Current and Emerging Water Main Relining Technologies
December 27, 2011
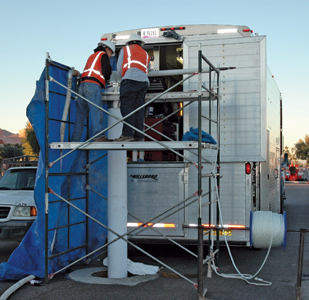
There is an increasing availability of water main relining technologies, which provide solutions that minimize replacement problems while providing potentially cost-effective alternatives to traditional open-cut replacement. This article summarizes a recent EPA report (Morrison et al., 2011) on a comprehensive review of existing and emerging renewal technologies for water distribution systems. Generally, renewal includes a broad spectrum of approaches, from repair to replacement and water main relining methods typically fall into the rehabilitation category, which are techniques that are often used to extend the operational life and restore much or all of the pipe’s hydraulic capacity, improve water quality, and/or restore structural functionality.
Rehabilitation approaches vary by pipe size: small mains (i.e., pipes less than 16 in.) are typically easier to replace, except in areas where access is difficult and typically less consequential when they fail; large mains (i.e., pipes 16 in. and larger) are typically more consequential when they break and require a more proactive condition assessment and renewal strategy.
Water main relining technologies are typically categorized into four classifications based on the AWWA M28 Manual (AWWA, 2001b). Liners that only act as corrosion barriers are considered non-structural Class I. Close-fit lining systems that span holes in the host pipe, but require support from the host pipe to prevent collapse are considered semi-structural Class II. Class III linings also span holes, but have sufficient thickness to resist bucking from external hydrostatic or vacuum loads. Fully structural Class IV linings act as a separate pipe and the existing pipe acts merely as a right of way for the installation. Water main relining technologies include spray-on lining, sliplining, cured-in-place pipe (CIPP), inserted hose lining and close-fit lining systems as described below.
Spray-On Lining
Epoxy lining involves cleaning the pipe to remove existing corrosion buildup and then spraying a thin, 1-mm epoxy coating on the inner pipe wall that cures in roughly 16 hours. Most lining machines are computer controlled with warning devices that sound if the minimum lining thickness is not being achieved. The specified conditions for using epoxies in water mains should be verified from the Nation Sanitation Foundation (NSF).
Polymeric lining materials have been used in the United Kingdom for several years and have started to see use in the United States. The linings are installed in a similar manner to the epoxy materials, but gain their physical properties within minutes of being applied. Around 6,000 miles of water mains have been lined with these materials, mostly in the United Kingdom and Canada.
Sliplining
Sliplining is a method of pipe rehabilitation in which a new pipe of smaller diameter is inserted directly into the host pipe by pulling or pushing. Segmental sliplining uses short pipe segments that are assembled at the entry point of the existing pipe. After installation, the annular space is grouted and the grouting pressure must not exceed the buckling resistance of the liner. Segmental sliplining pipes can be HDPE, PVC, centrifugally cast fiberglass reinforced polymer mortar, steel, glass-fiber reinforced plastic or ductile iron. Continuous sliplining uses continuous lengths of pipe or pipe that is assembled in the field prior to insertion. Continuous sliplining pipe can be HDPE, fusible PVC or welded steel.
Cured-In-Place Pipe (CIPP) Lining
CIPP lining begins with cleaning the pipe to restore the cross-section and plugging existing services to prevent resin migration. The pipe surface should be free from debris and water, particularly if the liner is required to bond to the wall. The installation can be an inversion or pull-in process and the resin impregnated tube is cured with either hot water or steam. Any cut ends or service connections must be pressure tight to prevent resin tracking and services may be reinstated by excavation or using a cutter.
Inserted Hose Lining
Inserted hose liners can be woven fabric and coated inside and out with PE or made entirely of PE. Prior to lining, the service connections are located and the pipe is cleaned. The liners are winched into place in factory folded shapes and reverted to round using air, steam, or water. Pressure testing occurs after the liner cools and then services are reinstated with excavation or using a robotic system.
Close-Fit Lining
Close-fit lining is a family of methods known by several names (e.g., fold and form, symmetrical reduction, reduced diameter pipe, etc.) in which a thermoplastic liner pipe is temporarily deformed in the field or at the factory to reduce its cross-section before its insertion into the host pipe. With the liner pipe in its deformed condition, it becomes a sliplining operation to install the new pipe since the reduced cross-section creates sufficient clearance for the installation. The deformed liner is subsequently restored to its original diameter usually with internal pressure forming a close-fit with the original pipe. Existing services are reinstated by direct excavation, robotic, or man entry methods.
Other Liners
Grout-in-place PE liners have closely spaced, hooked anchors on the outside of the liner that serve as spacers maintaining an annulus with the inner pipe surface. The annulus created is filled with a high-strength cementitious grout and then a rounding swab is passed through the pipe, applying air pressure, rounding the liner tube, and distributing the grout evenly against the interior surface of the host pipe.
Melt-in-place pipe was first trialed in the United Kingdom in 2008. The composite liner is made up of glass fiber reinforced polypropylene and a woven tube. Once in place, the liner is heated by an electrically powered heating pig that melts the thermoplastic, and a removable silicon inversion bag is used to pressurize the liner tightly against the host pipe. A summary of the water main relining technologies presented above is provided in Table 1.
John C. Matthews, Ph.D., is a research scientist at Battelle Memorial Institute, Baton Rouge, La. Ariamalar Selvakumar, Ph.D., P.E., is an environmental engineer at the U.S. Environmental Protection Agency National Risk Management Research Laboratory, Edison, N.J. Wendy Condit, P.E., is a senior research scientist at Battelle Memorial Institute, Columbus, Ohio.