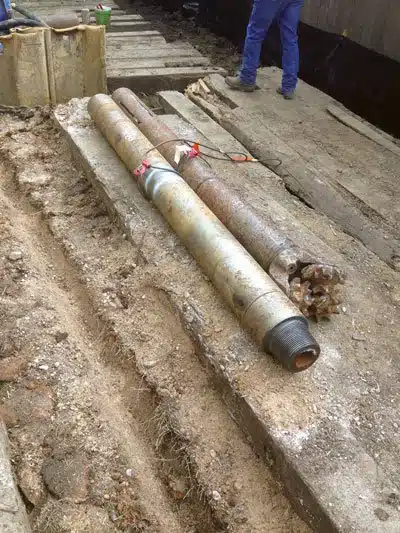
Comparing HDD Steering Methods
December 1, 2015
The gyro is heavier than a magnetic steering tool and is housed in a large, steel sub, approximately 8.5 ft in length and weighs up to 1,200 lbs.
As horizontal directional drilling’s (HDD’s) growth stabilizes, safety has become our leading issue.
The front line of drilling safely has to be avoiding strikes. Safe drilling requires good planning.
A safe plan requires three elements: Know the precise location of existing lines, know the precise location of the advancing drill bit and know and record the precise location of the newly installed line. All three relate to steering accuracy, yet far too many HDD engineers and planners do not know which steering method is the most accurate or why.
The laws of physics haven’t changed. When it comes to steering accuracy, the facts are the same as 30 years ago. DC tracking, known by many as Tru-Track, is the most accurate method available. The physics of DC tracking dictate that it is the most accurate. The majority of HDD veterans know this, but the industry’s unbridled growth has blurred the facts. Claims of “new” technology easily mislead the less informed. New isn’t automatically better and often isn’t even new.
Accurate steering begins with project planning. Select the most accurate steering method and design the drill for success. Shortcuts hinder accuracy. All too often, contractors are required to use less than the most accurate steering methods.
For liability, nothing is more important than knowing the precise location of the installed line. An accurate location is the lifelong responsibility of the owner. Future questions and liabilities will funnel directly to the owner. A line, installed via HDD, is often in an area where future construction will take place. Installed lines, of any type, simply have to be where they are supposed to be. It is critical to document and then communicate the drilled line’s precise location. If someone hits your line with a piling, excavation or even another drill, tomorrow or a decade from now, the liability remains. Did you select the most accurate steering system? Do you have accurate documentation? If not, the haze of uncertainty never fades.
DC tracking was the catalyst for HDD’s tremendous growth. HDD originated with Martin Cherrington about four decades ago. Growth was limited, with the holdup being the steering. In those early years, there was no reliable method to verify the drill bit’s location or direction. With the placement of a magnetic steering tool behind the drill bit, capabilities improved. The technique became known as wireline steering, because a wire, inside the drill pipe, connected the downhole steering tool to the surface computer.
Soon thereafter, a single event changed the pipeline and utility construction industry forever. The advent of Tru-Track, a patented surface tracking method, allowed the contractor to know the precise location of the drill bit at any time. By temporarily placing a thin wire, in a somewhat rectangle shape, along the planned drill path and inducing a momentary DC current (readily available through the DC welder already on most every rig site), which created a known magnetic field, the operator could take a stand alone survey (DC tracking’s most important attribute) and verify the magnetic steering tool’s precise location at any time.
The HDD boom began. Contractors could now drill in congested areas where HDD was more critically needed. The DC tracking accuracy is so precise that multiple pipelines can be safely installed via HDD on the same right of way. HDD contractors can know the precise location and heading of the drill bit, survey after survey, from entry to exit and have full knowledge of the exact exit location prior to the bits appearance. In addition, the length of HDD limits were extended as the DC tracking was so accurate that rigs placed on either side could drill toward each other and tap bit to bit.
Magnetic vs Gyro
Today, there are two methods of HDD wireline steering: magnetic and gyro. Walk-over is a third method of HDD steering that sometimes uses wireline type communications but it is not usually viable in larger diameter or deeper projects, therefore, not discussed in this context. Many in HDD assume the gyro is the newest steering product, therefore, most accurate. After all, isn’t it the tool of choice for oil and gas drilling? First of all, the gyro isn’t new and, in most cases, the oilfield’s tool of choice is the magnetic steering tool. The fact is that oil and gas sidetracks take place through steel cased holes. While in casing, they need a gyro, but, more often than not, once out of the casing they can trip and switch to a magnetic steering tool.
For HDD, the accuracy factor is even greater. The magnetic steering tool uses the surface tracking system to verify the tool’s precise underground position. The gyro can’t. For construction, accuracy is the number one goal and precisely plotting each survey is the difference between systems. For the protection of the owner, the distinction couldn’t be any more important. If you simply compare the DC surface tracking with a gyro, method against method, accuracy against accuracy, the magnetic steering tool wins hands down.
I listened to a gyro sales rep tell a group of HDD contractors that the big advantage to a gyro was that you didn’t have to set a coil on the surface. This should be a red flag to anyone concerned about safety. A gyro’s position cannot be verified, so, you never know where you are. Even if you use the DC tracking in conjunction with a gyro, the precise accuracy comes from the magnetic steering tool and the tracking, not from the gyro.
A magnetic steering tool is an accurate instrument that, in many cases, can be successfully steered without a surface coil. But, a coil makes the tool so accurate that drilling without it has come to be known as drilling blind, which has been frowned upon for a couple decades. For safety, standard HDD practices dictate setting a coil when possible and not take shortcuts. The gyro cannot be tracked; therefore, using the same definition, the gyro is always drilling blind.
Just how accurate is the DC tracking method? If asked, navigators could place a dime on the ground at the point the bit will exit. DC tracked shots are so precise the HDD inspectors monitoring each survey sometimes ask the driller to pull back and correct even the slightest deviation from the proposed plan. A gyro is never held to this standard, and can’t be, because they are never sure of its actual position. This type of directional oversight supports the HDD industry’s recognition and acceptance of the magnetic steering tool’s superior accuracy over the gyro.
DC tracking vs. AC tracking
Tracking improves accuracy but not all tracking methods are equal. There are two distinctive methods of surface tracking. The most accurate is a DC method. A temporary wire, geometrically looped, in a rectangle shape, laid on the surface, usually starting and ending at the power source, basically triangulates the tool’s position in relation to the magnetic field using each side of the looped wire. With nothing more than a known away distance, the DC tracking provides a standalone precise location. The AC method uses only one side of the wire. If not placed far enough away, the return wire interferes with the other wire. In addition, AC requires the user’s interpretation and entry of azimuth and inclination, creating an ever increasing error window. Not to mention the ability to manipulate the reported location. While tracking shots become a permanent entry in the DC steering reports, AC tracking shots are often discarded then recalculated, after the bit’s exit is determined, proving the original surveys were inaccurate to begin with. For those only familiar with AC and its questionable accuracy, the gyro is somewhat comparable. This isn’t the case with DC tracking. DC is far more accurate than AC or a gyro.
Size and Durability
There are major differences in types and brands of instruments used in the various magnetic steering tools. Some are better than other but, as in most cases, you get what you pay for. The magnetic steering tools are generally very durable, about 3 ft in length and 1 ¾ in. OD. They can be used in all but the smallest of HDD applications. They are in the 35-lb weight range and can be flown or shipped with relative ease. The gyro is housed in a large, steel sub, approximately 8.5 ft in length and weighs up to 1,200 lbs. Gyros, by comparison, are sensitive to shock/vibration and it often takes multiple tools to complete a rock job.
Set Up
I understand the gyro operator will not survey an HDD job and require the contractor to provide entry and exit coordinates. This will require the contractor to hire a surveyor or obtain the coordinates from some other source. Any errors are not the problem of the gyro operator. Most magnetic steering tool service companies use the onsite navigator to survey and set up a job and this is usually done while the crew is setting up the rig.
The Operator
The importance of well trained, experienced steering technicians/navigators cannot be over stated. Training never ends and annual proficiency verification is critical. There is no shortcut to experience.
Due diligence is not only selecting the most accurate steering method but to consider the entire package: The training and experience of the systems operator, not to mention ongoing technical support from the steering company’s office. Another consideration is the job completion package. Do the post-bore records and data provide industry recognized proof of where your product line is located? It should, after all, that is all you have.
Not all steering technicians work directly for the company you are hiring complicating insurance coverage and liability issues. Some steering companies employ independent contractors or share navigators with other companies having little influence toward their training or knowledge of their experience.
Conclusion
The HDD industry’s focus on safety, while displaying a lack of attentiveness to the accuracy of various steering methods, is a conflict. The good news is that this is a result of great growth and wonderful opportunity. While the HDD boom started as a result of precise steering capabilities the trend has been toward an acceptance of less accurate methods, if they are claimed as “new technology.” Paying more for something less accurate shouldn’t be acceptable. Comparing one type of tool to another isn’t practical if you fail to compare the accuracy of the entire method. When planning an HDD project, safety should be factored in all decisions.
The goal should be safety, therefore accuracy. Proven practices and procedures continue to be the foundation for success. Take the time to do it right applies to every other type of construction, yet steering shortcuts are often accepted and sometimes dictated, by self-proclaimed HDD experts. Knowledge of steering methods and its capabilities is a good indicator of actual HDD experience. Those who maintain a level of skepticism and research the facts will avoid future problems with steering and location for their clients.
John English is founder and president of Horizontal Technology.
Author’s Note: A rough draft of this article was sent to numerous veteran HDD experts including experienced navigators, current and former. Based on their replies, edits were made and some points were clarified. None disagreed with the paper’s theme. To highlight the fact that HDD steering is as much a political issue as a study of facts, some asked that their names not be mentioned. I thank each of them for their help and the sharing of their HDD knowledge.