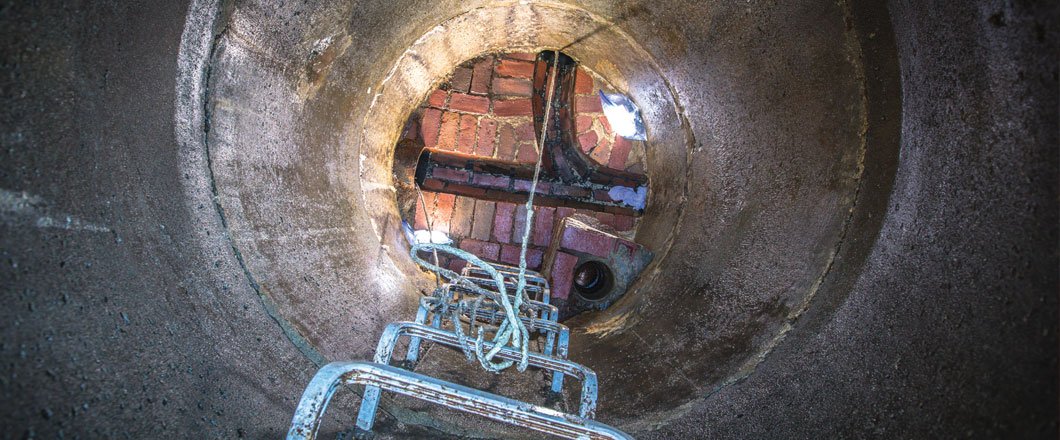
Inspection Reveals Proven Results for Manhole Rehab with Epoxy Coatings
As the nation’s sewer collection systems continue to age, the manhole rehab industry has matured and become common practice. Many cities have taken a progressive approach and repair hundreds of manholes per year. Overtime, the solutions deployed by these municipalities have and will continue to prove their value.
Most sewer corrosion is caused by Microbial-Induced-Corrosion (MIC), a condition in which harmful bacteria thrive and create a corrosive environment. Typically, manholes are made from either concrete or brick and mortar. Both concrete and brick mortar share cement as a common ingredient. Porous cementitious surfaces are an ideal biome for anaerobic thiobacillus bacteria to establish colonies where they consume trapped sulfates and produce H2S gas. The H2S gas accumulates in the non-liquid filled spaces within the system where it finds its way to autotrophic bacteria that then convert the gas to sulfuric acid that wreaks havoc on the manhole structures. The need to mitigate MIC has led to the rapid innovation and expansion of the sewer rehabilitation industry over the last 50 years. Many technologies and manufacturers have come and gone leading up to today’s fast-moving industry in which there are more choices than ever before when addressing manhole rehabilitation. Owners and specifying engineers are faced with the challenge of balancing cost, functionality, longevity, and safety when vetting out the right method and product.
Warren’s commitment to excellence is demonstrated through our inspection and testing process. Upon completion, each manhole undergoes a spark and adhesion test.
One option that has gained a significant following over the past 30 years is 100 percent solids epoxy coatings. Epoxy coatings may be used to structurally rehabilitate and protect assets in a single application. The epoxy works by conforming and tightly adhering to the rough surface of concrete or brick and mortar occupying the bacteria’s habitat and forming an impassable barrier of protection. Epoxies capable of high build (¼ to ½ in.) in a single coat may even be used to structurally repair or enhance their host eliminating the need for costly replacements. The use of epoxy coatings for rehabilitation is a cost-effective solution that promises decades of performance with little disruption or downtime to operations.
There exists a wide array of epoxy products available for purchase from a long list of manufacturers. Each epoxy product has a unique intended use. Some epoxies are strong and rigid, while others are flexible and elastic. As time passes, certain epoxy systems are differentiating themselves as high-performance options due to proven effectiveness years after initial application. Warren Environmental’s 100 percent solids epoxy system is one such example, with coatings that were installed in the company’s first year (1996) still in service protecting manhole substrates from corrosion by any means. Warren’s epoxy coating provides a monolithic system that ties the mainline into the manholes resulting in a 100 percent reduction in inflow and infiltration (I&I). Warren Environmental has been a trusted name in the epoxy industry for 24 years. Its products have been used to rehabilitate more than 200,000 manholes throughout the country, each potentially stopping thousands of gallons of infiltrating water from entering sewer systems, consequently reducing operation costs by up to $20,000 per manhole annually.
RELATED: Surface Preparation — a Fundamental Necessity for Manhole Rehabilitation
Lining the invert channel is an essential part of Warren’s manhole rehabilitation process as infiltration often occurs below the flow line.
A great example of the Warren Environmental system’s effectiveness is with the sanitary sewer restoration project for DeKalb County, Georgia’s Department of Public Works. Since DeKalb County’s inception in 1822, there has been substantial population growth. As county officials kept up with new construction, they also made it a priority to maintain the existing sewerage infrastructure. The system consists of nearly 2,700 miles of sanitary sewer pipelines ranging from 8 to 30 in. and 700,000 manholes made of either brick or concrete. Portions of the system were experiencing substantial inflow and infiltration problems as a result of leaks and root intrusions. The concrete pipes and manholes were suffering from severe corrosion damage.
The Water and Sewer Division selected Warren Environmental’s epoxy coating to rehabilitate failing portions of the sewer system. Warren’s system was selected based on tests done in the early 1990s. Out of six methods tested, the Warren system was one of the two that met the performance criteria established by the county. Additionally, Warren’s sample manhole was tested seven years later. It was found to be in excellent condition with no loss of integrity and no leaks.
Throughout the program, Warren’s epoxy products were used in the county’s most aggressive environments, high level of hydrogen sulfide, and low pH where typical where the epoxy was to be installed. Over a 10-year span, approximately 900 manholes were rehabilitated using Warren’s epoxy system and have prevented potentially billions of gallons of groundwater from entering the sewer system.
RELATED: San Francisco Embarks on Stormwater Rehab Project
Manhole #1 during the 19-year inspection. Test dollies installed in preparation for adhesion test.
A handful of the first manholes coated were inspected 19 years later, in September 2019. Mystic Consulting and Inspection Services conducted a visual inspection, cleaning, sounding for dis-bondment, and adhesion tests. The goal of the inspection was to do a full condition assessment on the coating by determining if it had worn away, been damaged by MIC, developed pinholes, disbanded from the substrate, or deteriorated in any way. The results were tremendous.
The epoxy coating was found to be in excellent condition. The pull tests provided results of 910 PSI with the adhesion test glue between the dollie and the epoxy failing instead of the coating. This implies that the epoxy and the substrate were bonded or adhered to adhesion strength higher than the force that caused the test glue to fail.
“The Warren epoxy coating has held up well considering what has happened in these manholes since the coating was applied approximately 19 years ago,” said NACE inspector Jerry Clemmer, P.E.
Warren’s product is estimated to offer more than 75 years of additional service life to assets in highly corrosive sewer conditions (third-party testing performed by the University of Pittsburgh). The DeKalb County, Georgia, manholes are a testament to the Pittsburgh testing and show how successful and cost-effective Warren’s system can be.
RELATED: Epoxy Coating Provides Less Impacts, Risk for Second Creek Trunkline Rehabilitation
Other factors that are differentiating epoxy products in the market for manhole rehabilitation include high-build capabilities. Depending on the severity of the deterioration, high thicknesses may be required for structural repair of the asset. Some epoxy products can achieve builds above 500 mils (½ in.); however, they require multiple layers or underlayment. Multiple layers increase the owner’s risk of inter-coat delamination between layers, which is a leading cause of coatings failure throughout the broader coatings industry. Warren Environmental’s epoxy system is capable of being sprayed up to 500 mils (½ in.) in a single, times-saving coat. This is well more than what is needed for most structural rehabilitations. This attribute eliminates the risk of multiple coats while providing structural enhancement required for manhole repairs.
Choosing the appropriate material and technique for rehabilitation is vital to extending the life of the manhole, as well as ensuring cost efficiency. The selected method should provide the desired long-term solution to the problem. Epoxy coating is a viable solution that municipalities need to consider. However, investigating case histories demonstrating long-term, proven results is an essential part of determining the best system for your project.
Phil Warren is technical manager at Warren Environmental.