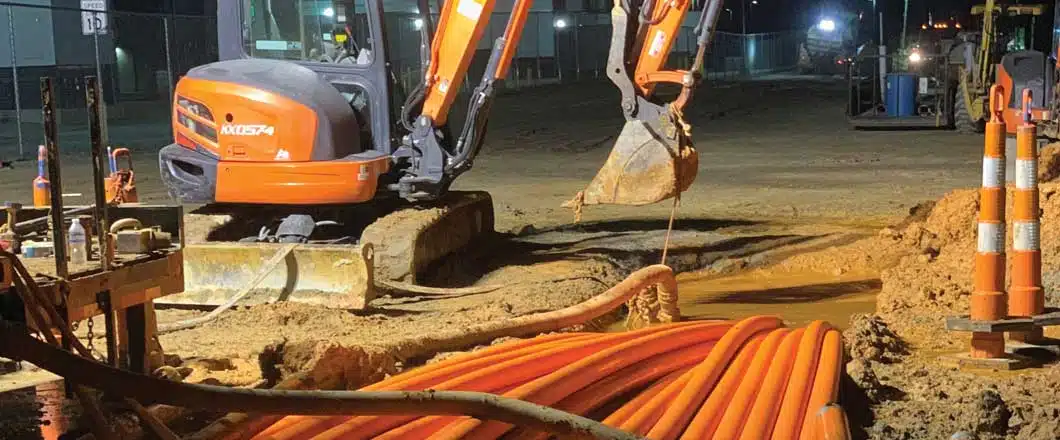
Record-number of Conduit Runs Pulled as Single Shot Using HDD
The underground installation of 24 runs of high-density polyethylene (HDPE) conduit pulled as one piece was named the Project of the Year by the Power & Communications Division of the Plastics Pipe Institute (PPI).
A total of 165,000 ft of 4-in. diameter, SDR 11 conduit was installed using horizontal directional drilling (HDD) to provide more capacity to an existing data center. The award was presented to PPI member company WL Plastics, the manufacturer of the conduit. PPI is the major North American trade association representing the plastic pipe industry. The association’s annual awards program recognizes projects and members for exceptional contributions to the industry.
Sections of 24 strands of conduit were pulled at the same time in 500 to 600-ft segments, and horizontal directionally drilled between manholes along the 7,000-ft-long path. The installation was planned and completed by Vision Directional Drilling Inc. , of Burlington, North Carolina.
“The customer needed a redundant pathway around their existing data center for fiber optic cable,” explained Vision Directional Drilling president Mark Hall. “There were a number of roads, culverts, creeks, steep inclines, ditches, security fencing plus existing underground utilities. And space to work in was limited. Originally, the project was designed for trenching, and we were able to come in and show them a considerable cost savings by using HDD and we alleviated most of the environmental impact issues. The end result was that we were also able to put it in much quicker and safer and with limited disruption.”
RELATED: HDD Under the Mississippi River
Founded in 1992, the company was started by Hall as Mark Hall Electric as a design build electrical contractor, and Vision Directional Drilling was created in 2006 to do all types of directional drilling with the majority of projects for communications, power, solar, water, sewer and geothermal, sports venues, pharmaceutical manufacturing firms, mining, data centers, FAA, aerospace, military/DOD and for the U.S. Army Corps of Engineers.
The crew used a Vermeer 80×100 with 80,000 lbs of pullback and a Ditch Witch JT60 that could provide 60,000 lbs of pullback with the conduit coming off the 1,250-ft reels. Both units were often used at the same time. “We would have one drill set up and then just hop scotch the drills back and forth. So, we’d have one drill working on one bore and then we’d have another crew taking the other drill and moving it to the next bore, setting it in place and having it ready to go,” Hall said.
The conduit was delivered to the site on a pre-determined schedule from a WL Plastics plant. “Using 1,250-ft reels made it possible for us to pull multiple runs off a reel,” Hall said. “There was very little left over at the end of the reel. We did not fuse any on the entire project.
“We had a couple bores where there was an elevation change of 70 ft was over 150 ft. The terrain and existing utilities didn’t matter because we calculate the bores from our lowest point to the exit point plus existing utility elevations to achieve our bore paths. And for the soil, we were in all different types of material. We encountered heavy swelling clay, running sand and rock.”
“This exceptional project shows how versatile HDPE conduit truly is,” stated Patrick Vibien, P.Eng., director of engineering of the PPI’s Power & Communications Division. “Bundling 24 individual sections of 4-in. diameter conduit and making about 10 pulls that each were hundreds of feet long, reduced cutting into the terrain, which reduced any environmental impact plus saved other underground utilities from being damaged by a backhoe, for example. Also, the HDPE conduit is a sustainable solution that will last for many generations. It offers unmatched corrosion and chemical resistance, is flexible, durable and strong, and is available in long coil lengths to reduce joints and installation time. HDPE conduit is available in a variety of sizes, colors, dimensions and lengths.”
Project Challenges
The challenge for Hall was the hilly, country topography. “What made the directional drilling better than trenching was the existing utilities and terrain,” he said. “This was an established data center. There are critical power and multiple carrier feeds into it plus fire lines, and storm drains. Because of the vehicular traffic and the security of the project, it was not an area suitable for trenching, which would have dug under the fences causing security issues and would damage the landscaping. We were able to do all this with zero damage to their existing utilities, landscaping or hard surfaces.
“Actually, figuring out how to put those twenty-four, 4-in. conduits together was not that hard.” Hall stated. “The biggest thing was being able to set up the equipment around the existing utilities and the areas that we had to work. When they originally came to us, to do it as directional drilling versus open trench, we had to figure out how long the runs could be, where we’d set and place the drills. We had several runs that went down through the woods and across creeks. We had to pick areas where we could place the drills. We were also drilling through rock on much of the project. Our customer was great to work with, and they were open to our suggestions on the design of the installation.”
The Vision crew took the conduit off the reel, laid out 24 pieces in a straight line and attached the pulling head. The resulting bundle was 28 in. in diameter, and a 36-in. diameter reamer was used.
“We wanted zero drag on our pulls,” Hall explained. “The tensile strength of that 4-in. SDR 11 HDPE conduit is 6,500 lbs, with a max combined pull rating of around 80,000 lbs.”
Depending on the type of soil, the Vision crew used Cetco HYDRAUL-EZ mud to achieve a viscosity of about 95 seconds, plus its Drill-Terge and Clay-Stop along with soda ash.
RELATED: Guidelines for Use of Compact HDD for Placement of HDPE Pipe in Municipal Applications
“We often had 18,000 lbs of pull or less,” Hall said. “There was zero stretch and we really just took our time to make sure that the mud design was just right. That’s every bit of directional drilling right there, to set up the drilling mud, and making sure all the calculations are right.
“If we do that, we can tell you what the pull is when we start to drag the pipe on the ground, we can tell what our drag pressure will be throughout the entire bore. We can actually mark it on the ground so the crew knows what the drag pressure is going to be at those marks. And I can tell you the range within about 2 to 3 percent all the way through the bore.”
According to Vibien, when pulling HDPE conduit into place, an increasing axial tensile load will be exerted on the conduit. “The amount of tensile load placed on the conduit during installation must be controlled and should not exceed the allowable values for each diameter and wall type. When done properly, there can still be a little elastic stretch that is completely recoverable, so a crew needs to be sure to leave some extra length out of the borehole and give it some time to recover before trimming it back.”
HDPE conduit that comes on reels retains a certain amount of memory, which makes it want to return to a coiled state.
“If you’re not careful, when pulling this many conduits, they will actually weave or braid itself together,” Hall explained. We over cut the hole enough that we had a safety margin for that. During the pull if the pipe gets in and starts weaving itself together, then you’ll end up losing pipes. They’ll crush and you’ll lose the inside diameter to it.”
To solve that, the crew laid out the conduit and managed each run of pipe to keep the pieces from braiding themselves together. Laying the pipe out on the ground prior to the pull helped overcame the memory effect and enabled the pull to go straight with all the conduit pieces in line. Hall said that during winter, when this data center project was done, it takes more time for SDR 11 HDPE conduit to lose its memory than when temperatures are warmer.
Hall said that all the planning and the focus on setting up paid dividends. “When we finished, we had to proof the inside diameter of each pipe, which was about 156,000 ft. We ran a mandrel through each strand. Every single foot that we put in the ground had to be tested and passed. And it did.”
Photos courtesy of Vision Directional Drilling
Steve Cooper is the managing director of SCA Communications.