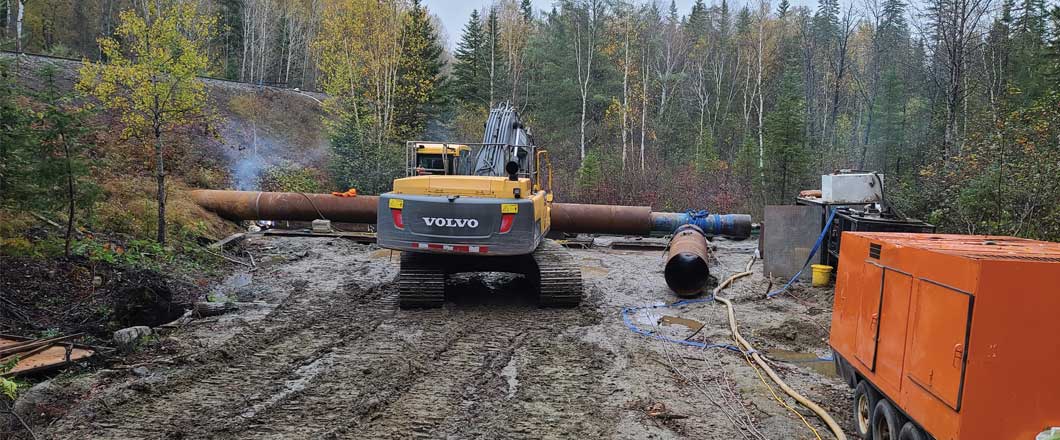
Working for the Railroad – Pipe Ramming Job Takes LTL Directional Drilling to Remote Locale
Over the course of eight days in September the pipe ramming and auger boring crew for LTL Directional Drilling were working for the railroad to help improve drainage and alleviate over the tracks flooding on a key section of the line.
Pipe ramming and auger boring have been the go-to installation method for pipes when travelling under railroad tracks for many years. As such, LTL Directional Drilling – a division of LTL Group in Thunder Bay, Ontario, have completed railroad jobs in Saskatchewan, Manitoba and Ontario often in remote locations. This project – approximately 1,500 km northwest of Toronto – was no exception.
“[We were] Improving the drainage course beneath a key stretch of railroad,” says Brandon Erhardt, pipe ramming and auger boring supervisor for LTL Directional Drilling. “In previous years, the railway had major flooding issues at this location. At one point, the water was flowing over the rail ties. The locations were blind drains which became silted and plugged over the years.”
The original plan, when first contacted by the railroad, was to complete the project in early 2021, when a significant portion of the water would be frozen. At an early site visit, the contractor and railroad engineering teams were met with a significant amount of snow that was piled 3-ft high in some locations. They could not get an accurate lay of the land and formulated some options for the railroad.
Recommended Approach
LTL Directional Drilling recommend installing a 36-in. smooth wall steel pipe using pipe ramming due to the elevation, proximity to signals and existing fibre-optic cables, as well as previous experiences with unknown soils and railway fill on similar projects. The pipe lengths were estimated at 130 and 90 ft.
The two blasted rock drainage tunnels – referred to as the western section and eastern section – were estimated to be about 130 ft and 90 ft long. Together, they created a horseshoe-shaped drainage course. The western section was approximately 3 m higher than the eastern section with water flowing from the south to the north through the western section and north to the south in the eastern section.
“Our actual install was 120 ft and 80 ft. We had to do the east pipe first, to alleviate the water backed up by that location, before doing the west pipe, otherwise we could have compromised the embankments,” says Erhardt.
The work required daily rail trips for the crew – approximately 1,500 m each way. Though Erhardt notes he has worked some projects that the railway commute to the site is 30 km each way. All the equipment that required transport via a lowboy trailer was loaded on to a hytracker on the main line, about 10 miles away, and hauled in. Pipe deliveries were also made to a main rail yard and shipped to the site.
Robust Equipment
To complete the job, LTL Directional Drilling called upon its Grundoram pneumatic pipe ramming tool from TT Technologies – in this case the 24-in. Taurus – mated to a Sullair 1600H compressor and a Barbco 48/60-950 auger boring machine. It also used its Volvo EC300 excavator to move the equipment and the 36-in steel pipe from Trinity Pipe.
“We’ve tried auger boring through in similar scenarios, but it takes an astronomical time because every time you hit a rock you have to send someone into the pipe to pull it out. Whereas with pipe ramming, we reinforce the front of our pipes to three times casing thickness and we’ll either break it or move it,” Erhardt says. “We rammed the casing in open-ended, so it takes all of the material and pulls it inside the pipe. Once we’re done, then we will run a set of augers through it to clean the pipe and remove all of the materials.”
The LTL Directional Drilling team took surveys and found the approximate bottom of the inlet, set line and grade, and proceeded to ram the pipe in with the Taurus Hammer using the 1,600-cfm compressor. The lead 36-in. pipes were fabricated by the crew off site, to expedite install. Due to the nature of railway fill, the contractor decided on 0.75-in. overcut bands, on 0.75-in. pipe, with custom machined mud injection blocks, allowing separate control over annular and internal lubrication.
The pipes were rammed in 40-ft lengths with pipes fully installed in one day at each site. “The TT [Technologies] Hammer, performed flawlessly, installing the pipes at an average rate of 55 seconds per foot over the course of the entire drive at 150 BPM,” Erhardt says.
Following the pipe ramming install, the pipes were cleaned using the Barbco auger boring machine. Augering operations were performed using a wireless remote. All non-necessary equipment was removed from the area, and augering commenced. Augers ran out 10 ft beyond the end of pipe and debris, brush and dirt were pulled back. Because the crew was working in live flow conditions, 20 ft of auger was left in the pipe to slow the water until the boring machine could be removed. Once all the equipment was removed, the final 20 ft was removed.
All told, it took the LTL Directional Drilling team eight days from unload to reload.
Mike Kezdi is managing editor of Trenchless Technology Canada.