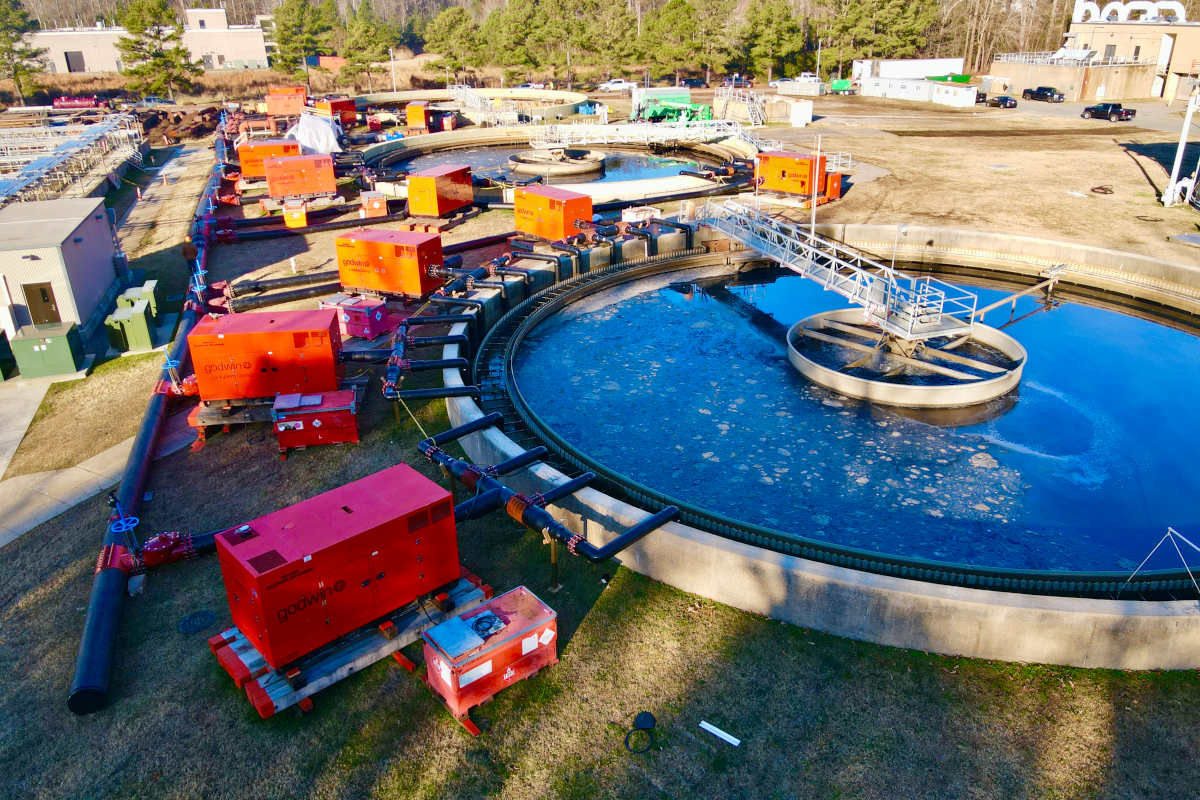
HRSD Assesses, Rehabs Pipes at the York River Treatment Plant
Prompted by a failure in 2020, the Hampton Roads Sanitation District commissioned a project to assess and rehabilitate critical piping at its York River Treatment Plant.
The Hampton Roads Sanitation District (HRSD) owns and operates 14 wastewater treatment plants in southeastern Virginia. The plants have a combined treatment capacity of 225 MGD, including the 24 MGD York River Treatment Plant in Yorktown, Virginia.
The plant was constructed in 1980 and suffered a crown corrosion failure of the 60-in. diameter headworks effluent pipe on Sept. 17, 2020, as Hurricane Sally dumped 6 in. of rain regionally. HRSD worked through the night and successfully contained the flow within 19 hours (Figure 1).
In the days that followed, a temporary flow diversion was assembled, isolating the 200 lf of prestressed concrete cylinder pipe (PCCP) piping for investigation and repair. CCTV investigation identified significant crown corrosion along the entire pipeline, with substantial lengths of exposed and compromised cylinder and reinforcing wire.
Six-months into the COVID-19 pandemic and facing material supply shortages, Rummel, Klepper & Kahl LLP (RK&K) coordinated with multiple pipe vendors to assess replacement material alternatives.
A combination of replacement and sliplining with 48-in. HDPE was performed to remedy the aged pipeline. Upon completion of the repair, and while diversion pumping equipment and material was available on-site, HRSD intermittently isolated and inspected 900 ft of downstream primary clarifier (PC) influent and effluent PCCP.
The condition assessment revealed significant to moderate crown corrosion, justifying a prioritized capital improvement project.
The condition of the three primary clarifier influent pipes was most concerning, with chunks of spalled inner concrete liner obstructing the CCTV camera from fully traversing the invert of each pipe section. The deterioration severity was consistent with changes in pipe geometry and the wastewater treatment processes.
Evaluating Repair Alternatives
RK&K evaluated the technical and economic feasibility of rehabilitation and replacement alternatives. It determined rehabilitation with carbon fiber reinforced polymer (CFRP) as advantageous and preferred over cured-in-place pipe lining and replacement. This was based on repair certainty, risk reduction, impacts on plant operations and/or favorable construction costs.
Key parameters considered in evaluating the alternatives included:
- Uncertain pipe geometries and challenging locations including tight bends, obscure terminations, and substantial primary clarifier influent pipe lengths located beneath the clarifiers
- Access restrictions including tight flow distribution structures and limitations in the center feed clarifiers, requiring access through center column modifications
- Active flow conditions and related worker protections from weir gate leaking and potential overtopping during extreme peak flows
- Treatment plant operational requirements restricting PC and aeration tank (AT) removal from service to one at a time and seasonal limitations requiring all aeration basins during winter months.
To attract a variety of bidders, replacement of the 231 lf of interconnected PC effluent pipe was allowed as an alternate bid item.
Rehabilitation or replacement of this combined piping required full bypass of the PC effluent flows from the center feed clarifiers to the aeration tank influent distribution chamber (DC2).
The rehabilitation project scope (Figure 2) included:
- Section 1: Rehabilitation of 455 lf of PC influent pipe in three sections
- Section 2: Rehabilitation or replacement of 231 lf of interconnected 36- to 72-in. diameter PC effluent pipe; rehabilitation of three PC effluent chambers; and abandonment of 246 lf of future expansion enabling piping
- Section 3: Rehabilitation of 271 lf of 42-in. diameter AT influent pipe in three sections
York River Project Requirements
Preparation of contract documents for traditional design-bid-build procurement featuring vendor-driven rehabilitation system design required establishment of design criteria and construction requirements including:
- Rehabilitation design for fully deteriorated host pipe
- Construction phasing plan prioritizing the PC influent pipe
- Treatment plant operation, coordination, and related change logistics
- Bypass pumping from each PC to DC 2 to isolate the PC effluent piping.
The trenchless pipeline rehabilitation technology used for this project was V-Wrap CFRP, supplied by Structural Technologies.
V-Wrap CFRP is a structural strengthening system for the restoration of damaged/weakened pressure pipe. V-Wrap utilizes layers of specially designed CFRP composite applied both longitudinally and circumferentially in the deteriorated pipe to resist all loads acting on the pipeline system.
The existing piping serves as a form for the CFRP system which becomes the new pipe once the system is installed. The CFRP design follows the approach of AWWA C305 standard for a standalone liner system (AWWA Class IV).
The CFRP installation steps include dewatering, cleaning and surface preparation, adhesion testing, fabric saturation, weight ratio testing, fabric installation, testing for voids, compression ring end-seal installation, topcoat application, and final CCTV and walk through inspections. The CFRP system provides a 50-year life extension to the pipelines.
Post cleaning visual inspections revealed structurally critical deterioration at similar locations in each of the three PC influent pipes. Given the significant deterioration and loss of wall integrity, the contractor (Structural Technologies) consulted with their liner designer (Simpson Gumpertz & Heger) for design of temporary shoring to allow for safe personnel entry.
Once temporary shoring was in place, implementation of locally applied CFRP between the temporary shoring posts was used to mitigate the risk of potential collapse.
Section 2 Bypass Design
Rehabilitation of the Section 2 PC effluent pipeline connecting the clarifiers to DC 2 required full bypass of PC effluent flows. These pipes are all connected without means for isolation, which differed from the Section 1 and 3 piping which were isolatable by removing clarifier basins from service and diverting flows to the other pipelines.
The bypass system featured 12 pumps controlled via a programmable logic controller (PLC) to maintain the water level in each clarifier within a window of 12 in. The PLC provided 24/7 remote monitoring of 21 different alarm conditions as well as real time reporting of level in each clarifier, pump run status and speed.
The bypass system (Figure 3 – featured image at top) for each clarifier consisted of four pumps with 10-in. intake suction piping positioned between the clarifier walls and launderer which allowed only 13 in. of clearance for suction piping.
In such a tight area, spacing of the pumps was key and each pump had to be laid out individually prior to setting the next pump. Each pump discharged to a temporary HDPE trunk line consisting of 24- to 36-in. piping. The trunk discharged into DC2 via three 24-in. HDPE discharge pipes, each equipped with knife valves for isolation and flow tuning.
With the PC effluent piping isolated, the effluent chambers were rehabilitated simultaneously with the pipeline. Based on as-found conditions, chamber rehabilitation included demolition, repair of patch areas, removal of microfractures, confirmation of concrete surface profile, preparation of existing reinforcement, and placement of repair materials.
Lastly, the plant was originally designed to accommodate future hydraulic expansion which was no longer envisioned. While rehabilitating the PC effluent pipes, 246 lf of expansion piping was bulk-headed and abandoned with cellular concrete.
Successful Outcome for HRSD
The construction contract allowed 12 months to complete the work. Through optimization of the schedule and resource loading using the daily work windows, Structural Technologies completed the project in only six months.
A collaborative mind-set from inception through completion was a major benefit to the project. Successful outcomes were the common goal of engineering, plant, and contractor personnel.
The contractor mobilized promptly, staffed the project appropriately, and prepared and executed an expedited project phasing plan reducing construction activity by six months, including work completion in advance of the seasonal operational restriction.
The contractor reported progress through shift activity reports including two-week look-ahead schedules so HRSD’s project manager, plant personnel, and the engineering and inspection team readily knew the work status and what to expect in coming days and weeks. This communication was welcomed with enthusiastic support of plant personnel who facilitated process change requests for upcoming phases of the work.
Project successes included pipe rehabilitation without impacting treatment quality or regulatory compliance, timely project completion, and a single cost-only change order limited to unforeseen conditions. Plant reliability was improved, and the project team hopes to collaborate on future projects.
Ann Copeland, P.E., PMP, ENV SP, is senior project manager at The Hampton Roads Sanitation District. Brad Alger is technical manager with Rummel, Klepper & Kahl LLP (#20 in our Top 50 Trenchless Engineering Survey). Atilana Bolton, P.E., Assoc. DBIA, is technical project manager with Structural Technologies.