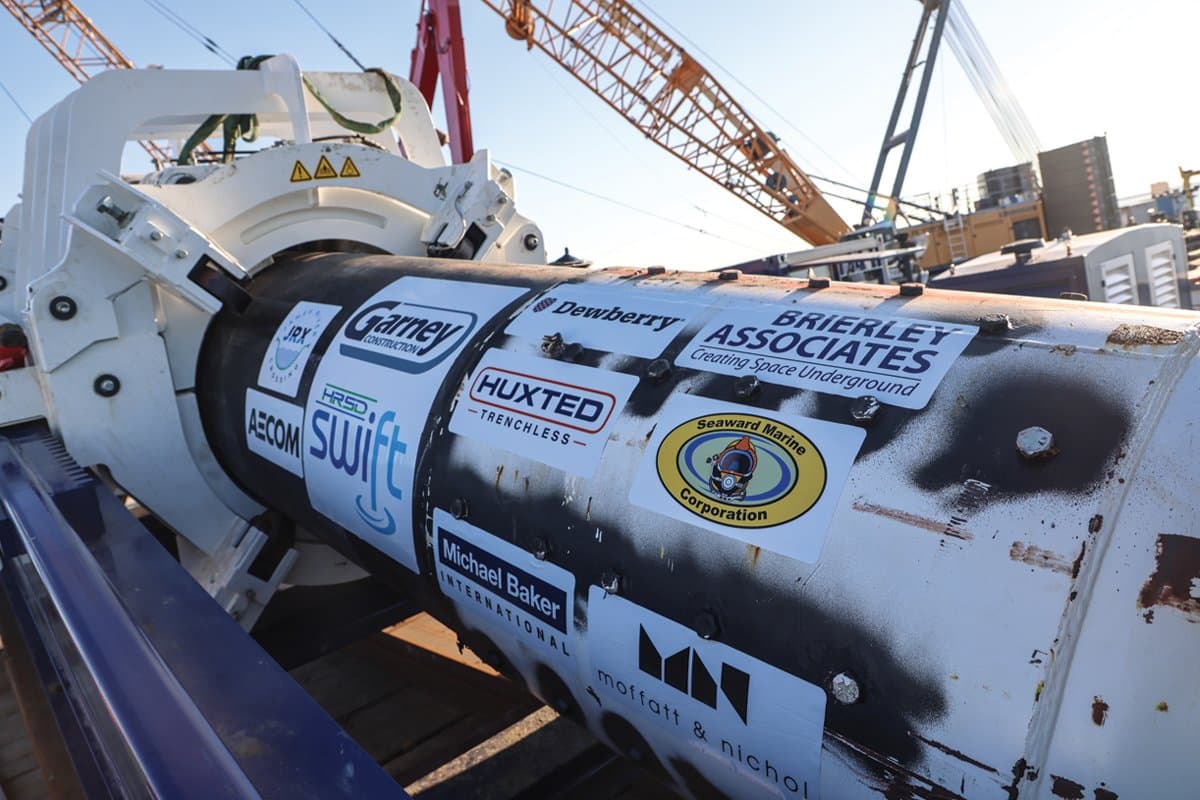
James River Crossing Sewage Force Main HDD Planning and Design
The James River Crossing (JRX) project is part of Hampton Roads Sanitation District (HRSD) Sustainable Water Initiative for Tomorrow (SWIFT) program.
A component of this program includes closure of the existing Boat Harbor Treatment Plant, construction of a new sewage pumping station, and a new sewage force main to convey sewage across the James River to the Nansemond Wastewater Treatment Facility.
JRX is being executed using a design-build (DB) delivery method that was awarded in April 2022 to the Garney/Dewberry design-build team.
This project includes designing, permitting, and installing a raw wastewater force main across the James River from Newport News to Suffolk. The total crossing is over 4.5 miles comprised of new HDPE pipe ranging in size from 42- to 54-in. diameter.
The project includes the installation of the new force main under the Newport News Shipping Channel and through a heavily used marine terminal. The basis for the DB request for proposal (RFP) was to perform a water-to-water HDD of approximately 3,200 LF using HDPE pipe under the channel. Early on, the team identified this HDD installation as one of the biggest project challenges.
Due to the criticality of the HDD, the team worked diligently to identify industry leaders with technical expertise, specialized equipment and project experience to perform this one-of-a-kind HDD. Huxted Trenchless and Brierley and Associates were brought onto the team as nationally recognized leaders in the trenchless industry.
The HDD crossed nearly 100 ft below the channel, at an elevation of -160 ft. The deep HDD geometry was necessitated by regional geology, with very soft clays overlying older loose to medium dense silty sands and fine sands. Advancing the HDD through these materials required careful steering and mud control.
HDD Planning
The length, diameter, geometry and geologic conditions of the HDD made this installation unique. Bridging documents were provided as part of the DB procurement to baseline an approach for the project. Those bridging documents included a 3,200 LF water to water HDD that would use two marine working platforms to install the pipeline under the Newport News Shipping Channel.
Evaluating the alternatives for the HDD, the team considered several different approaches. Including reducing the overall length and raising the bottom tangent as well as extending the drill to the shoreline to eliminate the need for a second working platform in the water.
Based on the assessment during the planning phase, eliminating the second working platform, reducing the amount of marine open cut installation, and extending the HDD to the shoreline would reduce the overall project costs by more than $10 million. However, this installation would push the limits of the industry and result in a record-breaking HDD for HDPE of this diameter and length.
Planning, designing, and constructing this record-breaking HDD required the DB team to address numerous key challenges that would result in a successful pullback.
HDD Design
Based on available information, the extremely soft soils, as sampled using the Standard Penetration Test, ranged in relative density from weight of rod (WOR) to single digit blow counts (termed N-blow counts) to an elevation of -100 ft resulted in subsurface conditions that constituted a highly challenging crossing – trying to keep the drilling fluids from migrating to the surface as inadvertent returns (IR) while maintaining a hole that could carry the cuttings to the surface and in turn not overstressing the plastic pipe.
Determining the geometry of the HDD and balancing maximum anticipated pull forces with the geologic conditions to confirm the installation would be within the limits of the HDPE product pipe was critical. In addition, mud handling procedures, borehole stability and duration of installation would complicate the installation and HDD model that the design team created.
To overcome these challenges, the team designed the HDD without a compound curve to reduce the anticipated pull forces. The extremely soft soils required the HDD to cross 100 ft below the bottom of the shipping channel, to -160 ft.
Entry and exit angles as well as bottom tangent radiuses were all designed to reduce pull forces to the greatest extent possible. However, the unknowns during design associated with borehole stability, final geometry and overall length of the increased the risk of excessive pull forces.
The tensile strength of the HDPE pipe was a major concern for the pullback. During the planning stages, mitigation methods were analyzed to help cut down the anticipated pull forces while pulling the 5,700 ft of HDPE into the drilled hole.
Therefore, a risk mitigation strategy was discussed to address challenges during installation if pull forces started to approach maximum allowable pull forces. The team decided that a pipe pusher specifically made for plastic pipes would be used to reduce overall pull forces, providing a push-pull installation.
The pipe pusher was installed on the 200-ft by 90-ft fixed working platform that was built in the river to provide up to 250,000 lbs of pushing capacity if needed.
Another key challenge was external loading on the HDPE pipe.
Due to the depth of the pipeline the external loading from soil and water depth was critical in determining the long-term stability of the pipeline. HDPE’s thermoplastic properties and dependence on time and temperature were key in determining the capacity of the pipeline to withstand external loads.
The unique geology under the river makes estimating soil loading, soil arching and overall load on the pipeline challenging. Additional geotechnical study was performed to better approximate soil angle of internal friction and determine the approximate soil arching that would be realized to decrease overall load on the pipe from full prism loading.
While initial conditions were within the short-term deflection and buckling conditions of the pipeline, the long-term deflection fell within a factor of safety the team was hesitant to accept. To mitigate this risk of pipeline deflection, two requirements for the pipeline were instituted.
The standard initial ovality of HDPE pipe from manufacturers is 5%. This industry standard is driven by equipment tolerances during the manufacturing process. Working closely with HDPE experts, our team reduced the initial ovality of the 42-in. pipeline to 3%. Limiting this initial ovality required close coordination with the pipe manufacturer and resulted in a long-term deflection within acceptable limits.
Due to the nature of the work, the pipeline is currently installed under the river and will not see operational pressures for over 15 months. Once the system is operational, normal operating pressure from the pump station will prevent deflection. However, during the 15-month construction period, there is a risk of deflection occurring even with internal hydrostatic pressure maintained in the pipeline.
Therefore, the team is re-pressurizing the pipeline every 30 days and maintaining that pressure for a minimum of 48 hours, to leverage the thermoelastic properties of HDPE and reset the modulus of the pipeline.
Working in a river poses unique risks associated with hydraulic fracturing of the geology and release of mud into the environment. Due to the extremely soft soils, the containment of drilling fluid required the use of steel conductor casings installed into suitable geologic formations to prevent this frac out.
A 66-in. diameter steel conductor casing made of 0.75-in. thick high strength steel was installed on both the north shore and south platform to capture drilling fluid.
On the north shore, the casing was installed in an excavation over 300 ft to an elevation of -70 ft and on the south platform in the river the casing was installed 600 ft to an elevation of -100 ft through the water resting on 30-in. diameter pilings that acted as goal post support for the casing.
These conductor casings handled all the drilling fluid and cuttings for recycling and disposal.
Construction for the HDD portion of the project started in August 2023 with the installation of piles for the temporary work platform based offshore. After the platform was constructed and the land area was prepared, the conductor casings were installed, and the drill equipment was mobilized to the site.
The actual pipe pull started on May 1, 2024, and continued uninterrupted until the early evening of May 2. In the following days, after a 24-hour period of relaxation, the pullhead was removed and testing flanges attached on each end. The pipe was successfully pressure tested and a sizing pig was sent through the pipe with zero anomalies in the ovality.
Paul Longo, P.E., is senior associate and senior project manager of the water market segment at Dewberry. Dave Sackett is chief operations officer at Brierley Associates.