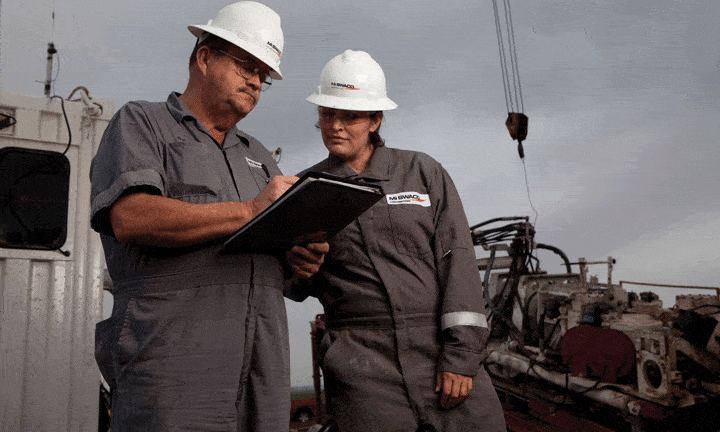
Using Drilling Fluids to Manage Risk in HDD
When installing underground utilities using the horizontal directional drilling (HDD) method, certain risks are inherent to the project. These risks turn into events that regularly impact projects and, in some cases, have become so common that they are accepted as part of the job. Because high downhole pressures and mud losses to the surface are likely to occur, vacuum trucks are kept nearby. Poor hole cleaning and lost circulation are always a problem, so high torque and drag on the product are expected during pullback. An extra ream pass is added to the drilling program to enable pulling the product over the cuttings bed that is left in the bottom of the bore. Yet at what cost?
It has become common place in the HDD industry for project managers to assume that these events are inevitable. Instead of trying to prevent these risks from occurring, project managers incorporate these events into their normal operations and attempt to work around them. Instead of budgeting ways to prevent the likelihood of these risks, the risks are becoming planned events, and attempts are made to cover the financial impact of these uncontrollable events in a fixed budget.
This approach to planning makes it difficult to assign a real dollar value on the financial impact of these events. Proper project budgeting and scheduling become impossible when these events are assumed to be a standard event in drilling. Rig time spent tripping drill pipe, fighting lost circulation, and overcoming reduced penetration rates caused by excessive torque — in addition to the costs associated with unplanned drilling mud disposal and cleaning up frac-outs and spills — cannot be planned for and detracted from the bottom line.
Contractors can minimize or eliminate the likelihood of these events by employing risk management strategies in the form of a drilling fluid (mud) program. Drilling mud is the blood that pumps through any drilling project; it circulates throughout the hole and equipment and interacts with the downhole tooling. While cooling the bit, it washes soil away from the cutters and carries cuttings to the surface. As it circulates through the bore, the fluid acts as a stabilizing medium that prevents sands from collapsing and clays from swelling. The effectiveness of a drilling fluid depends on the mud program planned for the project and how it is implemented and managed.
Schlumberger Oilfiend Glossary—A formal plan developed for a specific well (HDD) with predictions and requirements at various intervals of the (well) bore depth. The mud program gives details on mud type, composition, density, rheology, filtration, and other property requirements and general and specific maintenance needs.
Common Risks in HDD
On construction projects, the primary concern about risk is how it will impact the project’s scope, schedule, cost, and quality. On an HDD operation, those risks may cost time and money as well as affect the reputation of a company or the industry as a whole. Often, risks are interrelated; preventing or reducing the likelihood of one risk, in turn, prevents or reduces the likelihood of another.
RELATED: Drill Master: HDD Risk Reduction
A few major risks include
• costs associated with frac-outs from high downhole pressures
• stuck pipe or tools because of hole collapse or poor hole cleaning
• slow penetration rates, bit balling, string torque, or a combination of all three
• excessive wear and tear on drilling equipment caused by string torque and drag
• high mud disposal costs because of high mud viscosity and weight.
VIRTUAL HYDRAULICS drilling fluid simulation software maps the hole cleaning index and cuttings bed development in a 7,000-ft HDD operation. (Image of Schlumberger)
Reducing the Risks
Reducing HDD risk requires answering a few questions:
– What risks are associated with the project?
– What risks can be minimized or eliminated?
– What actions during planning can help manage risks and reduce their impact?
– What are the cost and tradeoff for managing the risks?
– Is the tradeoff beneficial to the project?
Drilling fluid selection is a major component of managing risk during HDD. The project manager should implement a formal mud program with clearly outlined methods of executing, monitoring, controlling, and revising as drilling conditions change. The program’s complexity should be related to the risks involved in the project. Mud programs for low-risk, short, small-diameter shots using a small- to medium-sized rig in relatively good ground conditions can be as simple as a laminated chart that conveys how much of each product is needed per 1,000-gal tank. A corresponding budget provides the estimated mud costs.
One example of how a proper mud program can help improve operations is illustrated by a contractor in West Texas. The contractor’s project involved a 60,000-lb midsize HDD rig in ground conditions of sand and gravel. Using bentonite and water, the contractor found that the pilot hole could not be drilled past 300 ft because rotational torque was too high. After fighting the hole for three days at a total rig-time cost of $40,000, the contractor feared hole collapse and stuck tools and called M-I SWACO for a solution.
M-I SWACO came on location and worked with the contractor to determine risks and objectives (Figure 1). To reduce torque, the contractor needed a fluid that would stabilize the hole, remove the cuttings from the bore, and suspend the cuttings to keep the bore from packing off. A customized mud program was designed using MAX GEL viscosifier, SUPER-VIS suspension agent, PLATINUM PAC stabilizing polymer, and PLATINUM ROD EASE lubricant in a 1,000-gal batch recipe. After flipping the mud system to the customized fluid, the contractor was able to punch out the 1,200-ft pilot hole in two shifts and ream it in four shifts. The product was pulled on day seven.
Larger, more-complex, and higher-risk projects require a more complex mud program. Planning could include a geotechnical investigation, pressure evaluation, drilling fluid designed to achieve specific goals, and methods to monitor and maintain the fluid.
RELATED: Project of The Year- New Installation: HDD & the Houston Ship Channel
With large-scale projects, M-I SWACO offers services using engineering software like PC MOD and VIRTUAL HYDRAULICS drilling fluid simulation software. M-I SWACO project engineers work directly with project managers to determine their needs for the drilling fluid. Using VIRTUAL HYDRAULICS software models based on the parameters of each specific project (geotechnical parameters, drilling profile, tooling, equipment, and penetration rates), the project team can determine which mud properties are required for adequate hole cleaning, hole stability, controlled drilling rates for pumpout, and penetration rates to keep pressures under the fracture gradient (Figure 2). Using this data, a mud program and budget can be made for the project and presented to the contractor. In the field, drilling fluid specialists work with the contractor to execute, monitor, and adjust the plan as the project progresses. These services and software have been used successfully on HDD projects up to 7,000 ft in length at diameters up to 48 in and oil and gas wells more than 30,000 ft in depth.
Conclusion
No matter the scope of the project, the mud plan should be designed to maximize the critical functions of drilling fluid in HDD:
– removing cuttings from the bore
– mechanically and chemically stabilizing the borehole
– suspending and releasing cuttings
– lubricating and cooling downhole tools
– transmitting hydraulic energy to the bit.
Proactively including a mud program in the overall HDD project plan can result in significant cost savings over the course of the project. Just like car insurance, “mud insurance” varies by the quality of the coverage. Investing in the proper mud plan quickly and effectively reduces risks and can save thousands, tens of thousands or hundreds of thousands of dollars depending on the scope of the project.