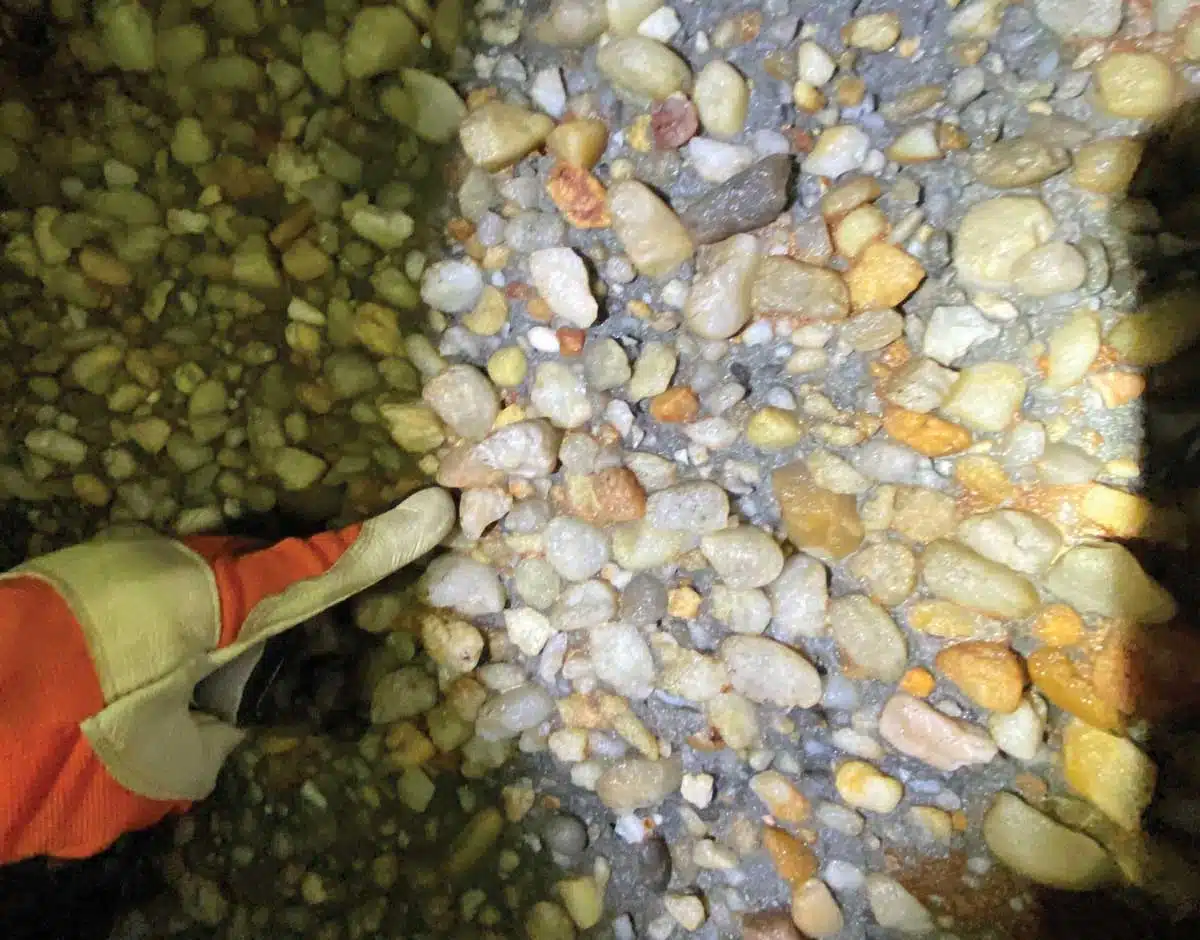
How to Properly Rehab a Manhole
Wastewater collections systems are comprised of gravity pipes, manholes, lift stations and force mains that gather used water from residential and nonresidential customers and convey the flow to the wastewater treatment plant.
Manholes serve an important role within collections systems. These vertical underground confined spaces are used by utility personnel and maintenance contractors as a point of access to the sewer system.
Specifically, some of the main purposes of a manhole are to:
- Join sewer lines or change direction or alignment of sewer pipes
- Allow access for CCTV inspection to be performed to identify joint misalignment, broken piping, substrate corrosion, or ground water infiltration
- Allow access to clean and remove obstructions present using high-velocity jet (hydrocleaning) equipment
- Allow access to apply trenchless maintenance technologies to sewer pipes, such as cured-in-place pipe (CIPP) lining or spray-in-place pipe (SIPP) lining
The Problem
Manhole structures are predominately constructed of Portland-cement precast concrete. These manholes are susceptible to acid attack from biogenic sulfide corrosion — a bacterially mediated attack mechanism common to wastewater collections environments — that rapidly degrades the cement paste of concrete, ultimately causing substrate loss and structural deterioration of the manhole1 (Figure 1).
Likewise, masonry manholes constructed with clay or shale bricks and laid with portland-cement mortar are also susceptible to biogenic sulfide attack of the mortar joints. This can result in similar structural deterioration of the manhole, oftentimes quite extensive, especially when the mortar joints are completely corroded leaving the bricks unsecured (Figure 2).
Biogenic sulfide corrosion of Portland-cement concrete and brick masonry manholes results in a reduced service life of these assets and allows for the infiltration and inflow (I&I) of surface and ground water into the sewer network. This destructive combination creates an enormous financial burden on the utility of the collections system.
Manhole Rehabilitation Solutions
There are a myriad of manhole rehabilitation technologies aimed at stopping biogenic sulfide corrosion of Portland-cement concrete and brick masonry manholes. Many of these corrosion protection technologies also promote the elimination of I&I from entering manholes — an emerging feature that is perhaps equally as important as corrosion protection.
Unfortunately, the rehabilitation of manholes can be complicated, and the selection of the correct product or technology can, at times, be confusing.
The NASSCO Manhole Rehabilitation Performance Specification Guideline discusses many of the common rehabilitation technologies for manholes2. These product technologies vary in material composition, installation requirements and cost, and functionality.
A general list of some of the common rehabilitation technologies include:
- Cementitious liners (geopolymer, epoxy-modified, calcium aluminate, microsilica-based)
- Polymer liners (structural epoxies or structural polyurethanes)
- Composite liners (fiberglass or carbon fiber-reinforced epoxy)
- Cast-in-place concrete (portland-based or polymer-based)
- Cured-in-place liners (CIPM)
- Concrete protective liners (HDPE or PVC sheet liners)
- Fiber-reinforced plastic (FRP) liners
Most of these rehabilitation technologies rely on adhesion (aka, bonding) to the manhole substrate to provide corrosion protection. Likewise, adhesion to the host substrate is paramount for rehabilitation technologies that can eliminate I&I from entering the manhole. For these systems, preventing I&I is achieved when the adhesion of the rehabilitation technology is greater than the tensile strength of the manhole substrate. In other words, the bond strength of the rehabilitation system exceeds the tensile properties of the manhole substrate and I&I is held back by the rehabilitation system from entering the manhole. This level of bonding is important to prevent an annulus occurring between the liner and the substrate which in turn staves off water migration. Surface preparation plays a critical role in achieving maximum adhesion to the substrate.
Surface Preparation
What is surface preparation and why does it need to be performed on manholes? Manhole environments become contaminated over time. For example, hydrogen sulfide (H2S) gas fills the headspace and can deposit sulfur contaminants onto surfaces (Figure 3). Biogenic sulfide corrosion generates dilute sulfuric acid and attacks the substrate, weakening or completely removing the portland-cement paste and exposing poorly secured aggregate and surface contamination from dirt deposits carried by I&I. Surcharge conditions expose manhole surfaces to wastewater containing fats, oils, and grease (FOG) and other debris. These, and many other types of contaminants interfere with optimum adhesion and I&I abatement capability of bonded rehabilitation technologies.
Optimum adhesion for bonded rehabilitation technologies is accomplished during the initial stage of the installation process, called surface preparation. Surface preparation is the process by which a clean, sound, and suitably roughened surface is produced on a concrete or brick masonry substrate using various preparation methods such as detergent washing, high-pressure water cleaning (5,000 psi or greater), abrasive blasting, grinding, impact tools, or a combination thereof. Surface preparation removes contaminants and produces a sound manhole surface, including a roughness profile and porosity, that will be a basis for providing a strong mechanical bond between the substrate and the installed rehabilitation material.
To what extent is surface preparation performed in manhole rehabilitation? Unfortunately, a manhole-specific industry consensus standard for surface preparation does not exist. The NASSCO Manhole Rehabilitation Performance Specification Guideline provides general installation requirements and testing acceptance, and the NASSCO Inspector Training Certification Program for the Inspection of Manhole Rehabilitation3 offers a more in-depth discussion on surface preparation requirements and testing. However, both defer to the rehabilitation material manufacturer’s recommendations for acceptance and testing criteria. This can lead to irregularity between acceptance requirements within equivalent rehabilitation materials, which in turn, may not achieve optimum surface preparation goals and can create potential conflicts with project contracts/specifications.
Improving Manhole Prep Standards
Other industry sectors, such as wastewater treatment plant rehabilitation — exposed to similar conditions and concrete corrosion — use many of the same rehabilitation materials that are used for manholes. For example, structural epoxy polymer liners and epoxy-modified cementitious liners are commonly used as corrosion protection technologies for new and rehabilitation wastewater treatment projects.
For wastewater treatment plant projects, it is common to reference industry standards, such as SSPC-SP13/NACE No. 6 Surface Preparation of Concrete4 and ICRI 310.2R Selecting and Specifying Concrete Surface Preparation for Sealers, Coatings, Polymer Overlays, and Concrete Repair5 to better define the surface preparation of concrete, including how it is performed, the level of substrate cleanliness and anchor profile, and testing and acceptance criteria of this operation. Referencing these standards establishes clear and consistent surface preparation requirements and acceptance criteria for the project.
Referencing the SSPC-SP13/NACE No. 6 or ICRI 310.2R could improve the consistency of surface preparation for manhole rehabilitation projects. However, the argument against referencing these standards is that they originate from other industry and may not be applicable or necessarily familiar to the contractors who perform work in the manhole marketplace. This is a valid argument.
A better solution is for industry to create a manhole-specific surface preparation standard created to address the key elements of properly preparing a manhole to receive rehabilitation technologies. This would ensure consistent preparation of manholes and allow rehabilitation technologies to achieve optimum service protection.
When specifying, it is critical to define the result of the preparation over the method. For example, if specifying hydroblasting methods, avoid specifying minimum water pressure required without also the resulting effect that will be measured. It’s the result that will dictate whether the pressure was enough so to meet the defined resulting standard. Defining the result is paramount to eliminating ambiguity. The aforementioned references can assist a specifier with these defined measurements (results) for passing.
Conclusion
Surface preparation is a key element in determining the success of a manhole restoration project. Improper or inadequate surface preparation may allow I&I into the manhole structure or lead to the failure of a manhole rehabilitation technology. The manhole industry generally relies upon manufacturer’s recommendations as the basis of surface preparation. This leads to potential disparity of surface preparation techniques and standards between rehabilitation technologies, even within identical technology types. An industry-specific manhole surface preparation standard would offer a solution to the industry to ensure consistent, optimum surface preparation is achieved.
References
- O’Dea, Vaughn, “Understanding Biogenic Sulfide Corrosion”, Materials Performance (November 2007), pp. 36-39.
- NASSCO Manhole Rehabilitation Performance Specification Guideline, NASSCO, Inc. Frederick, MD. 2013.
- NASSCO Inspector Training Certification Program for the Inspection of Manhole Rehabilitation, NASSCO, Inc. Frederick, MD. 2012.
- SSPC-SP13/NACE No. 6 Surface Preparation of Concrete, AMPP, Houston, TX, 2018.
- ICRI 310.2R Selecting and Specifying Concrete Surface Preparation for Sealers, Coatings, Polymer Overlays, and Concrete Repair, International Concrete Repair Institute, Inc., St. Paul, MN. 2013.