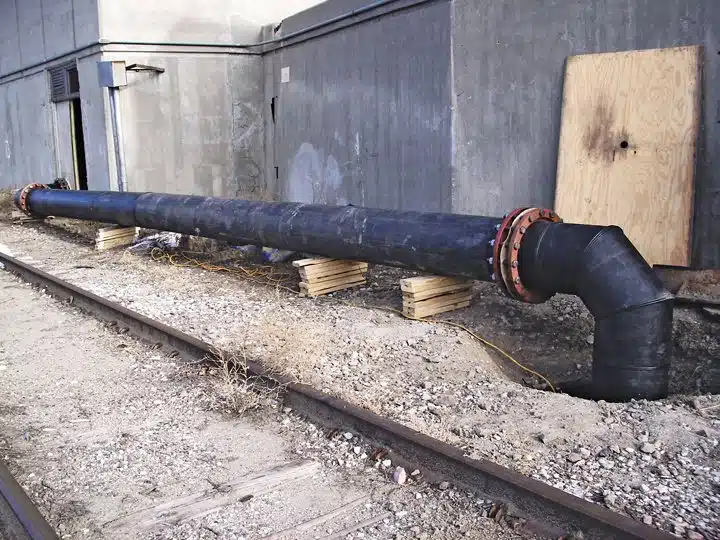
Big Omaha Environmental Sewer Rehabilitation Goes Smoothly With Expert Sewer Bypass Pumping
July 31, 2015
Omaha, Neb., was founded in 1854 and parts of its sewer system date back a hundred years or more — the very definition of problematic legacy infrastructure. Sanitary and storm sewer networks are still combined in many places and more than 50 times a year, during storm events, overflows lead to raw sewage discharge into the Missouri River.
Under the auspices of the Clean Solutions for Omaha (CSO) program, the City is working with the federal government to correct this situation in a responsible and timely manner.
Of course, the infrastructure rehabilitation needed is often complicated and expensive. One project, the Old Leavenworth Lift Station Diversion, will reroute sewage passing through old and massive twin 10-ft x 10-ft box culverts. And one detail of that project, flow diversion, proved to be challenge even for Griffin Dewatering, a firm that has been specializing in large dewatering and diversion projects since 1934.
Building a Pipe in a Culvert
To prevent any possibility of sewage overflow during the Leavenworth project, peak flows of 4,800 gpm (7 mgd) had to be diverted for two weeks, but from Griffin’s point of view that wasn’t the challenging part.
“What really made this project interesting to us was the nearby railroad, and the fact that we had to run our lines under nearby tracks to get to a pump station,” explains team coordinator Dave Gamerl. “We normally pump over ground, but in this case we had to, basically, build a new, temporary sewer line that ran for 300 ft back through the south culvert, then punch through to the north culvert, and then come up through a manhole to get to the pump station.”
And access to the culverts was minimal. “We had a relatively small opening to work with,” says operations manager Todd V. Roche. “Just 22 ft long.”
The temporary line was constructed of 18-in. HDPE, shipped to the site in 40-ft lengths. Given the rigidity of the 18-in. pipe, the 40-ft lengths were too long and had to be cut to 30-ft lengths which were then lowered into the culvert with cranes.
To assemble the 30-ft sections into a working pipe, a McElroy 618 fusion machine, fitted with all-terrain tracks, was inserted into the culvert. To maintain safely ventilated working conditions, all fusing was done within a few feet of the culvert opening.
To assemble the 30-ft sections into a working pipe, a McElroy 618 fusion machine, fitted with all-terrain tracks, was inserted into the culvert.
“We’d fuse a length of pipe, and then use the McElroy [fusion machine] to push the assembled pipe forward 30 ft,” Roche explains. “And then we’d pull the machine back to the opening. As the pipe got longer, pushing got harder, but we were able to successfully complete the 300-ft pipeline we needed.”
At the end of the straight 300-ft run, a complex assemblage of 90 degree and 45 degree bends was needed to route the HDPE through the common wall of the twin culverts and up through the available manhole. The culverts were originally made of brick and mortar and were rehabilitated with shotcrete in a previous project, so a small opening, about 3-ft x 3-ft x 3-ft, could be cut through the common wall between the north and south culverts without compromising structural integrity. Then, a flanged assembly was built topside, carried to the pipe end, and put together.
“The flanges gave us enough flexibility to make all the connections we needed,” Roche says.
Even after negotiating the manhole exit, a serious challenge remained.
“For one thing, now that we were on railroad property, anything we did had to be approved in advance,” Roche explains. “And, to actually access the pump station, a large, cylindrical gate-control structure had to be removed by crane.” But, with careful planning, efficient work and a large crane, the four-ton structure was removed and lifted over a flood wall, on schedule.
With the pipeline completed, the lead contractors installed a bulkhead to block sewage flows upstream from the actual rehabilitation work. Even here, a small challenge arose. “The initial installation of the bulkhead failed due to a fairly significant leak,” Roche explains. “But it wasn’t a big problem. An outside welding firm came in and re-welded, and we were good to go.”
Efficient, Secure and Backed Up
The actual pumping and bypass work, as mentioned above, was fairly routine in terms of water quantity and equipment needed. But CSO is eager to maintain its good rating with Nebraska’s National Resource District and is extremely vigilant when it comes to unnecessary sewage overflows, so Griffin put several safeguards into place to guarantee an especially secure project.
Chief among these was the use of two identical hydraulic submersible pumps and power units. Both were designed and built by Griffin Pump, and are rated for 5,000 gpm, well over the capacity needed for the Leavenworth project. This meant that one of the pumps could be designated as a backup. There are many reasons a pump can fail, including overheating, failing seals and oil leaks, so solid backup design is always a good policy. In this case, both pumps were connected to a custom-constructed ’T’ manifold so that, in case the main pump failed, the backup could be brought online in a matter of minutes. To make sure this happened as needed, Griffin Dewatering kept an employee on site to monitor the pumps 24/7 during the project — normal practice is for Griffin staff to be on hand during work hours, and a lead contractor employee to monitor overnight. Because the work was done in December, insulated blankets were used to prevent freezing.
But in the event, there were no failures of any kind.
“As a rule of thumb, if we make it past the first 72 hours without any problems, the project is going to go smoothly,” Gamerl says. “And that was the case here; really, once we got the pipeline installed, everything went very smoothly and we didn’t leak a drop of sewage. The contractor and the city were both very happy.”
Angus W. Stocking, L.S. is a licensed land surveyor who has been writing about infrastructure since 2002.
Tags: Griffin Dewatering, McElroy