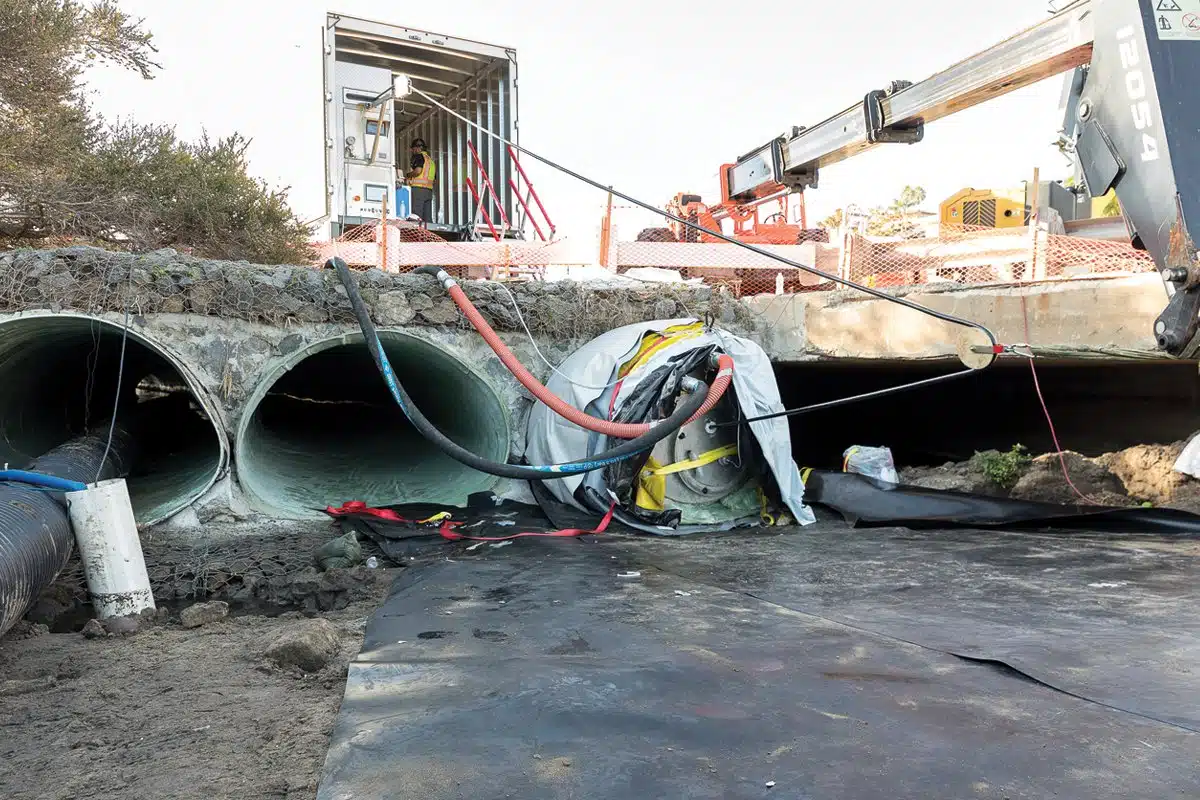
2024 Trenchless Technology Project of the Year Rehabilitation Runner Up – Moonlight Beach Triple 72-in. CMP UV-CIPP Rehabilitation Project
As part of its annual storm drain management program the City of Encinitas, California, identified a trio of pipes at Moonlight State Beach that were in need of repair.
Moonlight Beach is situated on the coast of the City of Encinitas in San Diego County.
The three culverts convey stormwater underneath a heavily trafficked beachfront pedestrian thoroughfare which connects a residential area to a popular section of beach with recreational amenities such as beach volleyball courts and picnic tables.
The culvert inlets receive flow from the Cottonwood Creek that runs alongside a road (which dead-ends as it approaches the beachfront), and the outlets are at the shoreline, expelling the water into the ocean.
The corrugated metal pipe (CMP)culverts were in a state of significant deterioration. Saltwater corrosion is a factor given the interface with the ocean, and the outlet ends are half submerged during high tide. Efforts had been made to shore up the pipes with a cementitious coating but even this was already beginning to corrode, especially at the inverts, and a long-term solution was required.
The Moonlight Beach Barrels and Storm Water Repairs project consists of the point repairs and lining of the three existing 72-in. CMP culverts that connect Cottonwood Creek with the Pacific Ocean. This project also included repairs to the south channel bank of Cottonwood Creek upstream of the metal storm water pipes.
The trenchless portion of the work involves the lining – via ultraviolet cured-in-place pipe (UV CIPP) – to restore the three parallel 285 ft long, 72-in. nominal diameter pipe arch CMP stormwater culverts with gradual bends.
The City of Encinitas collaborated with consultants RICK Engineering Co. and Kleinfelder for the design; the trenchless subcontractor Performance Pipeline Technologies carried out the prep and lining work with onsite assistance from UV GRP liner manufacturer IMPREG and UV curing system provider ProKASRO.
The liners were designed for host pipe condition III, and a wall thickness of 13.7 mm was specified in accordance with the ASTM standard calculations given the fiberglass liner structural properties. A vinyl-ester resin was chosen for enhanced corrosion resistance. After extensive planning and prep work, UV CIPP lining was completed over the course of three days in December 2023.
Why This Project Is Outstanding
This rehabilitation – as of the June 2024 submission deadline – is the the largest single-site large diameter UV CIPP installation by cumulative size ever undertaken. With 855 total linear feet of 72-in. diameter liner at 13.7 mm wall thickness, the weight of each liner exceeded 30,000 lbs.
This project required unusually intensive pipe cleaning and preparation. High tides deposit an immense amount of sand and ocean detritus in the pipes through the ocean-facing outlets, and all of this needed to be removed both for the initial measurement gathering for the liner design, and for the actual lining stage.
Given the size, shape, and state of deterioration of the host pipes, most of this was accomplished manually with shovels and wheelbarrows by the crew. Due to the partially eaten away cement coating, precise circumference measurements were taken at 5 m intervals so the liner could be appropriately sized to account for the variance.
The jobsite staging logistics were extraordinary given the size and weight of the liners, the proximity to the recreation area, the sensitivity of the coastal environment, and the necessity of coordinating the installation to coincide with both dry weather and low tide.
The inlet area connecting to the existing stormwater channel was graded to create a level space for the 15-plus ton liner boxes to be lowered by crane, and the displaced soil was used to create a coffer dam.
Only dry weather flow levels from the channel would be possible to divert, by being redirected through one of other culverts with HDPE pipe before a given culvert was lined. Water levels at high tide would have washed out resins and made lining impossible, so the crew had a finite window of low tide conditions for each installation.
The size of the liners demanded the highest UV-curing wattage available in the United States, in the form of a three times ‘jumbo core’ light train, each core having six 2,000-watt bulbs for a total of 36,000 watts of curing power.
Due to the pipe arch profile, a ball gear set designed to position the curing bulbs optimally for the shape was attached to the light train legs. A removable airlock was required during the introduction of the light train, as any loss of pressure that could lead to sagging of the immensely heavy liner could damage the light train.
Each rehabilitated culvert became operational immediately after the liner ends were cut off after the cure. Since the project was completed, the engineering department of the City of Encinitas has documented the liners’ success.
Mike Kezdi is managing editor of Trenchless Technology.