A Contractor’s Take on Mixed Ground Auger Boring
September 21, 2011
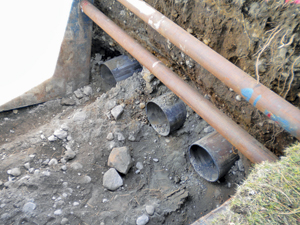
The Tahoe Forest Hospital, located in Truckee, Calif., needed three casings bored below its active main hospital for new utility and mechanical lines. The ground, however, consisted of mixed soils and colossal, hard granite boulders.
“We were worried about what the ground conditions would be under the existing hospital. When they built the hospital, they unearthed a 25-ft wide by 15-ft tall boulder that they left on the grounds as decoration. We knew it was highly likely we would encounter the same type of rock,” said Charlie Landino, foreman for Silver State Boring Inc. The contractor ultimately opted for auger boring using a 30-in. diameter Robbins Small Boring Unit (SBU-A) with mixed ground head to excavate the tunnels — the first time Silver State had used this type of cutterhead.
Project Setup
Tahoe Forest Hospital is an expanding healthcare center with a new cancer wing under construction. The hospital was in the process of designing the high-tech wing in autumn 2010, but needed to have all of the utilities in place before the new building could be built. Each of three pipelines, for the Tahoe Forest Hospital District Central Energy Plant Site Prep project, was designed to hold all bundled utilities the new wing would need, including steam, telephone, fiber optics, natural gas and water.
General contractor AM-X Construction & Excavation Inc. of Truckee, Calif., subcontracted three parallel 70-ft sections of the new pipelines, directly below the hospital, to Silver State Boring.
“There was a lot of concern from the hospital about the impact that noise and vibration might have on patients during construction,” said Rick Landino, owner of Silver State Boring. The chosen method needed to be both smooth and quiet, regardless of whether they were boring through soils or rock.
Choosing Mixed Ground Auger Boring
Though Silver State had extensive familiarity with Christmas tree, roller cone, and other types of ABM cutting heads, the contractor knew the particular geology at the site was not optimal for these types of tools.
“Other types of cutterheads wouldn’t have been in the realm of possibility here. There was no other way to drill it except with a disc cutterhead. The rocks were too solid and big to hand tunnel, and the hospital was active during operation, which meant we couldn’t use an air hammer because of vibration and noise,” said Rick Landino.
The company selected the SBU-A disc cutterhead, mounted with 6.5-in. tungsten carbide cutters, after careful consideration. “We had known about SBUs for a while, and I was helping out a friend that year at [industry tradeshow] and happened to have a look at one of the models there,” said Rick Landino.
The three 70-ft long bores, approximately 8 ft below the hospital’s foundation, were designed as jack and bore crossings. Rick Landino continued that Silver State was confident with their chosen boring method: “We were the only contractor to give a fixed price cost during bidding, and we guaranteed that we would come out the other side without any failures.”
Limited Space, Active Hospital
Digging the bore pit for launch was a challenge, as the older hospital building had many buried utilities — from fiber-optic to steam lines and sewer laterals — that needed to be cut and bypassed in order to excavate the site, measuring 13 ft deep and 20 ft wide x 36 ft long.
As with all Robbins SBUs, prior to launch, Robbins field service technicians went to the site to check on the ABM and SBU-A setup, and to train the crew on the machine.
“It turned out to be a pretty simple procedure to operate the machine. It wasn’t anything we weren’t accustomed to — and it actually was a little easier to use than other ABM cutterheads. We were apprehensive about the fact that you couldn’t remove the cutterhead to see the cutting face, but Robbins answered the questions we had and reassured us,” said Charlie Landino.
Silver State began each bore with a 24-in. thick concrete starting block to keep each bore on the correct heading. The contractor explained that the building setup resulted in a tight exit space, with each casing 4 ft apart and a 14-ft wide window in which to hole through. Each bore was monitored by pulling the auger string to check line and grade, though the short crossing lengths lessened the challenges. “The bores all went very straight. As long as you get the SBU started straight, it will just keep going,” said Charlie Landino.
The first of the three 70-ft bores began in October 2010. Restricted boring hours of 10 a.m. to 3:30 p.m. were imposed as the hospital was concerned about noise and vibration. In addition, the bore pit was in proximity to the building’s helicopter launching pad, resulting in a height limit for the contractor’s cranes. The three-person crew included a laborer, an ABM/SBU operator and a crane operator, who was required to keep the boom to below the height of the building at all times.
Boulder Challenge
About 25 ft in, the crew did hit a large boulder, though not as large as the one decorating the hospital’s courtyard. The first bore caught the edge of a boulder around 12 ft in diameter, but was able to maintain its alignment. The second bore drilled straight through the boulder, while the third hit mixed boulders ranging from 1 ft to 4 ft in diameter.
“The big rock we bored through was giving us rates of only about 3 to 4 in. per hour at one point. We were worried about a potential failure of the equipment and called Robbins. They said to just push a little harder, because the rock was extremely hard,” said Rick Landino. Though no tests were performed, Silver State estimated that the rock strength was close to 25,000 psi. The crew increased the forward thrust on the ABM, allowing the SBU-A to successfully bore through the boulder.
“There was no way another cutting head could have done this. It was very smooth when we were advancing through the rock and didn’t put too much stress on the ABM,” said Charlie Landino. Overall, advance rates for the duration of the project were in the range of 10 ft per day.
All three of Silver State’s bores were completed by November 2010. “It was low torque and low impact on the ABM, which we liked. It turned out that we didn’t even need to do cutter changes between bores,” said Rick Landino. After the first crossing, the hospital extended the boring hours, allowing the crew to start at 8 a.m. once it determined that vibration and noise were not a problem.
Overall, Rick Landino added, the crew was pleased with the SBU performance: “The boring method worked great, and reduced the impact on the building tremendously.” Silver State will be reusing the technology again in autumn 2011, on a 24 in. diameter bore in South Lake Tahoe, Nev., through similar soil and boulder
conditions.
Desiree Willis is a technical writer for The Robbins Co.
Mixed Ground Auger Boring
The Robbins SBU-A is a type of hard rock or mixed ground cutting head used with an auger boring machine (ABM). The circular cutterhead can be mounted with a combination of tungsten carbide bits, single disc cutters and/or multi-row disc cutters depending on the ground conditions.
The SBU-A , available in diameters from 24 to 72 in., can excavate hard rock or mixed conditions including dry soils, clay and alluvium, as well as cobbles and boulders from 4,000 to more than 25,000 psi UCS. For excavation, the SBU-A is welded to the lead steel casing. The ABM provides both torque and thrust to the cutting head, while a full-face auger is used for spoil removal.
During mixed ground boring, drag bits scrape soils from the face, while disc cutters effectively excavate boulders and sections of rock. Muck scrapers scoop the muck into large openings in the cutterhead that allow a smooth flow of muck from the face to the auger string.