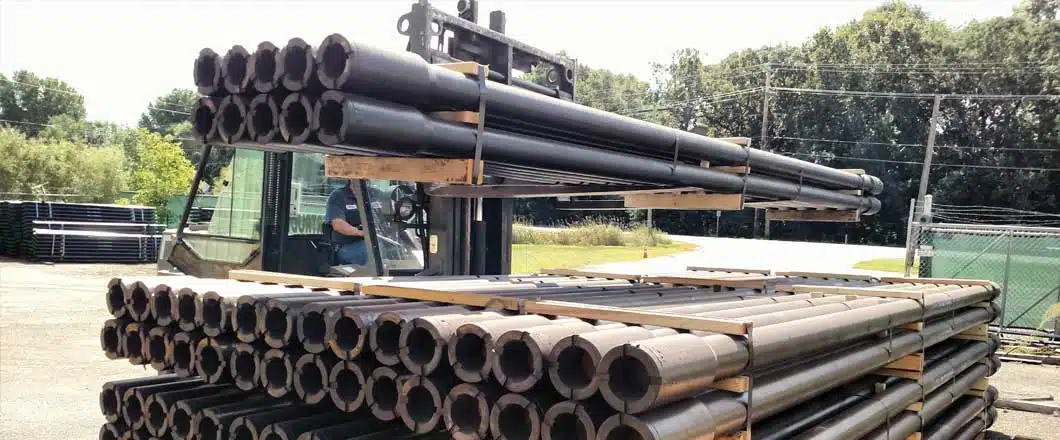
Common Misconceptions about HDD Drill Pipe
All horizontal directional drill (HDD) drill pipe is the same. If you have ever heard this said, I would exercise caution and recommend conducting some additional research before purchasing or drilling with just any pipe.
There are many misconceptions about HDD drill pipe and one of the most common is that people think that all drill pipe is manufactured the same way; however, this is not the case at all. There are primarily three different manufacturing methods used for producing HDD drill pipe.
RELATED: Why HDD Drill Pipe Bend Radius Matters
These methods are referred to as Integral Forged, Inertia Welded and Press Fit & Welded. The following is a general overview of these methods, which can be beneficial when considering which type of drill pipe to purchase.
Integral Forged Pipe is also referred to as One-Piece Forged Pipe because it is produced entirely from one piece of material, which means it will have the same chemical makeup for the threaded connections and the mid-body tube.
There are no welding processes used in the manufacture of integral forged pipe, instead, the ends of the raw material (green tube) are heated to produce a workable material, which are then upset to create the desired specifications; outside diameter, inside diameter and tong length required for the pin and box connections. Then the entire tube is heat-treated to a specified grade or hardness, which is almost always S-135 Grade for the demanding HDD application. Finally, the upset ends are precision machined and threaded.
Inertia Welded Pipe is produced from three separate pieces of material, the mid-body tube and two threaded connections (pin and box) or tool joints. Like the integral forged pipe, the ends of the mid-body tube are upset in order to form a thicker wall dimension creating a larger weld surface, which allows for a stronger weld zone connection.
Inertia welding, often referred to as friction welding, is a solid-state welding technique that actually forges metal together, in this case, the mid-body tube and the tool joints, without causing a melt to occur. This metal-to-metal fusion creates 100 percent weld penetration. After inertia welding, the weld zone is then machined and heat-treated to ensure proper strength and hardness.
RELATED: HDD Drill Pipe: The Bones of an HDD Project
Press Fit & Welded Drill Pipe — one of the oldest manufacturing processes — is similar to the inertia welded pipe in that it is produced from three separate pieces of material. The mid-body tube is also upset forged, but instead of inertia welding the tube and tool joints together, the mid-body is machined to extremely tight tolerances and the tool joints are pressed into the ends of the tube. Next, they undergo a MIG-welding process and, after that, the weld zone must be properly heat-treated to ensure precise strength and hardness.
Bend Radius Misnomer
Another misconception about HDD drill pipe is that people often think that if you oversteer or exceed the bend radius of drill pipe that it will instantaneously break or fail; and, if it doesn’t, then you must not have exceeded the bend radius.
Don’t get me wrong, pipe can and will definitely fail immediately if the pipe is severely oversteered and compromised, but this isn’t an either/or situation. In the vast majority of instances where bend radius is exceeded, the damage process has merely been initiated and the operator may not even know it occurred because there are no obvious signs or visible damage. If the pipe maintains its memory (ability to return to straight after bending) and there are no damaged or broken connections, you won’t even know that the pipe has been compromised.
As you continue using the compromised pipe, the metal fatigue and microfractures continue to worsen until the pipe ultimately fails. It can fail on a what would be considered a very easy bore and leave the driller perplexed as to why.
This type of failure can lead to questions about why they didn’t get the life out of this drill pipe that they got out of their last string of pipe and often have them thinking they may have received some defective steel or pipe. This is why knowing and understanding the bend radius of your drill pipe, along with proper setback and bore path planning is so important because once bend radius has been exceeded and the pipe compromised, ultimate pipe failure can occur anytime thereafter. It may not happen immediately, but one thing is for sure – you will be replacing your drill string sooner, potentially much sooner than you should be.
I would like to quickly make note of one other very common misconception with regard to drill pipe bend radius — understanding exactly how bend radius is interpreted. Many drillers and others in the industry think bend radius is the amount (feet) of pipe needed to make a 90-degree turn, when in actuality, bend radius is the amount of forward distance (feet) required to perform a 90-degree turn. It is easy to see how this could lead to drill pipe problems in the field.
HDD Drill Pipe String Lifecycle
How long does a string of HDD drill pipe last? Trick question or misconception?
Drill rods are consumables or wear parts, in fact, the most expensive wear parts on horizontal directional drills. Every contractor wants to get the most life out of their pipe, as reducing expenses directly drops to bottom-line profit.
RELATED: HDD Drill Pipe and Hard Band Hangups
Many people believe that a string of pipe should last “X” amount of time; however, many variables come into play throughout the lifecycle of a drill string that will directly affect the overall lifespan of the pipe. Ground conditions, operational factors and drill pipe maintenance all play key roles in determining the life of the pipe.
The ground conditions encountered during horizontal directional drilling are one of the most significant factors when it comes to wear and tear on the HDD drill pipe. For example, if most of your drilling is being performed in soft loamy soils your drill pipe will last significantly longer than if you are drilling in rocky soils or river crossings through cobble and chunk rock. This may appear obvious, but determining how much more, or less life too expect when factoring in ground conditions isn’t so easy. Pipe inspection techniques will need to be employed to determine how much life is remaining. Deflection damage and pipe rotating on rock will dramatically reduce the life of the pipe and that has to be taken into consideration when bidding work and forecasting expenses.
Drilling operations are also instrumental when it comes to the life of a drill string.
We already addressed setback and bore planning and how that can reduce the life of drill pipe. Another important item to be mindful of is drill pipe make-up torque.
Be certain to thread the pipe together to the manufacturer’s recommended make-up torque above ground, otherwise, the HDD drill pipe is at risk of over torquing downhole. This causes damage to the connections, such as flared boxes and mushroomed pins, which will significantly reduce pipe life, and don’t forget to use a high-quality thread compound for every connection made. Proper vise alignment is also critical. The drill pipe must be centered properly in the vise for make-up with the next connection, if not, stabbing damage to the threads and box shoulder can occur.
HDD drill pipe maintenance also goes a long way when it comes to maximizing the life of a drill string. The most difficult part about maintenance procedures is taking the time to do them.
Here are some good practices that will definitely extend the life of drill pipe:
- Conduct periodic visual inspections of the pipe and set any that are bent or showing pin or box damage aside for further repair or disposal.
- Clean or remove any foreign debris from drill pipe compound on the threads.
- If box ends are showing significant die marks, check vise jaws and replace as needed. Always replace the drive chuck or sub saver when racking a new string of pipe.
- Rotate the pipe in the rack to spread the wear evenly throughout the drill string.
- If you plan on storing any used pipe it is a good idea to flush the pipe to remove any drilling fluids, let it dry and replace the thread protectors.
Making the extra effort to maintain a drill string will definitely pay off in the long run and give you the best return on your investment.
Al Chancellor is in sales and marketing at Underground Tools Inc.