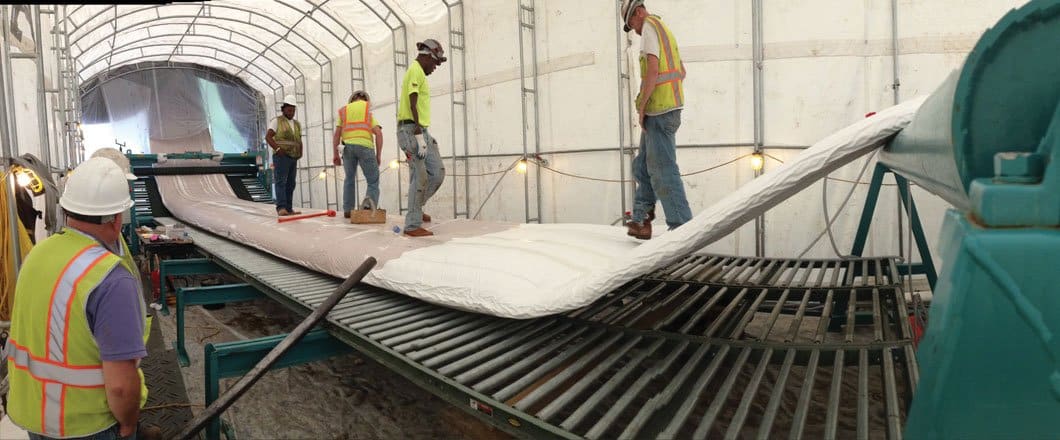
Celebrating CIPP at 50
What’s Been the Impact of the Signature Rehab Method for the Trenchless Industry
Fifty years ago, when the rehabilitation of an egg-shaped sewer was completed in the London Borough of Hackney, there was little fanfare for its success — or for what the results actually meant. Those involved with this seemingly inconsequential project had no idea that by 2021, this method of underground infrastructure rehabilitation would evolve into a multi-billion dollar worldwide, game-changing industry.
Cured-in-place pipe (CIPP) had the most modest beginnings and, in fact, wasn’t initially created to address aging sewer lines. Additionally, the process wasn’t even called CIPP — it was referred to for the first 20 years simply as the insitu form method. The universal moniker of CIPP came during the 1990s.
The 2021 trenchless market reaches into the billions, with more work on sewers lines needed every day as they continue to age and decay. Diameters and lengths are the largest and longest they have ever been, with diameters exceeding more than 120 in. in some projects. Technology and research continue to hum along.
RELATED: Listen to the Trenchless Technology Podcast CIPP @ 50 Series
Today, CIPP is as strong and steady as it’s ever been. The method attained first option status for sewer rehab more than 20 years ago and has expanded its reach to include potable water, gas and pressure pipe. CIPP has also spawned and grown other facets of the trenchless rehabilitation market, including CCTV, resins and robotics, point repairs, as well as methods such as fold-and-form and spiral wound relining. Trenchless research and education have grown exponentially over this time, ensuring innovation and inventiveness for the trenchless industry and introducing the trenchless world to a litany of CIPP pioneers along the way.
As the CIPP industry marks the 50th anniversary of this revolutionary solution to maintain and rehabilitate our underground infrastructure, we spoke to trenchless experts on the impact this once-unheard-of method has had on municipalities and owners, as well as how it influenced the trenchless market. We wanted to know: What do the next 50 years have in store for CIPP? How has this inventive and important rehabilitation method impacted how municipalities address their ever-aging and deteriorating underground infrastructure?
The big question: How is the overall CIPP market faring some 50 years after that first plunge into relining?
As the Story Goes
During the 1960s, future Insituform founder Eric Wood was an agricultural engineer and innovation guru who was brought in to find a solution for a leaky pipe in an air duct located above beds of mushrooms at a mushroom farm. Outright replacing the pipe would be expensive and tricky.
Wood — who tragically died in a plane crash in 1995 — came up with the cured-in-place solution to address the problem and the rest as they say, is history. 2021 marks that anniversary — the birth of the first cured-in-place process for sewer rehab, simply known as CIPP. The CIPP pioneer impregnated a felt tube with polyester resin, wrapped it in a plastic sheet, dragged it 230 ft into the 12-in., egg-shaped, brick sewer and inflated it with air. Then left it to cure. A pipe was given a new life for at least the next 50-plus years.
“That’s where the idea came from,” says Lynn Osborn, longtime trenchless expert and retired long-tenured Insituform employee. “He joined with two business partners, Brian Chandler and Doug Chick in 1971 and they worked with Thames Water in London to do a demonstration project on an egg-shaped sewer. That pipe is still relined today, and it’s been successfully tested several times [since 1971].”
The emergence of a process to take care of and extend the life of sewer lines gave owners and municipalities an alternative to dig-and-replace, thus saving them money, as well as time. If not for the insitu process, how we manage our underground infrastructure would be very different today, experts say.
“Without [CIPP], what would underground infrastructure be like? It would be mayhem,” says Chris Macey, who has worked in the trenchless industry as a consultant, mentor, educator and leader for over 40 years. He’s been with AECOM since 1978. “CIPP changed the construction footprint forever.”
Winnipeg, Canada-based Macey has developed large, sustainable programs for condition assessment and rehabilitation that have facilitated the widespread deployment of trenchless technologies across North America and globally. He has worked on numerous complex assessment and trenchless rehabilitation projects over his career including both shallow ground tunneling and extensive use of a diverse array of lining techniques.
“From my own experience, sewer rehab was a six-week adventure by the time you dug holes and communicated to people on the block and ripped up the entire roadway as opposed to going in and out in a day through two manhole lids,” he says. “CIPP was such a game-changer.”
Though introduced in 1971, CIPP itself didn’t reach North America’s sewer structures until 1976. The appeal and acceptance of this method wasn’t exactly immediate. Insituform, established as a company here, and tirelessly worked to educate and sell the idea of rehabilitating the pipes vs. replacing them. The first CIPP project ever done in the United States took place in Fresno, California, involving a 12-in. sewer line.
Osborn went to work at Insituform in 1984, remaining with the early trenchless giant through 2014. He joined the company at a time when Insituform was the only game in town, owning the proprietary patents, excluding competition. He traveled the country introducing CIPP to skeptical owners and public works officials. “There was some hesitation in those [early] days from engineers and public works directors, as well as from purchasing managers,” Osborn remembers. “But there were also champions of CIPP and people who jumped in with both feet and promoted it, seeing the benefits.”
Insituform Technologies COO Ralph Western points to the company’s early role as CIPP pioneers in the North America. “We went to the market which at that point was mostly dig and replace. And whether the pipe was concrete, cast iron or brick, that is very disruptive because you have to shut down roads, relocate traffic. And that takes a long time,” he says. “What we brought to the market was convenience that was very little disruption to the public. Water and sewer are basic human needs. We had the product here in the United States and United Kingdom and we also had the engineering background to be able to explain to clients how the product works and tout its 50-plus year life.”
CIPP’s Impact
There’s no question that CIPP has been the lynchpin for the trenchless rehab market, dominating this sector of trenchless for many years. How did it become the strongest and most stable asset of the trenchless rehab market and what has been CIPP’s overall impact on the industry?
The key to its explosive and expansive growth starts with the expiration of key proprietary patents once held by Insituform. The patents expired in 1994, opening the door for more competition, which in turn kicked open the door for incredible innovation and acceptance.
Today, we have a plethora of curing methods, such as air, hot water, steam, UV and LED. There are improved and CIPP engineered resins and much more accurate CCTV cameras and equipment, as well having CIPP used beyond sewer lines.
“When the patents expired, you immediately had more resources to be able to go out and talk to more engineers because now it wasn’t just Insituform,” Western says. “It created competition, which I think was good for the municipalities, very good from a technology standpoint because it put pressure on us and the industry to become better with product development and safety equipment. It also helped to grow the market with more opportunities and resources out there to convince the water and wastewater industry that there is another option than dig and replace.”
Osborn notes how the use of CIPP propelled other aspects of the trenchless market, such as cameras, robots and resins. “Before CIPP, there was sliplining, which has always been a good process and there was grouting and dig and replace,” he explains. “When CIPP came in, all of a sudden now there is much more use for CCTV cameras. Cameras existed before CIPP but they really started growing as more and more pipes were being rehabbed. All these contractors needed to do pre- and post-TV work when the rehabilitated a sewer.”
Robot technology to reinstate a service connection to the house didn’t exist before CIPP, experts say. “People started developing robots and that was fairly slow to come,” Osborn says. “Now there are robots all over the place and, as far as I’m concerned, that came out of CIPP. Today, they are used for sewer repairs and point repairs, as well.”
CIPP also created a niche market for specially engineered resins to adhere to create a new pipe within the old host pipe after curing. In the early days, contractors and/or engineers obtained resins from the general resin companies already out there. Now there are several resin and felt companies involved in developing different reinforced materials, materials for pressure pipe, materials for gravity pipe and for gas.
“There have been moderate changes in resins that improve constructability and ultimately increase the installed mechanical properties,” Macey says. “There have been changes in polyester and vinyl ester on the sewer side and epoxies on the water side. The changes have been more subtle than radical over the years but they have made construction far more consistent and the improved properties are genuinely increasing the design life.”
One area that CIPP has influenced and created a new niche is in the large-diameter, high-pressure gas arena. Cured-in-place lining (CIPL) for gas mains developed during the 1990s in Japan and 1990s in Germany with gas utilities taking the lead. CIPL is a descendent of CIPP but is definitely a different discipline. George Ragula, a fixture at Public Service Electric & Gas (PSE&G) in New Jersey with more than 43 years gas-industry experience and past NASTT chairman, has made this a strong focus of his professional work.
RELATED: 2018 Project of the Year Rehabilitation Winner: 36-in. CIPL Gas Main Rehabilitation Project
“PSE&G started looking at CIPL lining very carefully [during the 1990s] because we saw it had a lot of benefits going for it,” Ragula says. “It became the preferred method in project specific applications where pipeline capacity considerations and access are issues.”
CIPL differs from CIPP in several aspects. For one, CIPP is designed to resist buckling whereas CIPL is designed to resist hoop stress, which is caused by internal pressure of the pipe, Ragula explains. He also notes that CIPL, unlike CIPP, does not have a seam and is impervious to gas. Also, with CIPL, there is no annular space and the liner is bonded to the host pipe.
Ragula notes that in CIPL there have been significant improvements in the resins used to give longer pot life vitally necessary for large diameter work and increasing renewal distances and CIPL is experimenting with self-propelled cleaning devices to further improve cleaning, as well as carbon fiber structural reinforcement sleeves to bridge gaps in gas piping caused by certain fittings.
“There’s been a lot of process improvements and efficiencies,” he says. “There have been improvements made in inversion drum size, we’re capable of larger diameters and longer lengths and there’s been improved vacuum technology coupled with robotics technology.” Ragula notes that innovation will continue to play a key role here.
Research and Education
Research and education have played significant roles in the growth of CIPP over the last 50 years and will continue to do so for the next 50 and beyond. The Trenchless Technology Center at Louisiana Tech University in Ruston, Louisiana, is just one of several institutions conducting trenchless research over the last 30 years, with pivotal CIPP-related projects during that time, including a collaboration with NASSCO on use of styrene and CIPP air emissions.
Dr. John Matthews has been the TTC director since 2017 but has been in the trenchless industry his entire career, working on the side of research and education. He says early on, much of the research centered on the CIPP inversion process and its use on laterals — both of which are well established.
“Some of the early research done was typically something that was trying to crack into the market,” he says. “You had something essentially brand new and you were testing it to ensure it’s going to be what you designed. Now, it’s more about technological improvement and innovation related to speeding up curing and installation and stronger materials for high-pressure gas and pressure pipe.”
Matthews notes that in recent years research has focused on examining liners that have finally reached their design life.
“We haven’t had a liner last until its service life because it didn’t exist,” Matthews says. “We are assuming it will last past 50 years and a lot of data has shown that it will last beyond 50 years and look at improvements that can guarantee 75 to 100 years.”
RELATED: CIPP Market – Nearly 50 and as Strong as Ever
What’s Next? What will the next 50 years bring?
There’s a greater opportunity than ever for younger engineers and innovators coming up through the ranks, as CIPP pioneers are at the age of retirement, or sadly, passed on, leaving a void of institutional knowledge behind. Experts agree on the importance of engaging and utilizing the industry’s student trenchless organizations and associations to tap into their well of inventiveness and curiosity — to reach market segments still not embracing the technology, as well as those that push the CIPP envelope.
“We expect CIPP to remain the dominant method for rehabilitation on the wastewater side. There will continue to be innovation on both the product and installation side. The next leg of significant growth in the CIPP industry will be on the drinking water side. There have been hurdles in the past related to maintaining pressure and ensuring a leak-free service reconnection, but we believe technology is being advanced to address both of those needs and create a significant market for trenchless rehabilitation of drinking-water lines, offering a lower carbon footprint and minimal social disruption for communities,” Western says.
“Much of the nation’s critical underground infrastructure is either nearing the end of its useful life or has fallen into a state of disrepair, which means there is great opportunity on the horizon from a drinking water and wastewater perspective,” he says.
Osborn and Ragula see great things ahead for the next 50 years in expansion of application and the future of the hands who will continue to develop and push CIPP. “I really don’t see the sewer market taking another giant boom and that work will always be there paying the bills,” Osborn says. “Where I do see growth is in the potable water market, sewage force mains, pressure pipes and the gas market.”
More universities are including trenchless and CIPP directly into their curriculums all over the globe, preparing the next generation of trenchless CIPP engineers to handle what is to come. “That is a big change,” he says.
“It’s the signature method for the rehab market,” notes Macey. “It drives I/I programs as well as structural rehab programs. Done correctly, CIPP is not something that is a temporary fix or lesser life cycle than a new pipe. It is a new pipe. Educating people on the way to legitimately maximize its life is an important thing to do.”
Sharon M. Bueno is managing editor of Trenchless Technology.