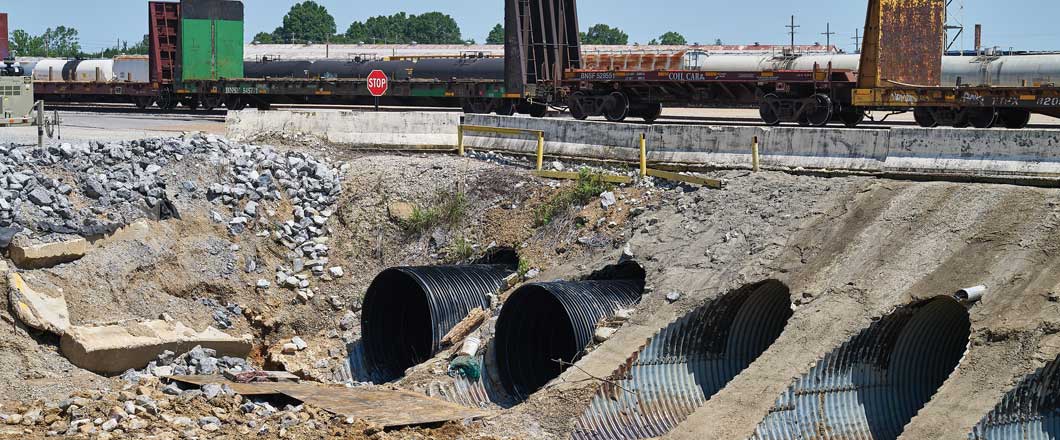
Culvert Rehabilitation at BNSF’s Memphis Rail Yard
Located in Tennessee, the BNSF Memphis Rail Yard is a bustle of activity. With more than 30 tracks, 25 of which are actively running, this is a critical yard that connects the East and the West Coast Class One railroads. There is constant activity. Scheduling is a critical aspect to the performance of the yard.
Located directly beneath this hub, are seven large culverts, each one 114-in. diameter and 1,436 lf. While these culverts have far exceeded their service life design, it had been determined that they were in need of replacement or repair. Most were experiencing some form of deflection and significant deterioration at the invert. Sink holes were starting to appear in between the tracks which created great concern for the railroad.
Given the prohibitive costs to replace these culverts, BNSF looked at repair options and determined that a reline solution would be most effective both structurally and cost-efficiently. A replacement would require a complete shutdown of the yard for an indeterminate period of time to allow for an open-cut and replacement of the existing culverts running directly beneath the central location of the yard.
RELATED: Emergency Culvert Reline and Repair in San Diego
It was critical this scenario be avoided as the cost deficits would be astronomical and the impact to the yard and freight transportation would be devastating. However, a solution that would provide a long-term structural repair and meet the hydraulic requirements was also critical.
Because of the age, deformed condition and close spacing of the host structures, experienced tunneling contractor LRL Construction Co. was selected to perform this reline job. They had experience working in confined spaces around the rail. Based on a detailed review of available options and long-term requirements of the project, a steel reinforced polyethylene solution was selected to reline five of the existing culverts.
Manufactured by Contech Engineered Solutions, DuroMaxx SRPE liners conform to the specifications in the AREMA Manual for Railway, Section 4.17, for design and load rating requirements. Due to the low Manning’s n, the DuroMaxx SRPE reline solution also provided an increased hydraulic flow capacity allowing for a slightly smaller diameter of 96-in. to be sliplined into the 1,436-lf space of each host pipe for a total of 7,200 lf, nearly a mile and a half of pipe end to end.
Because of the critical nature of this project to BNSF and the installation methods required to make it a success, it was determined that weekly calls be set up to track manufacturing, delivery and installation. This high level of communication also included pre-construction meetings with the contractor and the railroad. There could be no impact to the train schedule, and safety was extremely important.
The host pipes originally installed in the early 1960s had experienced heavy bed loads and high velocities over the span of their service lives. In a few barrels, the host pipe was starting to roll up on itself in some areas due to loss of backfill between the culverts. There was concern of void spaces between and over the culverts as well as the host pipes continuing to move over time from the massive loads over the top of these structures.
The culverts needed to be accurately measured to ensure that the 96-in. steel reinforced polyethylene reline pipe would fit. This needed to be done fairly quickly before further storm events and the train loading compounded this situation. Concern had to be taken to ensure that the liners were installed correctly even as parts of the host had to be removed.
RELATED: Contech Engineered Solutions Offers More Than Trenchless Pipe Products
The liner pipe was shipped directly to the site in 41- and 45-ft sections from the manufacturing facility located in Montgomery, Alabama. Grout ports and skid tubes were attached to each section of pipe. The skid tubes would aid in installation to avoid surface abrasion or damage during installation. There were four yard drain tie ins that also had to be reconnected on the site. The contractor was able to use top-hat risers specifically made to meet site conditions and install them once the main barrel was relined.
The contractor devised an ingenious method whereby they were able to push each length of pipe through the inlet end. Many days the contractor was able to get more than 10 pieces (more than 450 ft of pipe) in a single day while installing internal bands on each section, as well.
Randy Zeiger, P.E., senior operations manager at LRL Construction Co., commented, “The pipes installed much quicker than we originally thought. We had anticipated installing up to four pipes a day but were able to average about 10 pipes instead. The installation went very smoothly.”
As each section was completed, a multi-stage grouting process was performed to set the pipe liner into the host pipe. A cellular grout was used to backfill the void space between the liner pipe and the host. During one weekend between sliding the DuroMaxx into the host pipe and grouting it into place, there was a significant rain event dropping approximately eight inches of rain over a weekend. The experienced reline contractor was able to avert disaster with some additional suggestions made by Contech.
RELATED: Small Diameter Tunneling Machine Digs Emergency Utility Line
The rehabilitation of these three culverts running under the rail yard was completed with no interruption to the ongoing rail services of the Memphis yard. The remainder of the project will be finished after the rainy season in 2020.
Three of the seven culvert pipes were eventually fully grouted for a completely structural solution that allowed for an extended service life with a possibility of 100-years or more. The rehabilitation of these three culverts running under the rail yard was completed with no interruption to the ongoing rail services of the Memphis yard.
The remainder of the project will be finished after the rainy season in 2020. The success of this project led to two other relines with BNSF.
Don Herbert is the account manager and director for Rail Markets at Contech Engineered Solutions.