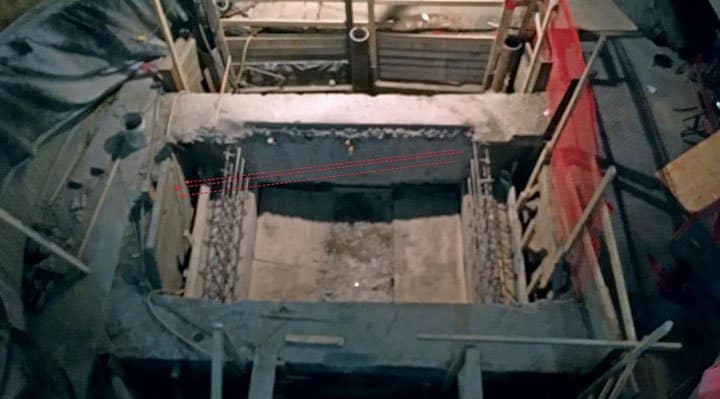
Pipe Ramming: Sometimes Bigger Isn’t Better
Over the years we have been lucky to have a wide assortment of interesting pipe ramming projects and driven thousands of linear feet of pipe into the ground. The typical projects tend to be large diameter steel casings installations under roads, railway tracks or watercourses.
As practitioners always know, these projects always have their challenges just by their very nature. However, every once in awhile, a small construction project comes along with a unique set of challenges that makes you nervous for the success of the operation; the type of project where information about obstacles in your way are scarce and potentially inaccurate.
Trenchless technology practitioners are always balancing the merits of the trenchless tools we have in our roster against the required project tasks. We know from experience the strengths and limitations of the big jack and bore machines, TBMs and microtunneling machines, but to some extent pipe ramming presents a different set of challenges. It is a brute force blunt instrument. It’s not steerable and can be hard to calculate the force required to push a large diameter casing through certain types of soil conditions.
RELATED: Pipe Ramming Across Mud Creek in Ontario
In some respects, it is easier to be more confident when you are using a large pipe rammer like a Taurus 24-in. tool or larger just because the extra force can help. However, there are times you have no working room to set up a large hammer or casing and you have to rely on a smaller tool. This is the situation we found ourselves in this past spring on a project to install an elevators power and hydraulic lines in Ottawa, Ontario.
The scope of work originally included just micropiles work to support elevator installations but a project challenge reared its head in the form of how to get the hydraulic and electrical lines into the mechanical room 40 ft away from the elevator pit – without the pipes being visible to the public as they took the elevator from ground level to departure tunnel.
Many designs were proposed but they were refused on feasibility and aesthetic grounds. The general contractor was left scratching his head about a possible solution and came to us with horizontal directional drilling (HDD) in mind. Unfortunately, the setup and long drilling length in combination with foundation structure unknowns made achieving the proper HDD alignment and depth cost-prohibitive and unpredictable in outcome. The idea was quickly dismissed.
RELATED: The Unexpected: Boulders Burden Ottawa Pipe Ramming Project
After some discussion with the stakeholders, it was decided that small diameter pipe ramming was the only viable solution to get access to and from the mechanical room in the small working area. The challenge was that the 7-in. casings needed to be rammed under a series of deep footings supporting the ramp walls and escalator and between support piles. The target window between the piles was 24 in. and that was more than 20 ft away from the start of the ram.
Site measurements were made and we started to put the project plan together with any information we could gather from old site plans. It was decided that the rams would have to be stacked in a triangle formation- giving us a few inches of clearance between the support piles and foundation bases. We had to assume the 1960-era as-built plans were accurate. There was no way to confirm.
There were enough question marks that even as ram work plans were being designed, the start date was delayed while the project teams investigated other potential solutions with the stakeholders. The building is a designated heritage site and could not be readily changed or modified to suit other design solutions and in the end all other options were put aside.
We started assembling the ramming tools. The limited workspace and physical obstacles made the choice of hammers slim. In the end, we modified a 5.5-in. earth tool to ram the pipe. We had no space to use anything bigger but we knew it would have enough force to push the casing a short distance in soft ground. We welded up a casing adapter to fit the threaded casing and act as a push ring. The 5-ft long casing sections were threaded to speed up operations. The cradle for the hammer and casing was set to a 7-degree slope, which would bring the exit pit to a depth of approximate 7.5 ft at the 40-ft mark. Adding to the physical challenge was the fact that this basement mechanical room exit pit would also be under at least 6 ft of groundwater pressure and running sands.
Once all the hoses and tools were set up, the hammer was started up. The first 10 ft of pipe was buried in about 50 minutes. Seemed encouraging. Then the hammer started to labor. The next 1 in. took three hours.
RELATED: Tapping Partners’ Expertise Critical to Success of HDD Project
We had concerns.
We knew it could be any number of obstacles. It could have been the foundations or we might have missed the small window and hit the piers? We outstripped the hammers capacity to overcome hydrolock.
Sometimes a pipe casing can get caught by water suction and just outstrips the hammer force. We did ram trajectory measurements to try and figure out what the casing might be hitting under the slab and identify the trouble spots we had encountered. We knew there wasn’t a plan B or C on the horizon. We started up the hammer again and after an hour of no advancement, the pipe rammer changed its frequency and the casing pipe started advancing at its original starting rate of 5 ft rate.
At 20 ft in, the pipe stopped advancing normally and was back to 1 in. in four hours. This was the lower pipe of the three in triangle formation. If we were having this much initial trouble in the lower pipe, what would the top pipe in the formation be like to advance? We tried multiple compressor pressures but nothing seemed to make a difference. Again, out of the blue, the pipe rammer stopped laboring and the casing started to advance normally. The challenge was that there was no room to maneuver outside the target window of the ram.
We were confident that we could relieve the pressure in the pipe some way. We modified a large Hilti 250 electric portable drill to run AW drill rods to clean out the casing and relieve pressure should the need arise. Once we made the first 40 ft, we knew that the goal was at least achievable. Typical of ramming projects, the constant hammering was tough on pipe and all the tools. We broke the casing adapter several times during the course of the operation and it had to be re-welded and reinforced. The last two pipe runs followed the same advancement pattern, 5 ft in 30 minutes dropping to 1 in. in three hours but, in the end, all the casing reached their required distance and were located in the exit area using a locator and sonde.
The rest of the operation was dull in comparison. The casing was cleaned out using our modified electric drill and mini auger.
The project was successful overall but it was one of those small projects that could have gone either way. The financial impact could have been significantly negative for all parties involved because there were no other acceptable solution options open to us. Not to mention damage to reputation.
We knew we would find a solution, but it might not have been easy for all the stakeholders. At the end of the day, no trenchless practitioner wants to rely on good luck or fate to remain unscathed but in some case it often feels like it boils down to just that. One can do all the due diligence in the world and plan every step precisely but it can still backfire. Given the challenges and outcome on this project. We should by a lottery ticket.
Andrew McPhedran is vice president of business development at Marathon Drilling.