Inadvertent Returns
Primary Causes and Preventative Measures
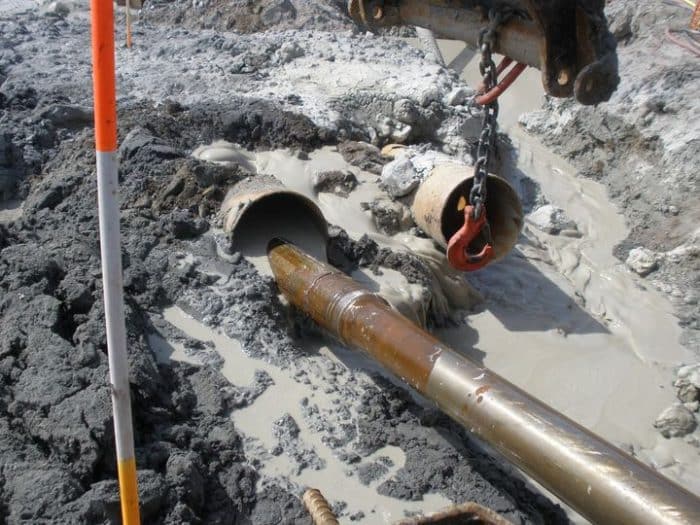
In one way or another, if you’ve worked in or around the HDD industry you’ve likely dealt with Inadvertent Returns (formerly known as Frac-Outs). I feel the proper definition of an Inadvertent Return (IR) is when the total volume of drilling fluid pumped downhole no longer follows the intended path, which is typically the bore path to the entry and/or exit pits. Others say an IR is an unintended discharge of drilling fluid to the surface, however, this is the final phase of an Inadvertent Return. An IR begins when the formation starts taking on drilling fluid, long before we see mud on the surface and/or completely lose flow. Sometimes an inadvertent return can “heal itself” by filling the void with fluid or drilled solids but when it doesn’t, mud on the surface or in a body of water is the result.
Causes
Basically, there is only one cause of an IR – EXCESSIVE DOWNHOLE PRESSURE – and drilling fluid will always follow the path of least resistance. Simple, right?!?! Control the downhole pressures and prevent IRs. But, as we all know and usually learned the hard way, nothing is simple in our industry. While we can easily control our pump pressures, trying to determine excessive downhole pressure can be difficult because of all the variables. Here’s a short list of common causes that can affect downhole pressure:
- Ground Formation – When comparing the several types of formations, solid rock and most clay formations can handle higher downhole pressures than unconsolidated formations like beach sand, some cobble or backfill. How many times have you encountered several different formations on a single bore, a clay formation with sand stringers, passing through different formations when trying to reach desired depth, etc?
- Depth – Typically, it takes more pressure to push fluid through 10 feet of cover material than it takes to push through 1 foot of cover material. The key word here is “typically”.
- Man-Made or Natural Obstructions – This would include previously installed pipelines, telephone poles, tree roots, water saturated ground or any type of structure and/or action that has disturbed the soil creates paths for the fluid to flow through, or around, with little resistance.
- Poor Drilling Fluid – A drilling fluid with high progressive gel strengths, loaded up or heavy with drilled solids can create excessive downhole pressures when trying to keep the fluid flowing. On the flip side – a drilling fluid without enough carrying capacity or gel strengths leads us to another issue…a dirty bore. Also, when drilling a clay formation without using enough clay inhibitor can cause the cuttings to stick together. When drill cuttings aren’t removed, they begin to build up or create a plug. Trying to push a large amount of fluid through a small space will increase downhole pressures, resulting in Inadvertent Returns.
- Fractured or cavernous ground – It takes very little pressure for fluid to flow into a fracture or cavern.
Preventative Measures
Here are some basic steps to help prevent IRs:
- Identify the ground conditions with geotechnical reports, well logs, etc. Ground formations play a large role in the bore design process as well as dictating what type of downhole tooling should be used, the drilling fluid mix design, the proper amount of drilling fluid to pump and the amount of pressure a formation can handle.
- Designing a drilling fluid based on the formation being drilled not only helps prevent IR’s but can also save time and money. Contact drilling fluid manufacturers for mud training, mix designs, and to questions about drilling fluid additives uses and addition rates.
- A common phrase heard throughout the industry but often misunderstood is – “Don’t out drill your mud”. A rule of thumb is to pump 1-5 times the hole volume (1X in a rock/cobble formation – 5X in a reactive clay formation). Out drilling the mud, or not pumping enough causes the fluid to become heavy which increases downhole pressure and increases the chance of an IR. Pumping too much fluid in a sandy or cobble formation “blows out” the formation, loads up the drilling fluid with solids, also increases the chances of an IR.
There are going to be situations where an IR is unavoidable but that doesn’t mean all is lost. I was on a project drilling through a fractured rock formation. During the planning process, losing flow was anticipated so we chose to use NSF approved drilling fluid additives. As expected, we had an IR and to make matters worse, the IR was flowing into a creek that was nearly impossible to access for containment. Using the proper additives and proving the drilling fluid did not create a toxic threat which allowed us to continue drilling successfully and complete the bore. Having a good containment plan prior to starting the bore can save hours, even days, of lost time.
Proper planning and preparation is essential for completing a successful bore, preventing IRs and earning a profit.