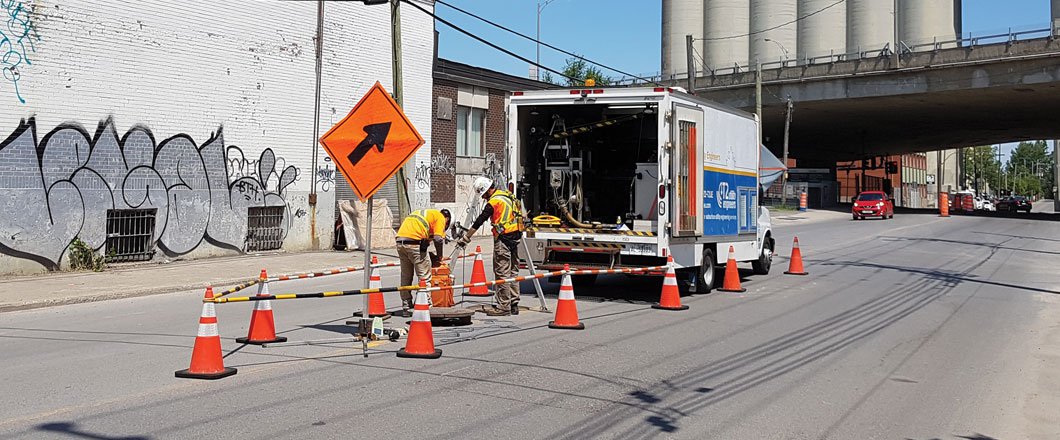
Understanding the Level of Effort to Be Applied to SUE Investigations
It is clear that not all projects are alike and each have their own distinct level of risk and the amount of utility investigation, in this case, using ASCE 38 as the investigative standard, that would be required to attain the comfort level of utility risk mitigation to deliver the projects.
One major aspect is having an informed engineering consultant and project owner. As clear as this sounds, it is not always the case. Many times, I have observed consultants performing minimum requirements in the terms of reference (TOR) for the request for proposal (RFP) language, rather than performing their services with an eye toward delivering a constructible project while protecting the public health, safety, and welfare.
Some projects will deserve a robust utility investigation; others might be acceptable with somewhat less of an investigation. Project conditions and contract documents generally will inform the level of effort required. For instance, in urban areas, horizontal directional drilling (HDD) is considered an “ultra-hazardous” activity due to the consequences of potential damages wrought by undocumented, abandoned, and congested utility systems hidden from view and with poor and missing record information.
Regardless of what a contract document may state, the engineer should be cognizant of this danger and remediate it in some fashion. If the TOR and RFP in any way state that the use of SUE or ASCE 38 is required, then there must be a competent SUE firm or individual on the project licensed to practice engineering in the local jurisdiction. This is an international standard as well as a standard of practice. Many documents and 30 years of practice in Canada and the United States form the basis of this statement; ASCE 38-02, CSA-S250, NASTT’s HDD Good Practices, and ASCE’s SUE Guide for Municipalities just recently published are but a few.
A significant misunderstanding of ASCE 38 is that using One Call or private locators does not equate to SUE and therefore the minimum Utility Quality Level that can be assigned by a licensed engineer to any utility segment on the plan would be QLD – the most basic and most uncertain depiction available. And maybe for a few simple projects, that level of effort is sufficient, but most projects, regardless of parameters, should result in a mix of achieved Utility Quality Levels (QLA, QLB, QLC, QLD) based upon the negotiated contractual effort and the achieved results that are dependent upon the synthesis of records, experience, knowledge, geophysical equipment and success and diligence.
The use of SUE on projects varies from methods of construction, expected utility congestion, age of the site, history of the site, density of population and building demographics and more. These factors inform the amount of risk and therefore the amount of utility investigation that are prudent for the project design. With all of these considerations 2 projects come to mind where the application of the QL and impact on existing utilities were vastly different. A Sewer Trunk System (STS) rehabilitation project and large-scale project that is a part of the City of Toronto Basement flooding protection program mega multiyear project.
The Rehabilitation STS project was primarily done through trenchless rehabilitation methods and had minimal risk on existing utilities with the exception of where the sewer bypasses would need to be constructed. With this information and choice of Construction method, T2 Utility Engineers (T2ue) was assigned to develop a SUE investigation and tailor the level of risk mitigation and QL applied to the areas of risk. T2ue had collaborated previously on numerous projects of these kinds and learnt a great dynamic collaborative approach to providing service.
The objective of the recommended SUE investigation was to obtain concise chamber dimensions of the sanitary trunk sewers and reduce the uncertainty that existing utilities create on the project. T2ue’s investigation involves Record Request Circulation, Topographical Survey, Utility Designating, Invert Investigations and CCTV Investigations. The recommended project approach included a utility investigation that was of differing levels of effort for different areas of the project. In this case, a QLB (geophysics) effort was made only on the areas of where the sewer bypasses were being planned with some additional survey and elevations at distinct points along and adjacent to the project alignment to provide supplemental information on MH elevations and acceptable grading cuts.
The investigation utilized a wide variety of geophysical utility designating techniques to determine the presence and best horizontal position of utilities capable of being identified within the project limits. Utilities found and documented included water, gas, electric power and telecommunications. The investigation also included induction scanning to identify utilities that were not on furnished utility record drawings. Sewer chambers were opened, accessed, and documented to confirm the actual pipe sizes, materials, offsets, elevations and drainage direction. Mapping of the system, alignments and interconnections are shown on the SUE Mapping Drawings based on a combination of record information received, results of the inspections, surveyed MH’s/CB’s and professional judgment. Pole camera and CCTV inspections were conducted within critical areas to verify chamber information. 3D Laser scanning was utilized to obtain internal dimensions of each sanitary chamber. All utility data were referenced to local coordinates in coordination with Ivan B. Wallace OLS (IBW), a licensed Ontario Land Surveying firm. The information was referenced into the provided topographic base map using the established Project Control (horizontal and vertical coordinates).
T2ue produced the SUE Mapping Drawing (Quality Level D, C and B as per CI/ASCE Standard 38-02) showing the horizontal alignment of the underground utilities at the achieved quality level over the project area.
The Second Project that came to mind was The Basement Flooding Protection Program (BFPP). A part of the BFPP IV currently under the final phases of design, was one that had a vastly different purpose than rehabilitation. This project was created to upsize and handle capacity of sewer system for today’s density and wet weather events that had not been anticipated years ago with the creation of the City of Toronto and its vast neighborhoods. In August 2005, Southern Ontario experienced one of the largest storms it had since Hurricane Hazel. More than 150 millimeters of rainfall in a two-hour period—it was in excess of a one-in-a-100-years storm. Large areas were flooded and many houses experienced sewer backup and many roads were impassable. Most areas affected were built in the 1960s. After this unprecedented event, the City of Toronto took the steps of initiating the Basement Flooding Protection Program. Flood events since then, most notably in July 2013, have resulted in additional flooding and the subsequent expansion of the program.
The Basement Flooding Protection Program is a billion-dollar, multi-year program to help reduce the risk of future flooding by making improvements to the City’s sewer system and overland drainage routes. The upgrades to the sewers are happening in mature, built-up areas, meaning that they not only have potential impacts on the existing sewers but also on all other buried and aerial utilities within the project area. Within this mega project one area that is currently being designed again had Marya Jetten P.Eng of Jacobs as one of the many project managers on this project. T2ue has been engaged in this project since its inception in 2008 of BFPP I and subsequently BFPP II BFPP III and now currently working on BFPP IV.
Once again through collaboration and understanding of the consultant and the Project Owner, City of Toronto, the TOR were very clear that the use of SUE is one of the key elements in design considerations and project risk mitigation. The clear and precise language used in the TOR by City of Toronto allowed the Consultant, to formulate the required level of risk mitigation and engage a SUE Consultant to execute the work.
This project unlike the Rehabilitation STS has a considerable amount of Open-cut/Trenchless construction-installation of new and upsized infrastructure and did not have an option for rehabilitation although in some areas it might be a solution where applicable. The thought was to attempt to achieve QLB on the entire impact urban alignment of the project and utilize methods of less certainty (but lower cost) to achieve QLC and QLD on the open and greenspaces where the majority of the work would have minimal impact on utilities. Within specific areas that shaft location and large excavations would take place in these non-urban spaces higher QL levels of utility information were recommended and achieved at critical points.
The key focus on this project was the vast differences in road allowances and utility impact that the proposed design had and has to deal with. When planning a 7-m shaft for the Trenchless solution and the paved road right of way is only a few meters larger on some smaller residential streets, understanding the utility impact and locations is critical in all aspects of design. The impact of such a design on traffic flow, existing utility location or even coordination for relocation is high and decisions on shaft locations would be based on QL B findings. The locations of the actual shafts would be refined even further by targeted QL A locations in critical intersections of utilities that would conflict with the design and assessing the actual impact. The same process but on a larger scale for the larger roads and utility dense areas would be used in understanding the utility impact and necessary level of SUE investigations needed and to what QL.
The understanding and the collaboration between the design and SUE consultant is key to any successful project. Understanding that a paint mark on the ground or a line on survey is not a QL rather just a data point of known (if under the direct responsible charge of a licensed professional) or unknown origin (from a one-call or other reason) of the represented utility. The Utility QL assigned by the SUE consultant is a combination of the following as per the definition from the ASCE on quality levels.
Utility Quality Level: The value, assigned by the Professional, of a Utility Segment or subsurface Utility Feature that identifies the relative (non-quantifiable) uncertainty of a Utility Segment’s or subsurface Utility Feature’s existence and actual location to that of its documented location.
The value is judged and assigned on the source, precision, consistency, collection methods, and interpretation of the data put into context with information from other sources in the possession of the Professional at that point in time.
A Utility Quality Level is assigned to a Utility Segment or Utility Feature of an underground Utility for a specific project for a specific time period, usually until substantial project completion or the end of coverage of professional liability insurance.
In conclusion, working together as a collaborative team the SUE consultant and design consultant will allow for projects to be delivered with the utilities being front of mind and not just an afterthought to be dealt with later therefore causing delay and cost overruns. Dealing with utilities and the issues and impacts they cause to new infrastructure and rehabilitation projects is a key to the project flow and seamless execution from design to construction with an efficient ability to forecast budgets. Being able to project costs and avoid change orders allowing the construction proponent to accurately bid and quantify risk. The more information that is provided during design the less risk to the constructor causing an overall risk mitigation factor to all parties involved.
Daniel Jarvie, P.Eng, is a project manager and Ophir Wainer, B.Sc, is Canadian business development manager at T2 Utility Engineers.