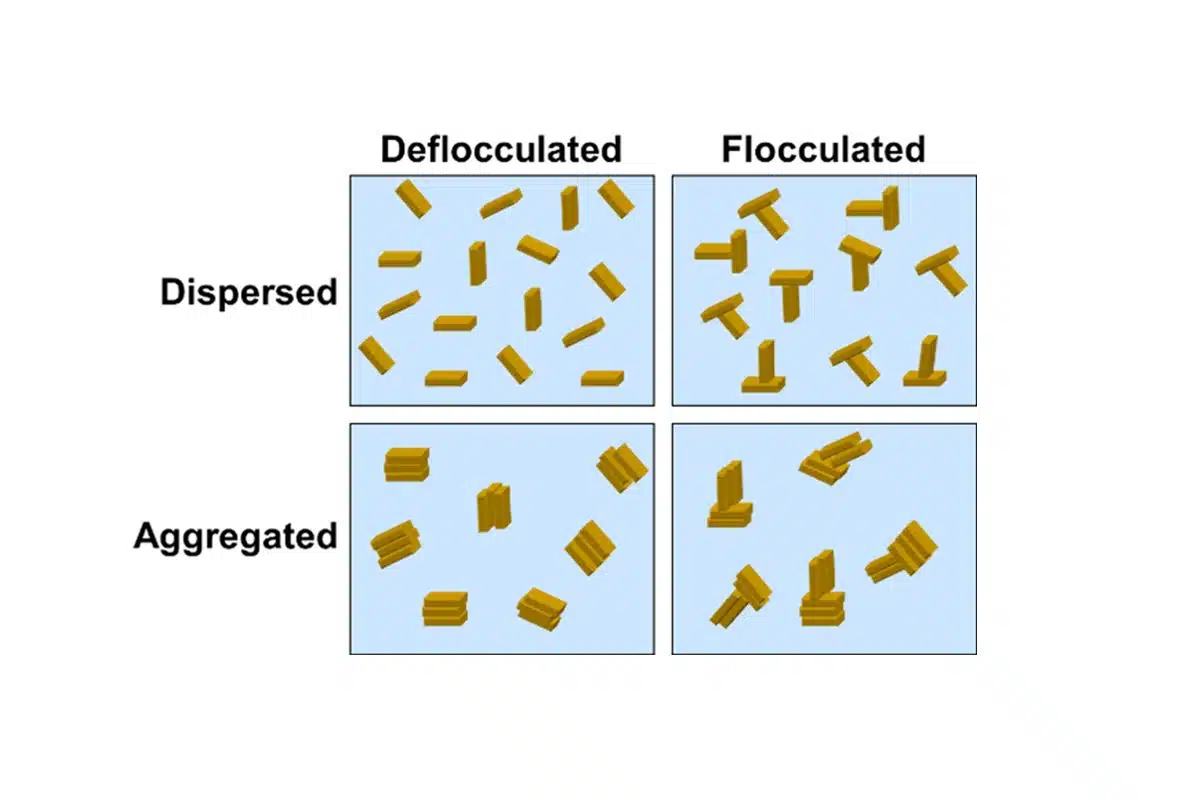
Know Your HDD Solids Content
Different Non-soluable Solids Impact Directional Drilling Fluid Differently
The fundamental rule for trenchless excavation is that you can only mine as fast as you can remove the cuttings. Drill fluid is the conveyor removing excavated solids and essentially consists of water and sodium rich bentonite clay. The typical volume of drill fluid required to clean a bore is three to five times the excavated volume of sand to clay materials.
The drill fluid conveyor must be able to suspend cuttings during removal from the bore, and release suspended cuttings if the fluid is being recycled. For this article, soil is categorized as either granular or clay. Each type affects drill fluid functionality differently.
Viscosity and density are the key properties of drill fluid. Drill fluid is a non-Newtonian fluid, meaning that viscosity (resistance to flow) changes when mechanically stirred and subjected to flow. No flow results in a gel, a solid with weak strength. Gel strength holds solids in suspension until exceeding the gel strength during static conditions such as rod changes and shutdowns. When flow starts, the gel becomes a viscous liquid. The amount of viscosity slows the settling rate of suspended particles. Ketchup is an example of a non-Newtonian fluid. In the bottle, ketchup is a gel until you wiggle a knife into the bottle (rotate and move drill rods). When you pour the ketchup (turn on your pump) it flows. It is this change in viscosity that allows drill fluid to become your cutting removal conveyor.
The type of flow in the bore annulus impacts cutting suspension and transport capacity. Flow may be laminar, turbulent, or transitional. During HDD construction, drill fluid is turbulent at the bit face and laminar during annular flow. Turbulent and transitional flow velocity can suspend cuttings and thus is desirable at the bit. Turbulent flow in the annulus would be optimal, but the resulting pressures require pumps that are larger than presently used and will fracture most soil systems. Laminar flow appears like a sheet flow on the ground surface. Flow is ‘smooth’ along the bore with no stirring action to lift cuttings that have settled to the bore invert. Only at the drill bit discharge is there sufficient turbulent flow necessary to pick up the cuttings.
Dispersed and deflocculated drill fluid stays relatively unchanged when drilling through granular solids. However, drilling through clay that has a molecular charge will change the drill fluid to one of the other three states shown in Figure 1. During cleaning/deconditioning, some of these cuttings will remain electrically attached to the drill fluid.
Granular solids consist of particle sizes ranging from silt to boulders and have no associated electrical charge. Granular solids in drill fluid quickly reach a terminal settling velocity in laminar flow. Terminal velocity is reached when the buoyant weight of the particle equals the fluid ‘drag’ resistance resulting from viscosity. Larger granular particles of the same density fall faster than smaller particles. Cleaning a hole requires the largest granular particle terminal velocity to be slow enough to suspend the particle to the bore entry, bottom-up circulation rate. Larger particles settle to the bottom of the bore resulting in bed load, which causes problems because the hole is not being cleaned.
Bedload cannot be resuspended unless mechanically stirred by motion of the drill rods, mechanical conditioning of the hole to drag the cuttings out of the bore, and/or with turbulent flow emitting from weeper subs. One alternative is to get a bigger pump to increase the annular velocity to move larger particles faster out of the hole. A second alternative is increasing the drill fluid viscosity to increase the suspension time of larger particles. However, more pump or viscosity means more downhole annular pressure and increased frac-out risk.
Cobbles and boulders will not be suspended until the size has been reduced sufficiently for the turbulent fluid at the bit to suspend the broken cuttings. Breaking down large particles takes time and allows the soil surrounding the larger particles to erode resulting in over excavation and reduction in bore wall stability. Sand and gravel sizes will be suspended and removed as a function of the drill fluid viscosity and the effective weight and largest sectional area of a particle. Silt sized granular particles have a terminal velocity near 0 inches per minute. The consequence is that silt remains suspended and will be difficult to remove from drill fluid unless high energy systems are used like centrifuges. High energy systems eventually will remove the bentonite as well as the silt which is undesirable.
Granular cuttings increase the drill fluid density by the weight of the cuttings being carried. Granular soil does not change the viscosity of the drill fluid. Increased return fluid density will increase the annular pressure required to move the drill fluid. Good drilling practices generally have return fluid density in granular soils at or less than 11 pounds per gallon.
Clay acts differently than granular soil. Individual clay platelets are smaller than silt size particles and are electrically charged. Native clays are likely to contain other electrically charged contamination such as salts that are soluble and will have a negative reaction with drill fluid. The electrical charge associated with excavated clay with contaminates alters the drill fluid state to an aggregated or flocculated condition, reducing the ability of the drill fluid to both transport cuttings and clean the drill fluid during recycling. Additionally, a dehydrated electrically charged clay will attract water from the drill fluid thus increasing drill fluid density and viscosity. Mitigation of this effect consists of diluting the return fluid with water or new fluid and eventually, replacing all the bad drill fluid.
Clay excavation by the drill bit and jets can either cut the clay into chunks or emulsify the clay into the drill fluid. The excavation process is very similar to mixing a new batch of drill fluid with either a high energy colloidal mixer or a paddle mixer. High energy excavating breaks the clay into small platelets (emulsion) which allows water to enter the space between the clay platelets and disperses the clay. Low energy excavation, like the paddle mixer, peals and cuts the clay creating chunks of native clay platelets that will only hydrate around the surface chunks thus preventing undesirable hydration of all the chunk internal clay particles. These relatively unreacted chunks can be transported with less impact to the drill fluid.
Cleaning equipment for granular or clay material uses the principles of weight and terminal velocity. A centrifuge increases particle weight by spinning the fluid. Larger particles weigh more than the bentonite drill fluid particles thus can be removed while leaving the drill fluid intact. Shakers and screens reduce viscosity and allow the granular particles to collect on the screen while the lower viscosity drill fluid passes through the holes in the screen.
Additives can be useful to adjust drill fluid chemistry to maximize desirable properties for the soil being excavated. However, understanding the nature of the excavated solids and their interaction with the drill fluid is paramount to predicting how your base drill fluid will behave. Proper geotechnical data and discussions with your drill fluid supplier can significantly improve the ability of your drill fluid to remove the cuttings, improve drill production, and reduce drill fluid cost.
Brian Dorwart, P.E., PG is a senior consultant with Brierley Associates, Bedford, New Hampshire.