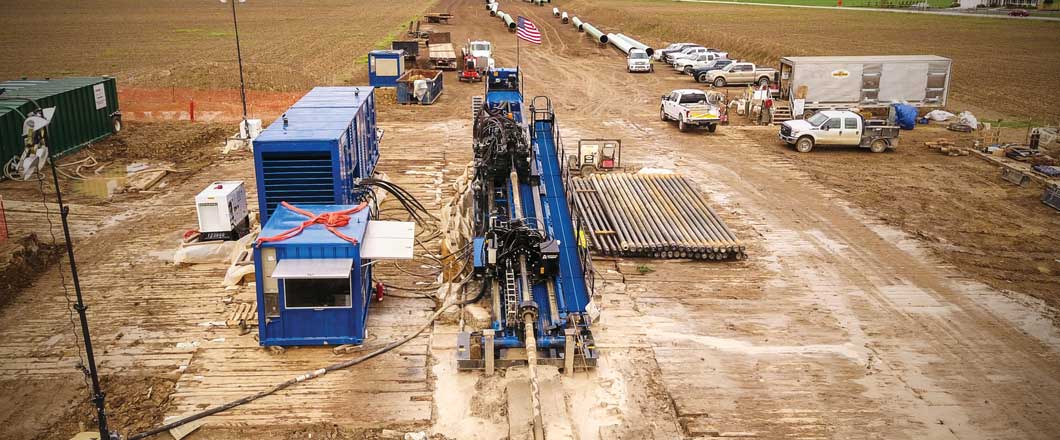
Maxi Rig Work in Urban Settings
Maxi rigs always seem to grab the headlines of the horizontal directional drilling (HDD) market — those enormous and powerful machines with million-plus pounds of torque and pullback. The projects they are used on routinely involve long lengths and large diameters and can usually be found crossing a large swatch of land or a body of water.
Those rigs are just cool.
However, a new trend has slowly developed in recent years that has found maxi size rigs on the lower end of the class — about 100,000- to 250,000-lb level — operating on projects in more urban and congested settings. Their use in these urban settings has also carved out a new niche of work for the HDD market.
RELATED: What’s the Fuss? Contractors Find New Solutions for Slurry Handling, Disposal
Maxi rigs aren’t just found on the large, wide-open spaces of pipeline projects anymore.
American Augers product manager Richard Levings — who has a long and respected history in the HDD industry — says as maxi rigs continue to operate across the world on pipeline installations, supporting growing worldwide energy needs, these rigs are being used to fulfill other infrastructure needs such as underground electrical transmission systems, large diameter water systems and utility installations that require longer bores.
All good news for the HDD market.
“The maxi rig market has consistently grown since its inception in the 1970s,” Levings says. “Due to the global demand for energy, electric and renewable resources, the need for maxi size level pipeline construction and maintenance will generate a sustainable market for years to come. Moreover, as maxi size rigs continue to be utilized in more urban areas as a key piece of equipment for water installation, the market will only continue to grow.
“In terms of the amount of work in progress, 2020 has been consistent with previous years,” he adds. “However, we are seeing more and more maxi rigs projects move into urban areas with increasingly challenging and constrictive jobsites. This has driven many maxi size HDD crews to use telematics and insight features to boost their visibility into their operation and create solutions to their new jobsite issues, resulting in a more efficient production.”
RELATED: Read the 2020 HDD Guide Here
Even during a global pandemic, maxi rig work continues as projects are deemed as essential work during the lockdown across the country. “The maxi rig market was able to continue working during the shutdown on a few essential projects like installing electrical and water infrastructures,” Levings says. “As the world started to slowly reopen, almost all maxi size jobsites were able to resume construction activities while practicing social distancing and other important safety measures to reduce COVID-19 exposure.”
The move into more urban and congested areas has been coming as more and more infrastructure is being constructed to accommodate the growing population. “It’s essential to move water, electrical and energy sources into these areas,” Levings says. “This generally means constructing large pipelines through areas with established dwellings and businesses, which creates a constricted, limited-space and jobsite.”
He goes on to explain that maxi rig techniques have evolved over the past decades to meet these changing jobsites, such as having projects designed into smaller installation lengths so the use of a smaller maxi system can be used. “For example, instead of using a 500,000-lb system, a 250,000-lb unit would allow for a smaller footprint, optimizing the jobsite,” Levings says.
While large HDD sites like this are still the norm for this rig class, the latest trend has the smaller size maxi rigs moving into more urban areas
While creating a new sector for maxi rigs to be used in, challenges are also inevitable to make these rigs work with minimal disruption to the communities. Being used in these locations brings about a different slew of operating issues that contractors and project owners must deal with to ensure a successful project. The biggest challenge is managing the weight and size of the equipment used with these rigs in these areas. “Many new subdivisions don’t have roads built for these larger, heavier loads, so it’s important to utilize the right size maxi system,” Levings says. “Thankfully, advanced technology is helping HDD operators develop systems that manage space and equipment, generating a more efficient and productive operation.”
The advanced technology Levings references involve telematics and other software features. “[This new market] has driven many maxi size HDD crews to use telematics and insight features to boost their visibility into their operation and create solutions to their new jobsite issues, resulting in a more efficient production.”
Telematics allow operators to gather and use real-time data to manage their equipment and optimize their jobsites for increased efficiency and productivity. “By using systems that can provide accurate real-time information, operators can diagnose problems remotely, schedule maintenance and repairs and keep up-to-date documentation of the project’s progression,” Levings says.
Telematics also enables operators to keep stakeholders updated as installations are completed. This helps keep the number of people on the actual jobsite lower, which creates a larger area to work when space is limited, he explains.
RELATED: Maxi Rig Market Update – How Are Things Going for the HDD Industry’s Largest Machines?
“There are two telematics communication systems used on the jobsite to increase productivity — one-way or two-way — however, both systems give fleet managers the opportunity to manage their fleets in one location,” Levings says. “As a one-way communication tool, telematics can transport equipment data in order to track hours of service and the location of equipment. When available for two-way communication, it allows a higher level of diagnosis and the ability to adjust remotely to the equipment in real-time.”
Advanced technology and software are great ways to assist an operator and crew to being more productive on the more constrictive projects. However, Levings notes another tool for the toolbox when it comes to succeeding on the jobsite — a concept pretty simple and just commonsense. “The most effective strategy for contractors to stay efficient, productive and cost-effective while working on smaller jobsites is to plan, plan and then plan some more,” he says. “Smaller jobsites don’t have storage room for extra water, tools, pipe, excavators, etc., and they require a higher level of logistics to move the large equipment in and out of the jobsite as the project progresses.”
Oftentimes, a storage location is required nearby to house all the necessary equipment these smaller sites can’t handle, he adds. As always, operators are instructed to implement best practices for underground construction to complete projects safely and efficiently.
“Many new transportation or midstream pipeline systems are being built around the globe to deliver energy products to the place of consumption,” Levings says. “Maxi rigs will continue to be used in the development of this infrastructure and to install new systems where surface obstructions exist and traditional HDD methods are not feasible.”
Sharon M. Bueno is managing editor of Trenchless Technology.