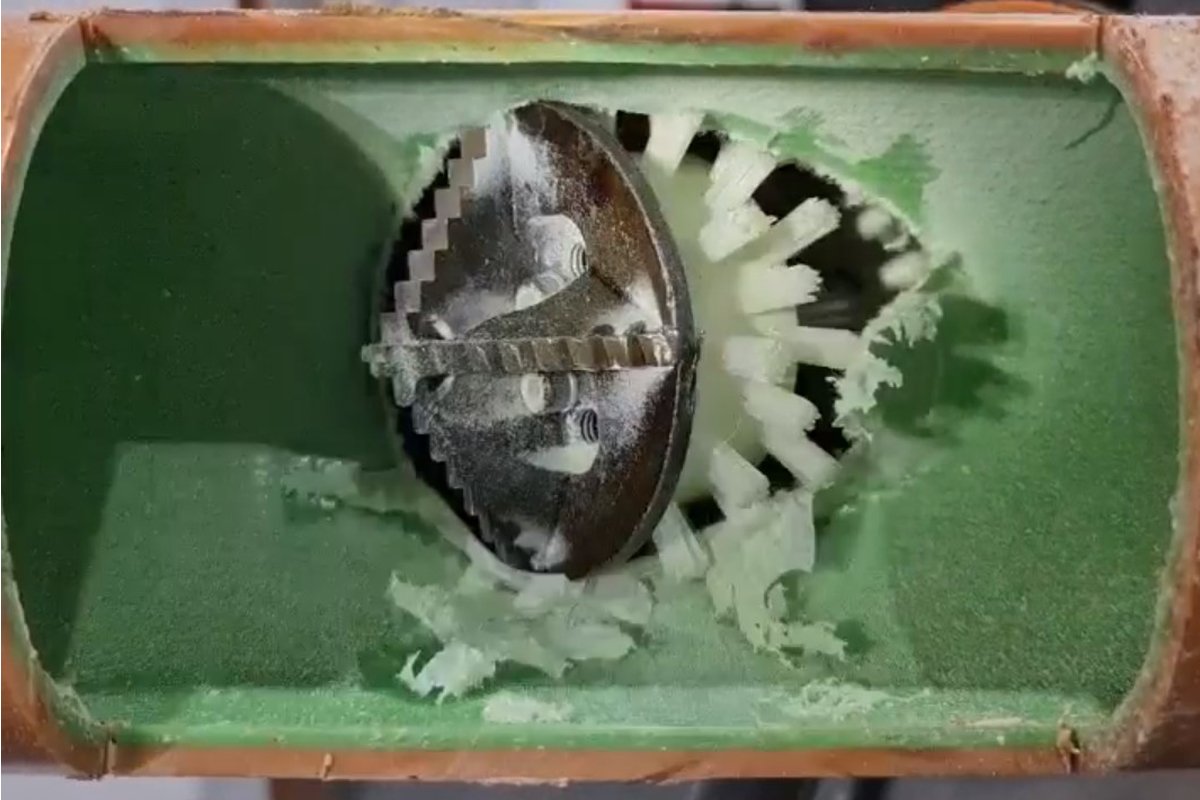
What You Need to Know about Lateral Reinstatements
Whenever cured-in-place pipe (CIPP) liners cross over a pipe connection and are cured, it is necessary to reopen the overlapped pipe to reestablish flow by performing a lateral reinstatement.
If you are new to CIPP, or simply want to improve your performance, there are some important steps and considerations that will help take some of the stress and risk out of lateral reinstatements.
Inspection, Planning and Preparation
Prior to the start of any CIPP project a thorough CCTV inspection should be conducted to assess the condition of both the main and lateral pipes, identify potential issues such as blockages, and pinpoint the locations and clock positions of lateral connections.
Selection of Appropriate Reinstatement Technology/Equipment
Equipment choice can depend on various considerations, such as the pipe’s diameter and composition, type of lining material, and current state of the lateral connections.
Robotic cutters stand out for their high precision and speed yet necessitate advanced training and entail higher initial purchase and maintenance costs. Their utility might be constrained in scenarios involving smaller diameter pipes due to a narrower range of suitable options.
Conversely, backside mechanical cutters present a more budget and user-friendly solution. But their applicability can be affected by specific challenges such as the location and length of the access pipes. Also, before the liner is installed, this method requires pre-cleaning the lateral connection pipes through which the reinstatement tooling will pass. Though time-consuming, it is a critical step needed to ensure smooth passage of reinstatement tools to the liner’s backside and prevents the accumulation of scale/debris on top of the liner which can slow down reinstatements and diminish tooling lifespan.
Expertise and Training of Personnel
Selecting the right equipment is essential, but the success of CIPP lateral reinstatements is fundamentally reliant on the proficiency and training of the personnel executing the work. The complexity of the task and the skills required to effectively reinstate lateral connections can vary based on the chosen equipment and methodology. Nonetheless, the presence of skilled and thoroughly trained personnel is crucial to ensure reinstatements are performed safely and accurately, thereby minimizing the risk of damage to the liner and surrounding infrastructure.
Resin Slugs, Step Heat Curing and Pre-Liners
Resin slugs, excess resin that accumulates and hardens within the lateral connections during the lining process, are a challenge in lateral reinstatements.
Causes include over-saturation of resin, improper liner wet-out, high curing pressures, and resin expansion during heat curing. Resin slugs increase reinstatement times and hinder robotic cutters which may not be able to reach fully up the lateral connection and prolong mechanical backside reinstatements significantly since the resin debris cannot be removed until the initial opening is made.
To mitigate these issues, attention to resin volumes and curing pressures is crucial. Additionally, step curing, or heat curing in stages, is an effective but often underutilized strategy. This involves initially setting a lower temperature to partially solidify the resin, then gradually increasing temperature and pressure until the final curing temperature, pressure, and curing time are achieved.
In cases where resin slugs persist despite these measures, employing a pre-liner offers another solution. While typically used to prevent resin washout or to span gaps in the host pipe, pre-liners can also trap excess resin, preventing it from migrating up the lateral connections.
This is particularly beneficial in UV/LED curing systems, where the challenge often lies in uncured resin beyond the reach of the curing light. By containing the resin, the curing light ensures complete resin curing, avoiding the complication of uncured resin that can quickly gum up reinstatement tooling.
Risk Management and Contingency Plans
Given the complexity and potential challenges of CIPP reinstatements, it’s important to have comprehensive contingency plans in place for the multitude of scenarios that could occur:
- Equipment Malfunction: Keep backup equipment readily available to minimize downtime. Perform regular maintenance and pre-operation checks to reduce the risk of in-field failures.
- Misaligned Cutting: If using a robotic cutter from inside the liner pipe, use pre-installation CCTV inspections to accurately map and mark lateral positions. If misalignment occurs, evaluate the feasibility of implementing a Tee or Wye Connection Collar, a felt/resin spot repair, or additional cutting to rectify the issue.
Tee and Wye Connection Collars
The use of Tee or Wye Connection Collars is highly recommended as it will help provide a fully sealed connection. For whole system renovations, combining liners and connections in steps from the main, at each tie-in, and up to the highest points helps ensures sewage will not penetrate the joints as they are overlapped (similar to overlapping shingles on a roof).
Post-Reinstatement Inspections
Post-reinstatement inspections are vital quality control to confirm that lateral connections have been correctly reinstated and that both the liner and pipe maintain their integrity. Any potential issues that could compromise the system’s functionality can be identified and immediate solutions implemented.
Successful lateral reinstatements require a methodical approach encompassing everything from the initial inspection and thorough preparation to the selection of equipment. Furthermore, resin management and trained operators performing the reinstatement process are pivotal. Each phase is critical, which necessitates a thorough understanding of the task at hand to mitigate risks and enhance project success.
Ryan Boldan is global learning solutions director at Picote Solutions.