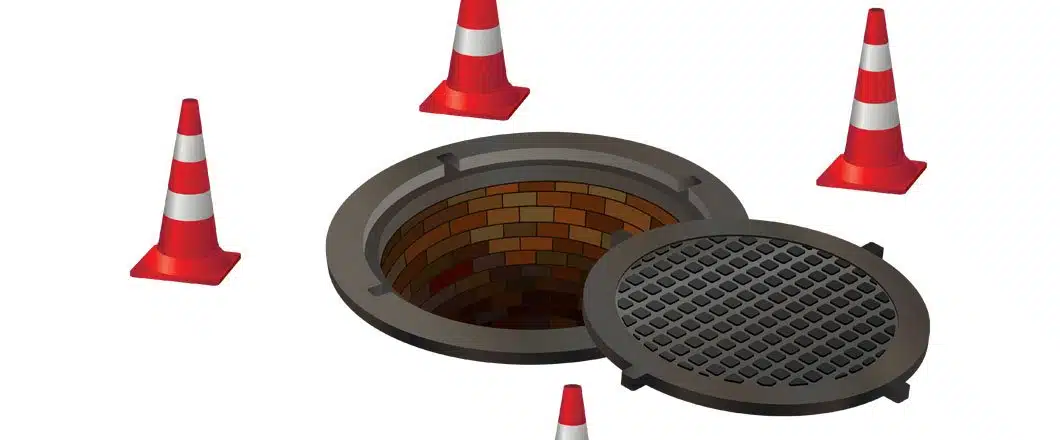
Surface Preparation — a Fundamental Necessity for Manhole Rehabilitation
In the trenchless technology industry, we are both blessed and cursed with multiple technology options to solve essential problems. For manhole rehabilitation, there are five basic technology options:
- Cement Spincast
- Polyurethane Spray
- Epoxy Spray
- Formed-in-Place Cement
- Mechanical Seal
Get clarity on your objectives: mitigating infiltration and inflow (I/I), optimizing bench flow, restoring structural integrity, protecting against corrosion, or all the above. Choose wisely. Understand the process, validate service life expectancy and know who is performing the work because Execution is Everything.
No matter what technology or service provider you choose, nothing is more important than surface preparation to ensure longevity and prevent failures of a manhole restoration project. Nothing.
In preparing this article, investigations were made within NASSCO, SSPC, NACE, and ASTM organizations for the most current wisdom on surface preparation and learned an estimated 85 percent of coating failures are directly attributed to incorrect or inadequate surface preparation. This is one of the drivers behind the steady increase in the requirement for onsite inspection. Thorough surface preparation makes common sense, but not always common practice.
RELATED: Four Steps to Streamlined Manhole Rehabilitations
Without getting too deep into the five technology options and vendor attributes (bonded vs. unbonded, structural vs. non-structural, corrosion barrier or non-protected) it is highly recommended to follow vendor specific guidelines for surface preparation. The following five steps are fundamental for any manhole rehabilitation project, any technology, any technique:
Step 1 — Visual inspection of the substrate
In most cases, brick and mortar or precast concrete will be the surfaces that need prepared. A top-down view will reveal this, but to truly study the surface, there is no substitute to entering the structure for bottom-up investigation. Using a forensic approach, look for evidence of water stains, defects, physical damage, corrosion or chemical damage, contamination and excess moisture from the bench to the chimney.
Step 2 — Pressure washing
Pressure washing will reveal greater insight into the existing condition of the substrate. Low pressure water-blasting (4,000 to 5,000 PSI) is most common, but high-pressure (5,000 to 10,000 PSI) and high-pressure water jetting (up to 30,000 PSI) may be required. To remove previous failed material applied to the native substrate, more extreme measures include dry and wet abrasive blasting (reference SSPC-SP CAB 1-3)
RELATED: Manhole Rehabilitation Overview: Considering and Choosing Your Options
Step 3 — Validate Substrate (brick or concrete)
An acceptable prepared surface should be free of contaminants, laitance, loosely adhering mortar, brick, or concrete, dust, and should provide a sound, uniform substrate suitable for the application of protective coating or lining system. (reference ASTM D4258)
RELATED: Rain Drain Restoration Tackles Manhole Rehab Along Airport Road
Step 4 — Active Leak Correction (brick or concrete)
There are advantages and disadvantages for each of the following techniques with respect to sealing active leaks, but all rehab technologies make this a fundamental requirement.
- Injection Grouting: A hole is drilled into or near the leak site and urethane grout is injected to stop leak (older brick structures may require a more comprehensive curtain grouting technique)
- Hydraulic Cement: fast-setting mortar used to stop individual leaks (not recommended for brick structures)
Step 5 – pH Testing
pH Testing may not be required by all rehab technologies, but if so, there are three standard types of testing methods and one little known secret that is easy and inexpensive to administer:
- pH test paper
- Insta-check pH pencil
- pH meter
- Phenolphthalein—a weak, colorless acid sprayed onto a wet concrete surface. If no color is observed, the concrete surface is still acidic and additional surface preparation is necessary. If the solution turns pink in color, the pH value has reached approximately 8. At a pH of approximately 10 the solution turns a bright magenta.
No matter what technology or service provider you choose, nothing is more important than surface preparation to ensure longevity and prevent failures of a manhole restoration project. Nothing.
If you are truly interested in your manhole restoration project passing with flying colors, you’ll make certain that surface preparation is your number one priority, but only after choosing the technology, methodology, and service provider that best meets your rehab objectives. Thorough surface preparation is a fundamental necessity to the extended service life you expect of your manhole, maintenance hole, window to the collection system.
Don Rigby handles education and engagement at Madewell Products Corp.