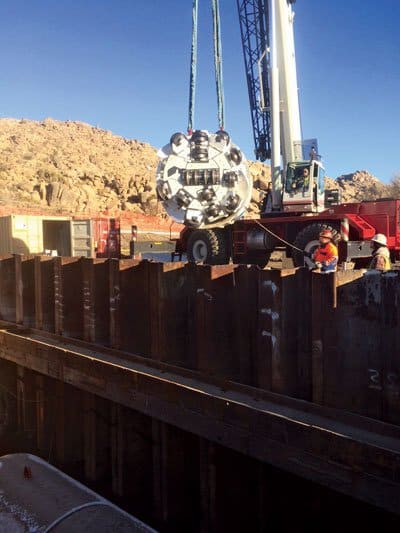
Small Diameter Tunneling Machine Digs Emergency Utility Line
May 15, 2015
Among the destruction was a sewer pipeline running below the Mojave River that conveyed 14 million gals per day (gpd). The damaged sewer line was replaced in just eight days following the flooding, with 5,000 ft of temporary sewage conveyance facilities to service surrounding areas. The work required a pipe bridge and transferred the wastewater to a section of undamaged pipe. However, the setup was deemed inadequate for long-term use and the Federal Emergency Management Agency (FEMA) and California Office of Emergency Services (Cal OES) set up funding for a permanent solution.
The Upper Narrows Pipeline Replacement Project, proposed by owner Victory Valley Wastewater Reclamation Authority, is just such a plan. The new pipeline measures 6,430 ft in length and is being placed deep below the riverbed. A portion of the pipeline is also being relocated out of the riverbed and constructed along streets adjacent to Victorville. The existing sewer pipe will be left in place and become fish habitat.
Trenchless Variety
As it winds below and alongside the Mojave River, the new section requires multiple different trenchless technology methods, from horizontal directional drilling (HDD) to rock tunneling, microtunneling and pipe ramming. HDPE pipe will serve as an upgrade to the section of pipeline, replacing the previously used vitrified clay carrier pipe. In 2014, contractor J.W. Fowler was awarded the complete contract for pipeline construction, including all of the various pre-specified trenchless methods.
J.W. Fowler, a family-run business since 1972, was well-versed in the various methods and felt confident it could overcome project challenges. “This project has all the different facets of trenchless technology. You usually don’t see that in a project of this size,” said J.W. Fowler project manager Jeff Anderson.
The pipeline travels through a variety of geologies, from clay to granite. The contractor first tackled twin HDD drives, measuring 1,740 ft each. It then followed up with 60-in. microtunneled drives with steel casing, measuring 865 ft and 1,850 ft in length. J.W. Fowler is now on its third project, a 1,250-ft rock tunnel, before completing the work with a final 140-ft section of pipe ramming.
Rare Requirements
The project was initially designed envisioning a pipe jack through the rock tunnel section to meet the microtunneled section. The unexpected discovery of varying lenses of hard rock and soil throughout the rock tunnel section, however, caused the project team to rethink the plan. Eventually, it was decided that a rock machine with the capability to install either liner plate or rib and board liner would be best. The machine could be equipped with the ability to propel itself either by thrust from the erected liner system or through the grippers.
“The rock machine coming from the other side will meet with the Microtunneling Machine (MTBM), and then we will extract the MTBM through the rock tunnel. We decided that due to the length of the tunnel, this would be the best option,” said Anderson.
Because of those requirements, J.W. Fowler was looking for a machine to bore a long section of tunnel in rock of varying strengths, at a depth of 100 to 150 ft, and one that could do so with pinpoint accuracy. The contractor would need to be within inches of line and grade in order to meet up with the abandoned microtunneling machine.
Rockhead Rolls In
J.W. Fowler turned to The Robbins Co. for supply of its largest Rockhead to date — a 78-in. diameter, heavy duty tunneling machine with 14-in. diameter disc cutters that was capable of excavating very hard rock conditions. The rugged machine functions much like a hard rock, shielded TBM. Grippers push against the tunnel walls, propelling the machine forward so that it does not require launch with an ABM or pipe jacking unit. A variety of types of tunnel lining can be installed in the tail shield, from ring beam and board to four-flange liner plate. The self-propelled machine is capable of excavating distances of 2,000 ft or more, depending on the conditions.
The machine was engineered and assembled in Robbins’ Solon, Ohio, facility by a small but specialized crew and shipped to the jobsite in early 2015.
Ready for Launch
The Robbins Rockhead launched on Jan. 16, 2015, from a pit measuring 60 ft long by 16 ft wide and 14 ft deep. A crew of eight to nine members have since been running the machine 24 hours per day, six days per week. The seventh day is used for maintenance.
Ground conditions have been softer than anticipated. “We are not always in rock and have to slow down. As of right now [late April 2015] the ground is good, but we vary between degraded granitic materials and less degraded rock. The degraded material becomes like a clay as it disintegrates. It changes frequently and is not consistent — we may be in rocky conditions for 5 ft and then in soft material for the next 3 or 4 ft,” said Anderson.
The contractor must slow down the machine in such conditions, and in some sections muddy, watery material has required the use of pumps at the front of the machine to remove the liquid.
In the softer ground, cutter changes have been minimal. “We have changed two gauge cutters and one twin cutter at the 100-ft mark, which was during the first cutterhead check,” said Matt Weaver, Robbins field service technician onsite. “Just shy of halfway, we changed four gauge cutters and six face cutters and we anticipate this to take us to the end of the tunnel. This is a front-loading cutterhead so cutters can only be changed in stable geology. With changing ground conditions cutter checks can’t always be done at scheduled footage and you have to make the best judgment calls you can to be prepared for what lies ahead.”
Throughout the challenges, J.W. Fowler has been grateful for the presence of Robbins field service technicians onsite: “We’ve had two operators come out to help; when we first started the job there was one operator. They have been helpful and very knowledgeable about the machine,” said Anderson.
As the machine excavates, crews are erecting two different types of primary liner behind it. Four-flange liner plates were specified at either end of the tunnel, for the first 100 ft and the last 70 ft. The remainder of the tunnel is lined with ribs and lagging. “We have the liner plate to make sure the ends of the tunnel can be sealed up afterward and any water won’t migrate,” said Anderson. “As for the ribs and lagging, we are doing that in 5-ft sets, but we sometimes have to go down to 2.5-ft sets when the ground is very soft.”
Overall, says the contractor, the machine is performing well. Advance rates have been as high as 30 ft in two 10-hour shifts. “The Rockhead design is a good one. The best part of our machines and working for Robbins is that with every job comes some unique situations. Both our customers and field service team provide feedback and Robbins engineering has, in my experience, always been very open to this information. This allows our product line to constantly improve and provide our customers the best machine for their project,” said Weaver.
“While the unexpected conditions have had a dramatic impact on the expected production rates and the tunneling effort as a whole, the machine and the crews have done an admirable job of dealing with the conditions that have been encountered. Both men and machine continue to soldier on toward successful completion of this tunnel,” said J.W. Fowler executive vice president John Fowler.
Anderson was optimistic, as of late April, that the machine would reach the finish line shortly: “We will be at the extraction point in three to four weeks and then we will remove the MTBM. After that, the contractor will install the new 48-in. HDPE line throughout the whole tunnel. The new section of sewer line is scheduled to go online Sept. 1 of this year.
Desiree Willis is a technical writer for The Robbins Co.
Tags: May 2015 Print Issue