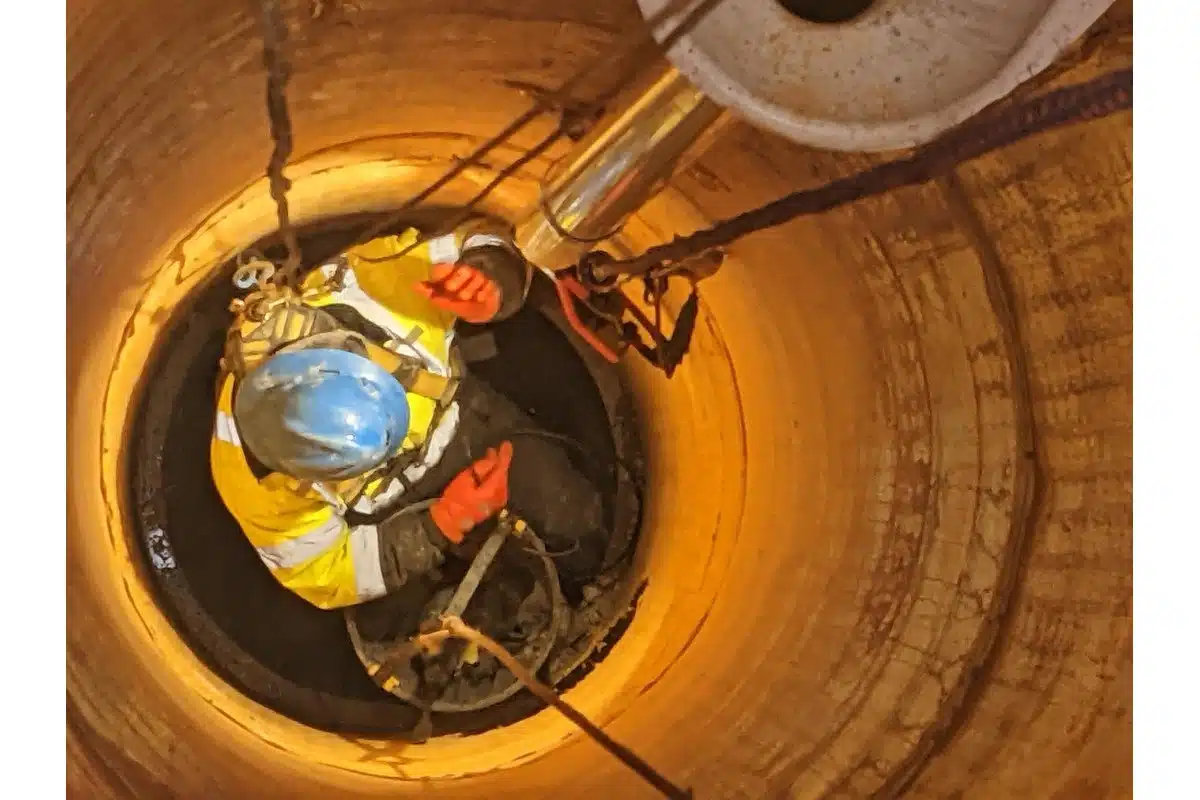
Transforming Manhole Rehabilitation
A Case Study on Advanced Solutions for Corrosion Resistance
Aging infrastructure poses significant challenges for municipalities across the United States, particularly in urban areas where sewer systems have been in place for decades. Many of these systems were constructed using materials that are susceptible to corrosion and degradation over time.
Manholes, which are critical components of sewer systems, often suffer from corrosion and structural degradation due to harsh environmental conditions, especially where hydrogen sulfide (H2S) is prevalent. The presence of H2S exacerbates these issues. H2S, a byproduct of anaerobic bacterial activity, is highly corrosive and can significantly accelerate the deterioration of concrete and metal structures within manholes.
Corrosion in manholes is not just a structural concern; it also poses environmental and public health risks. When manholes deteriorate, they can allow infiltration and inflow (I&I), leading to excess water entering the sewer system. This not only increases the treatment burden on wastewater facilities but also raises the risk of untreated sewage overflows, which can contaminate local water bodies and pose serious health hazards.
Traditional rehabilitation methods, such as spray-on epoxy and cementitious liners, frequently fail under these conditions, leading to further deterioration and the potential for catastrophic structural collapse. Additionally, traditional dig-and-replace methods are often not feasible due to their high cost, extensive disruption, and the risk they pose to surrounding structures. However, an innovative method exists that avoids excavation, results in a brand-new manhole within the existing structure, and offers 100 percent structural integrity and corrosion resistance, setting a new standard in manhole rehabilitation.
Manhole Problem Identification
In a recent project in a small municipality in South Dakota, the challenges of aging infrastructure were vividly illustrated. The municipality was grappling with a deteriorating manhole more than 40 ft deep that had been previously rehabilitated using spray-on epoxy coatings.
Unfortunately, due to the improper application that caused pinhole leaks, these epoxy coatings were unable to provide adequate protection against corrosive elements. The coating, because it was improperly applied, began to peel off of the manhole walls allowing gases, particularly H2S, to penetrate behind and seep between the liner and the manhole walls.
Over time, this seepage led to a gradual degradation of the manhole’s structural integrity — exacerbating the corrosion of the underlying concrete and exposing the wire mesh within the structure. The threat of structural failure and collapse was imminent, emphasizing the limitations of traditional rehabilitation methods in environments with high levels of H2S.
Project Challenges
The rehabilitation of this manhole, exceeding 40 ft in depth, posed unique challenges that rendered traditional methods impractical. Located immediately adjacent to a large car dealership building and its parking lot, excavation would have necessitated digging up the entire corner of the building.
This presented a significant risk of structural damage or collapse to the dealership itself and nearby buildings. The potential for a sinkhole was also a concern due to groundwater seepage bringing soil into the manhole over time.
The financial implications were substantial, with estimates running into multiple hundreds of thousands of dollars, solely for excavation and associated repairs. Given these risks and costs, traditional dig-and-replace methods were not feasible, highlighting the necessity for trenchless rehabilitation methods as the only viable solution.
Another challenge was stabilizing the air quality before beginning the rehabilitation work. This involved deploying an air-moving fan positioned upstream of the work area to mitigate high concentrations of H2S. Powered by a large air compressor, the fan effectively reduced H2S levels to safe limits, ensuring a secure working environment. Maintaining continuous operation of the fan was critical to sustaining safe conditions, as any interruption could quickly reintroduce hazardous gases.
To manage the high flow rates from the large interceptor line, an internal bypass was employed using a pneumatic plug with a flow-through pipe. This approach allowed the redirection of flow away from the work area, enabling safe working conditions without direct exposure to the flow.
This method was essential for repairing the bench and invert as required before initiating the Monoform PLUS process on the manhole. Traditional bypass methods would have been excessively costly for the municipality, particularly given the interceptor line’s critical role in the town’s infrastructure. Potential shutdowns would have necessitated extensive bypassing efforts, risking environmental impact if flow redirection was mishandled.
The Solution: Innovative Manhole Rehabilitation
Addressing the challenges of deteriorating manholes requires a method that goes beyond traditional solutions. The approach employed here involves creating a fully structural, independent lining system. Custom ABS plastic forms establish an annular space within the existing structure, which is then filled with a high-strength concrete mixture reinforced with fiber mesh.
This system integrates a corrosion-resistant HDPE liner, offering robust protection against hydrogen sulfide. Once the concrete sets and the forms are removed, the resulting lining system stands alone, meeting rigorous load specifications and ensuring long-term durability.
This method streamlines surface preparation and performs well under various environmental conditions, significantly reducing project timelines and disruptions. For example, in a recent project near a commercial building, this approach was applied effectively without extensive excavation, thereby minimizing impact on the surrounding area.
A representative from the municipality noted, “The solution provided was efficient and high-quality, avoiding costly and disruptive excavation. The team’s work was impressive, meeting our needs and ensuring minimal impact on nearby infrastructure.”
Long-Term Impact & Conclusion
In addressing the challenges posed by deteriorating manhole infrastructure in a small municipality, traditional manhole rehab methods, such as spray-on coatings and dig-and-replace, proved impractical due to environmental risks, structural constraints, and escalating costs. These challenges were compounded by the high levels of corrosive hydrogen sulfide (H2S), which accelerated structural degradation and posed significant public health risks.
John Bluntach is structure rehabilitation business development director with HK Solutions Group.