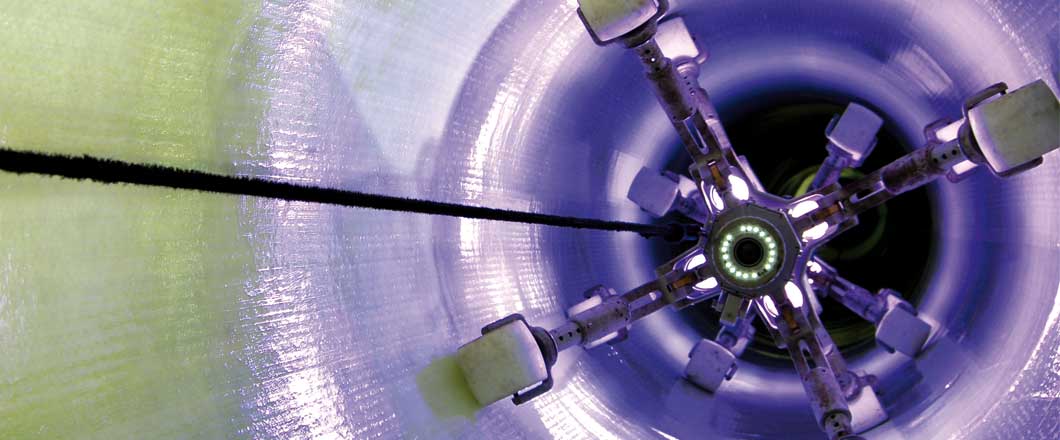
Light Bright: Ultraviolet Curing Continues to Make Inroads in the CIPP Market
While the cured-in-place pipe (CIPP) market continues to hum along as the premier rehabilitation method for our deteriorating and aging underground infrastructure, one segment of the CIPP market has yet to attract that same expansive audience in the United States.
But its manufacturers and advocates continue to project a bright future for ultraviolet (UV) CIPP, as more and more system owners and engineers understand the curing method’s benefits.
Introduction of UV CIPP goes back more than 30 years when inventor Thomas Reutemann in Germany patented and introduced the technology to the trenchless world. While Europe was quick to accept and utilize the new UV curing technology, the United States, well, not so much. UV’s acceptance and usage has slowly made gains over the last decade or so but remains well behind the amount of work being done in Europe.
While UV curing has been routinely called the “next big thing” in the CIPP world over the years, it has yet to make that monumental leap in usage by systems owners and engineers. Slow and steady progress has been made but UV curing continues to lag behind its heat-cured competition.
Even with that said, the UV CIPP community remains optimistic and solidified in the technology’s place on CIPP projects now and going forward. There are strong projections for this technology going forward and more and more companies offering the UV option for CIPP projects. We spoke with several UV CIPP companies to gain perspective and insight into the UV niche of the CIPP community, asking about the technology strengths and weaknesses, as well as its future and what holds it back.
While everyone we spoke with notes the popularity of the UV curing technology in Europe, they also point out that growth in the United States, though making inroads, still lags at 5 to 10 percent usage vs. traditional CIPP curing methods. Even with that low percentage, UV CIPP is gaining traction, they say — a steady and growing traction.
“The market on a global level is growing,” says Geno Camali, CEO of I.S.T. Innovative Sewer Technologies. “Europe is over 80 percent UV and China is now seeing a huge growth to over 20 percent of UV and vastly growing. The U.S. market is just starting to get traction with about 5 percent of CIPP being UV [cured].”
“Today’s UV CIPP market in North America is small, encompassing less than 10 percent of the overall market,” says Ian Lancaster, senior vice president of infrastructure solutions at Aegion Corp. “The market is experiencing small, steady growth, mainly due to the contracting community embracing the technology, as well as agencies recognizing the benefits in certain types of medium- and large-diameter pipeline applications. The European market vastly differs from the North American market since UV CIPP has been more widely adopted and accepted by the local agencies and contractors. Because of this early penetration, the European market is flat since it is fully saturated.”
RELATED: Seeing the Light – SAERTEX multiCom Continues to Grow along with the UV CIPP Market
Granite Inliner director of business development Jason Walborn points to the long process of educating engineers and system owners about the UV technology as part of the reason why the U.S. is slow to embrace the UV curing method. “In the U.S., the UV market is continuing to grow at a point in which it should have years ago,” he says. “After a long process of educating system owners and the consulting engineering community, UV is finally getting the recognition it deserves as a valuable alternative — not a low-cost alternative — to traditional heat-cured CIPP.”
Reline America vice president Tim Cook attributes increased interest and use of UV curing to the availability of curing information for engineers and owners. “Education and better understanding on the part of engineers and the end users regarding the advantages that UV glass fiber-reinforced plastics (GRP) brings to CIPP. This has led to an increase in UV specified projects.”
RELATED: Reline America – Changing the Face of Pipe Relining in North America
What Is UV CIPP?
How does UV curing work in a CIPP project? It’s pretty simple when you think about it: UV CIPP is an adaptation of the traditional CIPP and uses ultraviolet light to cure the resin inside the liner instead of heat with water or steam. The process has other differences. For one, a glass-reinforced liner is installed using a winch and the pull-in-place method vs. the inversion method. Using CCTV, the pipe is inspected to make sure there are not wrinkles in the liner. The crew then pulls a UV light train through the pipe to cure the liner at a predetermined rate.
The equipment involved with UV curing vs. heat curing is a bit different. The liners are composed of glass layers with a series of foils and barriers that together form a dual-sided, fully encapsulated liner. To feed the liner into the pipe, UV CIPP installers require a truck with a conveyor unit, explains Walborn, adding that a telescoping boom winch is positioned at the other end to pull the liner into place.
“Companies also need equipment to inflate the resin-impregnated tube with air pressure and a curing system comprised of a light curing train, sized for the diameter of the pipe with an onboard CCTV camera for pre-cure inspection,” he says. “The equipment requires a computer-monitored system to ensure proper light exposure to the circumference of the tube while the light train travels through the pipe.”
Camali notes that because the UV cure system controls all aspects of curing the liner, the crew needs to be fully trained by both the UV cure system manufacturer and the UV liner manufacturer. “The training can be done in [a few] weeks but it is recommended that the crew be familiar with conventional lining,” he adds.
UV Benefits
While both UV and heat get the CIPP job done, there are benefits to using UV vs. heat. These benefits include environmental and its flexibility, as well as the capability to use CIPP to reline pressure pipes. Lancaster puts it pretty succinctly: “There are generally four reasons UV CIPP is attractive: a smaller overall footprint, reduced emissions, enhanced physical properties (if glass is utilized) and continuous cure cycling monitoring.”
RELATED: A Hole in One – Bypassing Without Pumps in West Palm Beach
UV’s low environmental impact is what its advocates tout the most, noting that with UV curing there is no release of styrene — a primary ingredient found in some conventional resins — into the air or groundwater, which has made headlines in recent years with conventional curing. With UV, styrene is encapsulated and locked into place during the curing process. The UV market will grow as more users look for a non-emitting rehab solution, our group says.
“UV CIPP requires minimal energy and water during the curing process,” Walborn says. “An additional environmental benefit [is that the] UV liners utilize an engineered, polymeric film to serve as a styrene barrier. This helps encapsulate the resin for greater control in environmentally sensitive areas, stormwater and combined sewer systems.”
Camali and Walborn add that the UV liner’s shelf life is a big bonus. “Unlike conventional felt liner, [UV liner] can be placed in room temperature and stay for a year,” Camali explains, noting, “As a contractor, you can order a crate of liner and only cut what you need rather than having to figure out a wet-out request.”
There are some drawbacks with the UV curing method, the group notes. Chief among them is the size limitations available, typically no more than 72 in. vs. up to 120 in. for conventional curing. “Currently, the largest pipe UV can be used on is a 72-in. diameter [pipe],” Cook says, noting manufacturers are working to increase the size available.
“UV CIPP’s biggest weakness is the overall cost profile of the installed product,” Lancaster says. “This is directly due to the increased material costs (particularly the resin and glass), as well as the decreased production rates associated with the installation of the liner.”
But evolution of the market and technology continues. UV curing is a vital component in the CIPP toolbox with a strong future ahead, advocates say. Camali has an ambitious projection that the use of UV curing will grow to more than 80 percent of the market as engineers and owners gain better understanding of the technology and its benefits and it becomes more cost-friendly. Some have a more reserved outlook.
Walborn doesn’t necessarily see UV curing eclipsing heat curing. “UV CIPP isn’t intended as a replacement to heat-cured CIPP,” he says. “Sure, it has some attractive properties — environmental, physical strength, pressure pipe — but its place in the market is complementary to the heat-cured CIPP that everyone knows. It’s another tool in the toolbox.
“While there will always be a market for heat-cured CIPP, the market share for UV products is on the rise,” Walborn says.
Whichever the case, all agree that the technology used will continue to get more advanced, pushing this curing method forward. Lancaster says the introduction of the LED technology, as well as the use of highly translucent felt materials in lieu of the more expensive glass material, has made UV curing a stronger option.
“The availability of larger diameter pipe liners has grown, liners have much greater e-modulus strength, UV curing equipment has improved with more intense UV output, resulting in thicker and larger diameter pipe liners being able to be made and has reduced the amount of time needed to cure a liner,” Cook says.
“The first UV system only had a knob to turn the bulb on and an amp meter,” Camali says. “Now we have temperature sensors throughout the cores, position sensors, stronger bulbs, automated software to run inflation, light train initiation and deactivation and multiple cameras.”
Longer curing lengths and diameters are also in the UV future, they say.
Sharon M. Bueno is managing editor of Trenchless Technology.