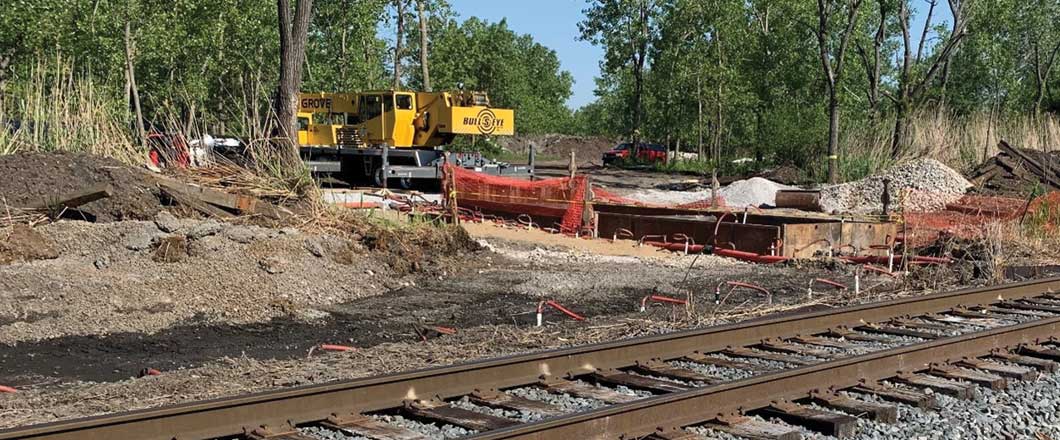
Dewatering 101: An Introduction to Construction Dewatering
Construction dewatering is the process of removing groundwater from a construction site to provide a safe and stable subgrade for excavation.
Groundwater is removed from the site using deep wells, wellpoints, eductors, or conventional “sump and pump” methods. Dewatering may be temporary during construction activities or permanent for the life of the facility.
Safety is imperative at construction sites, employees don’t like operating with wet feet; this includes workers in excavations, pipeline welders and any other worker at the construction site. Also keeping the bottom of the excavation dry reduces the potential for slipping and tripping hazards and can prevent equipment damage. If the groundwater at the site is contaminated with chemicals from a dry cleaner or a leaking fuel storage tank, removing the water from the site reduces employee exposure to the toxins.
A stable work site is important. Proper removal of the groundwater before construction begins can eliminate excavation failures due to uncontrolled water entering the job site.
RELATED: Case Study: Emergency Bypass Solution Enables Critical Repairs for Aging Sewer Line in Los Angeles
Groundwater exerts pressure on the surrounding soil. When soil is removed below the level of the groundwater (static level), water may flow into the excavation. This may cause the walls of the pit or slope to fail leading to timeline delays, personnel safety hazards and equipment damage. Additionally, water pressure from under the excavation floor may cause sand boils or upheaval of the soil which can lead to decrease excavation safety and settlement/subsidence of surrounding structures.
From left, deep well dewatering, eductor and wellpoint systems are some of the options available to remove water from a construction site.
Multiple options exist to remove groundwater from a site; the simplest possibility is called open sumping (reactive water removal), the other options; wellpoints, deep wells and eductors, are based on the installation of wells to pre-drain water from the subsurface (proactive). Along with sumps and wells, associated pumping equipment is required to complete the system.
Open sumping is simply a series of trenches or a small pit or depression in the construction site. As groundwater collects in the sump a pump removes the water to a discharge pipe.
Wellpoint systems are one of the most common dewatering options. Shallow, normally less than 25-ft deep, small diameter wells are completed using jetting drilling techniques. A series of wellpoints are connected to an above ground header, which in turn is attached to a surface mounted vacuum-assisted centrifugal pump that draws water up the well, into the header to a discharge point. Based on physics, the absolute maximum vacuum lift possible, in a perfect world, with no friction loss, at sea level is 33.9 ft. Since those parameters do not exist, less than the theoretical maximum vacuum lift is possible from a wellpoint system under ideal conditions at sea level. Note that changes in elevation, like a project in Denver, and system inefficiencies will further limit the available vacuum lift. Wellpoint systems are simple to install and operate however, area on the project site for location of the header lines and vacuum pumps will required.
Deep well dewatering systems remove groundwater from the site through a series of drilled gravity wells. These wells are larger in diameter than wellpoints and can have a diameter of over 12 in. An electric submersible pump is placed in each individual well. The wells are connected to a header which collects the pumped water for transport to a discharge point. There is no depth limitation to deep wells and large volumes of water can be removed from each well.
Note that electrical power is required at each well to run the pump. Deep well systems need some type of monitoring system as water must always run through the submersible pump. If no water is in the well and the pump continues to run in a dry state, the pump will overheat and be damaged.
RELATED: Big Omaha Environmental Sewer Rehabilitation Goes Smoothly With Expert Sewer Bypass Pumping
Eductor systems are especially functional in low flow dewatering applications. A series of wells are installed and connected to two parallel headers at the surface. One header is the high-pressure supply line and the other a low-pressure discharge line. The eductor “pump” (sometimes referred to as the body) is placed at the bottom of the well and has no down-hole moving parts. Both the high- and low-pressure lines run to a central pump station which feeds water under pressure to individual eductors placed at the bottom of the wells. The eductors use a nozzle/venturi setup to create a localized vacuum and draw groundwater into the well screen and up to the surface, through the low pressure return line to the pump station. Excess system water is discharged from an overflow tank and the remaining water is returned to the eductors via the eductor pump station through the high-pressure line. Eductors have a more complicated surface infrastructure including two header lines, and tankage/pumps at the central pumping stations. However, there are no moving parts in the eductors and a well can run dry with no damage to the system.
RELATED: Dewatering Pumps and Considerations
Jack and bore and auger boring pits often require dewatering. Recently we collaborated with a contractor on a jack and bore project in the Chicago area for the completion of a pipeline under an active rail line. Both the launch and receiving pits of the project required a well point dewatering system. The pits were 40 ft X 16 ft (launch pit) and 20 ft X 16 ft (receiving pit) and were roughly 19 ft deep and required dewatering for construction and safety operations. Approximately 270 well points were required and were installed using the jetting drilling method. The system operated successfully, allowing for the project to be completed in a safe and efficient manner.
In summary, there are multiple options available to remove groundwater from construction sites, supporting a dry, safe workplace environment for workers. Dry worksites allow for construction activities to be completed efficiently and without schedule delays.
David Bardsley, PG, is the director of business development at Griffin Dewatering