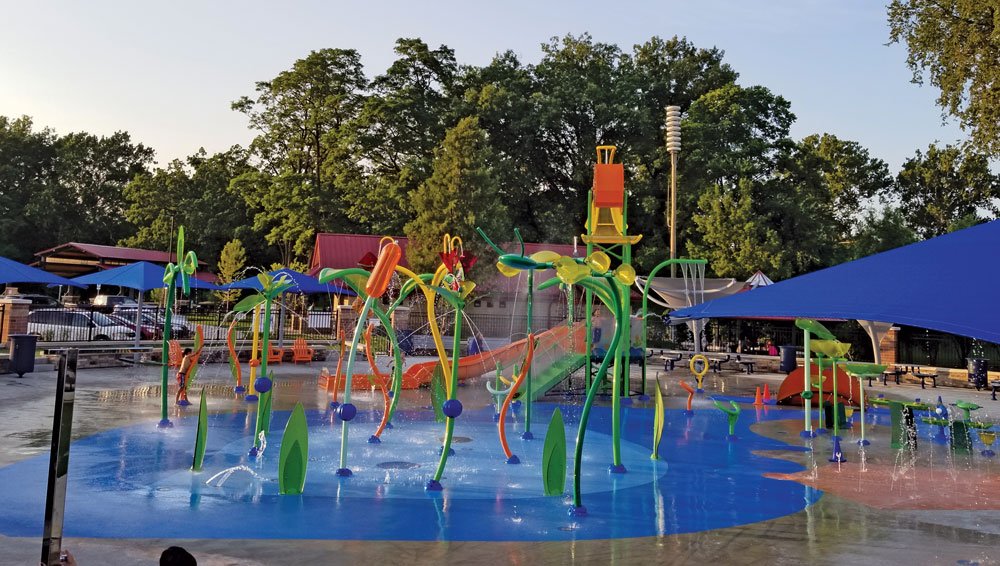
Lateral Lining Saves Water and Summertime Fun
The City of Sterling Heights, a suburb of Detroit, Michigan — population 132,000 — has undertaken what it calls The Recreating Recreation initiative to leverage existing natural resource assets to create a City that provides its residents with year-round recreational opportunities. One of those initiatives, an outdoor splash pad, or water park, opened earlier this summer with great excitement from the City’s residents.
The splash pad was built on a closed-loop system, meaning that the water flows through the sprinklers, is looped back to be filtered, and is then redistributed through the sprinklers where the cycle continues. Shortly after the opening of this popular attraction, City officials recognized that the splash pad was losing an estimated 8,000 gallons of water every day. While some depletion of water is to be expected via naturally-occurring evaporation and by residents cooling off and enjoying the summer activities, this amount was extreme. To protect its natural resources the City took immediate action.
RELATED: CIPP Solution for Major Soft Drink Bottling Plant’s Complex System
City officials called on Corby Energy Services Inc., a Detroit-area contractor, to assess and quickly address the excessive loss of water and dirt that was leaching in to the system. Corby Energy completed an initial televising and investigation of the 10-in. return drain. After review, it was determined that the pipe could not be repaired by excavation, as the return line was under the newly poured concrete pad. With a specialty in the construction and rehabilitation of mainline systems using the cured-in-place (CIPP) method, Corby Energy project manager Josh Freeman realized this project was unique because there was only one point of access to the pipe. He determined that a “lateral blind shot” was needed in order to rehabilitate the failed water line and he needed to partner with another group to tackle the rehabilitation of this unusual project. He called MaxLiner USA technical services manager Chad Miller for a recommendation.
Corby Energy project manager Josh Freeman realized this project was unique because there was only one point of access to the pipe. He determined that a “lateral blind shot” was needed in order to rehabilitate the failed water line.
“It was clear to me that this job had to be done quickly, and during a time that was non-disruptive to the operation of the water park,” said Miller. “Using CIPP technology for this job was a good call by Corby Energy Services because it allowed the contractor to get in to do the work overnight when the splash pad was closed down, minimizing disruption and allowing the City to open the facility up the following morning.”
Miller and Freeman reached out to a familiar partner and local contractor, John Curtis, from InnovaLiner Inc., located just across the Michigan border in Monclova, Ohio. “This was truly a team effort,” continued Miller. “The work had to be done fast and the high-exposure location made a quality installation critical, so the InnovaLiner and Corby crews came to the jobsite packing all of the equipment and materials they needed. This included the camera, liner, resin, clear calibration tube and heater to cure the liner. I live in Michigan about an hour north of the jobsite, so I took this opportunity to provide the InnovaLiner crew with some additional on-site training. I loaded up my truck with the MaxLinerGun and was there with the crew around 7:30 p.m., on stand-by until the park closed at 9 p.m. and we could begin the work.”
The aluminum MaxLinerGun is a compact inversion unit for lining 2- to 12-in. diameter pipes and is best suited for residential and industrial drains in horizontal or vertical applications.
“I knew the MaxLiner system was well-suited to easily transport in tight spaces, but this job really showed me how well it maneuvers to get from one location to the next with minimal disruption,” said Freeman. “It’s great to see how mainline and lateral CIPP methods can be utilized together in completing a complex project.”
RELATED: Pipe Relining Market Overview: CIPP Still the Relining Leader
The challenging project included relining 70 ft of pipe with 10-in. liner, much of which was shot uphill. The lines also included multiple 45-degree bends, which meant that great care had to be taken to avoid wrinkling, which would have impeded water flow. “We worked with Corby Energy and InnovaLiner to select the best materials for this job based on these unique characteristics,” continued Miller. “We recommended the 4.5-mm Max SuperFlex, a non-woven needled punched PE felt liner, which is bonded to an impermeable PU coating with a special stitched seam. This single-layer liner is highly flexible and is capable of navigating multiple bends up to 90 degrees, as well as transitions. We knew this would work well for this application.”
“We were a bit nervous going in because of the size of the lines and the bends we had to navigate,” said Curtis. “But the results using the Max SuperFlex were awesome – the liner finished with minimal wrinkling in the bends, with nothing that would impede flow in the short- or long-term. Having Chad onsite to support us was also incredibly helpful. Our crews learned so much and will have a higher level of confidence for future projects like this. Chad also increased our comfort level in inverting the recirculation hose inside of the Max CalTube for the hot water cure. One of the greatest learning curves for us, however, was the vast selection of liner types offered by MaxLiner for different applications.” “This project was a true example of how great partnerships come together to complete projects successfully”, said Josh Freeman of Corby Energy.
By 6 a.m. the next day the lines were rehabilitated, the water was recirculating, and the crew was nowhere in sight, allowing the splash pad to reopen to the public for many years of future enjoyment.
Heidi O’Leska is director of account services at Campbell MacGregor.