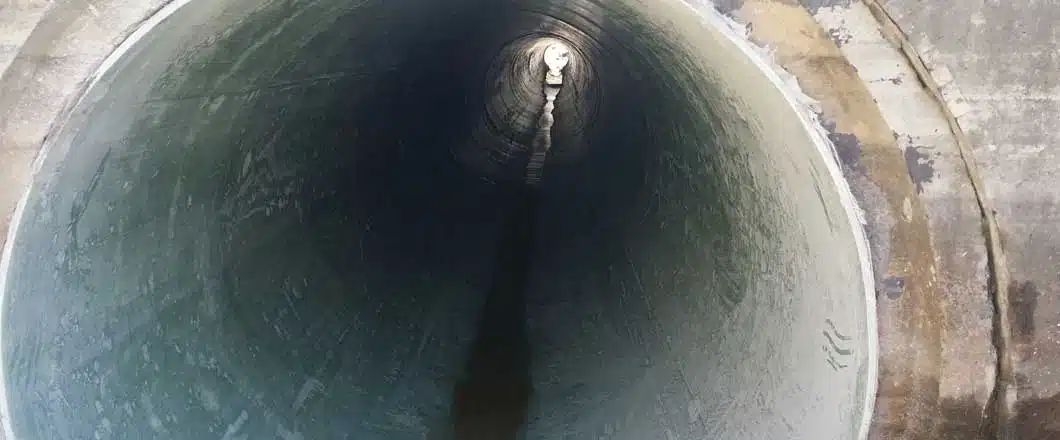
Selecting the Most Appropriate CIPP Installation & Curing Method
In the early 1970s, cured-in-place pipe (CIPP) technology was developed using water inversion and hot water curing. In the early 2000s, other curing methods were developed including steam/hot air. In the mid-2000s, ultraviolet (UV) light curing, for mainline pipe, was launched in North America after becoming popular in Europe.
Today, a variety of installation and curing methods offer choices on how best to accomplish the manufacture of a new cured-in-place pipe (CIPP). Existing host pipe materials and ground conditions, however, will affect the proper and efficient installation and curing of the CIPP requiring evaluation.
RELATED: Celebrating CIPP at 50
Initial project evaluation includes:
- Consideration of pipe size.
- Different pipeline materials have different heat dispersion characteristics (heat sink). Selection of appropriate liner materials and curing techniques will minimize damage to the CIPP and ensure proper curing.
- In pipelines containing pipe sections with different materials, the curing method should be selected considering all materials being lined.
- Pipelines previously lined with a plastic material.
- Ground conditions, water levels and infiltration surrounding the pipeline.
To achieve a successful installation requires that the installer becomes thoroughly familiar with existing project conditions, understands the product, the heating and cooling requirements and how it’s affected by the existing pipe material.
Ambient Resin Curing
Curing is achieved by mixing a set volume of resin and catalyst, causing the materials to react and cure, usually two hours at 75 F. The cure time ,however, will be dependent on the ambient temperature in the installation environment. Applications for ambient curing are primarily for short liners, service connections and repair products that can be installed in a fast, predictable amount of time prior to the resin cure.
Water Inversion & Heat Curing
With water inversion and heat curing, the installer must have enough water available and equipment capable of heating the water to reach required temperature, for curing. The liner is then heated and cooled until the cure cycle is complete.
Water installation and heat curing have shown to provide consistent installation quality. Opportunities include:
- Hot water installation and heat curing, apply to all pipe sizes, types of materials and installation conditions where a moderate curing temperature (usually 180 degrees or less) is maintained. This is a consideration when installing a liner, into host pipe, having low heat sink characteristics.
- Water installation and heat curing is commonly selected for long and large liner installations such as onsite over-the-hole installations.
- The heat from the resin chemical cure will generally be absorbed and dissipated in the water, limiting potentially excessive heat spikes during curing.
Some requirements, that should be evaluated when selecting this cure method.
- Water installation and curing is typically a longer time compared to other technologies.
- The installer has the responsibility to supply and dispose of any liner processing water, in an environmentally acceptable and approved manner.
Air Inversion & Inflation Steam Curing
With steam and air curing, compressed air and steam equipment is required for curing the liner. The installation includes inverting or pulling the liner into place. Air-pressure is required to hold the liner tight against the existing pipe during installation. Then combining steam with the air to elevate the temperature, will cause the liner to cure.
RELATED: NASSCO Brochure Addresses Styrene Use in CIPP
Opportunities for using the steam and air technology for curing CIPP are many.
- Provides higher temperatures, is more efficient and generally will provide for a faster cure.
- Will eliminate need, handling, disposal and cost of large amounts of water.
- Less overall installation equipment is required on the jobsite.
- Less labor is required depending on project conditions.
- Steep grade installations
Some conditions, however, should be evaluated when selecting this cure method.
- Long length liner installation. Curing requires sufficient volumes of steam and air pushed through the entire pipe length, while maintaining and exceeding the required cure temperature. Limiting installation lengths.
- When using steam directly to affect the cure, water condensation must be removed. This can be an issue when the condensate accumulates in a pipe low point or “belly” preventing proper curing.
- When using steam directly, the cure temperature must be properly controlled to avoid excessive temperature increases caused by combination of steam and resin curing temperature, to prevent damage to the liner materials being installed.
Pull-In and Inflate & Curing with Ultraviolet (UV)
Liner material components include a corrosion resistant fiberglass fabric tube in conjunction with photoinitiated resin. Several additional UV technologies are available and provide options for installation and curing of the CIPP product.
Typically, pulled-in and inflated with air, the cure of the resin is initiated by light administered by a mechanical train pulled through the liner, thus curing and creating a CIPP. After the curing process, the inner protective film is removed. The UV light cure has generally become accepted, in North America and is available as an addition to heat cured methods.
Consideration for use of the light cured technology are many.
- Generally, less equipment needed resulting in smaller project footprint
- No residual water or steam condensate disposal required.
- Curing is computer controlled and fast.
- Is not affected by temperature
- Steep grade installations
- Visual inspection of the liner available after installation and before curing.
- No excessive heat during liner curing. The heat generated by the resin cure is recorded
- Can effectively be cured in high and low heat sink environments.
- Infrared sensors monitor key installation and cure information.
Some conditions, however, should be evaluated when selecting this technology and cure method.
Long installations length, limited by pulling distance.
RELATED: TTC Completes Environmental Impact Study of Steam-Cured CIPP
Seriously cracked and broken pipe may damage the liner during pull-in installation.
Limited availability of large diameter liners.
It is important to define the existing pipe material, its condition and the ground water environment. Though most of the underground piping systems can be rehabilitated using any of the available CIPP installation and curing systems, occasionally a system will need additional evaluation to determine which system will be most applicable.
They include pipelines with multiple pipe materials with different heat sinks, various plastic pipe materials, very smooth wall pipelines with minimal mechanical interlocking between host pipe and liner materials and pipelines affected by high heat, to illustrate a few examples.
Gerry Muenchmeyer is owner of Muenchmeyer Asscoaites LLC.