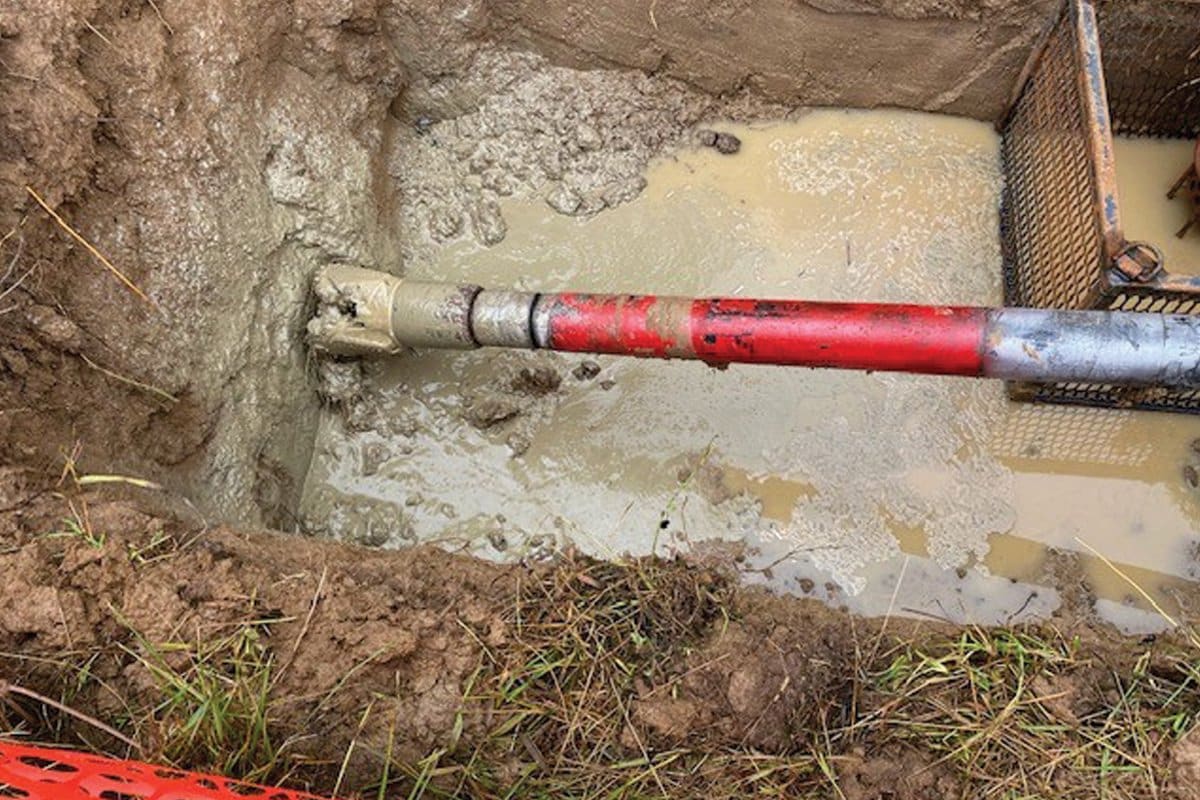
Directional Motors – Pilot Hole Concerns and How to Maximize Performance
The horizontal directional drilling (HDD) industry has relied on directional motors when drilling pilot holes in rock since its inception. Like all things HDD related we have seen several technological advancements with directional motors, as well.
It’s hard to believe but the first motors used by maxi rigs in HDD were 2-7/8 in. with a 4-3/4-in. bit, now it’s not out of the realm of possibility to use a 9-5/8-in. motor and shoot a 16-in. pilot hole in rock.
There is one thing we learned a long time ago about directional motors that should still apply today: What radius they can safely go through without causing damage to the motor or, worse, breaking a threaded connection. Industry standards were created years ago on this topic and the HDD industry has recently moved away from using these as a guideline. It’s important to understand the capabilities of directional motor and stresses they can handle.
We thought it would be a good starting point on this topic to share the capabilities of three common sized motors used in the HDD industry. 5-in., 6-3/4-in., and 8-in.
The 5-in. and 6-3/4-in. motor should only be used when the radius of the curved section or build section is 1,200 ft or greater. A 1,200-ft radius is equivalent to .75 degrees (2 percent) per 15-ft joint or .75 degrees (1.3 percent) per 10-ft joint of drill pipe.
The 8-in. motors require a radius of no less than 2,000 ft. A 2,000-ft radius is equivalent to .85 degrees (1.5 percent) per 30-ft joint.
These would be ideal target radii and are rarely seen anymore. When the design is less than the above stated radii, it causes adverse wear to the bearing stack by putting significant side load stresses on the bit box of the motor causing shorter runs and higher repair charges for the HDD motor supplier. The common practice used to be that customers would rent a motor from an HDD supplier and be responsible for repair charges.
Today, most (U.S.) motor suppliers offer an all-inclusive rental rate for motors where repair charges are included in the monthly rental rate. This model has put the risk of a high repair bill into the hands of the HDD motor supplier.
Tighter designs can also lead to a catastrophic failure of a threaded connections of the motor leaving parts downhole. If these parts aren’t retrieved, a new pilot hole has to be drilled. It’s long been known that HDD contractors can’t include their risk into the projects they bid, if they did, they would never be awarded work. These risks have been exponentially increased by tighter designed pilot holes in rock.
Constructability of bore designs has become the hot topic over the last couple years. If the HDD industry can come together to share and promote the standards for drilling pilot holes in rock, we can all share in more success.
Maximize Directional Motor Performance
The directional motor is as effective as the volume pumped through it. If the mudflow is on the low side of the directional motor power parameters, the horsepower and bit speed of the motor will be lower. The closer toward the high end of the mud motors volume range the more powerful and efficient the motor is. The bit is faster and hydraulics better for top production rates, if the proper amount of mud is pumped.
There are several lobe and power configurations available in the HDD industry. The lobe configuration should be thought of as the fine tuning of the operation, much like selecting the proper IADC code bit for the formation being drilled.
An example of this is, if we know a bore is going to be drilled through a sedimentary formation, the directional motor should have higher bit speeds not as much torque or horsepower to maximize ROP. Conversely, when drilling in Igneous or metamorphic formations the lobe configuration should have more torque and horsepower vs. bit speed. This can lead to a significant increase in ROP on a pilot hole.
The power of a directional motor is measured in stages which correlates to length. The shorter the power section the less power you have.
Matching the power section to the formation being drilled has the same effect as matching up the lobe configuration. Considering these things in the planning stages of the job will have the greatest impact on performance of the pilot hole.
Brad Reinsel is U.S regional director at INROCK.