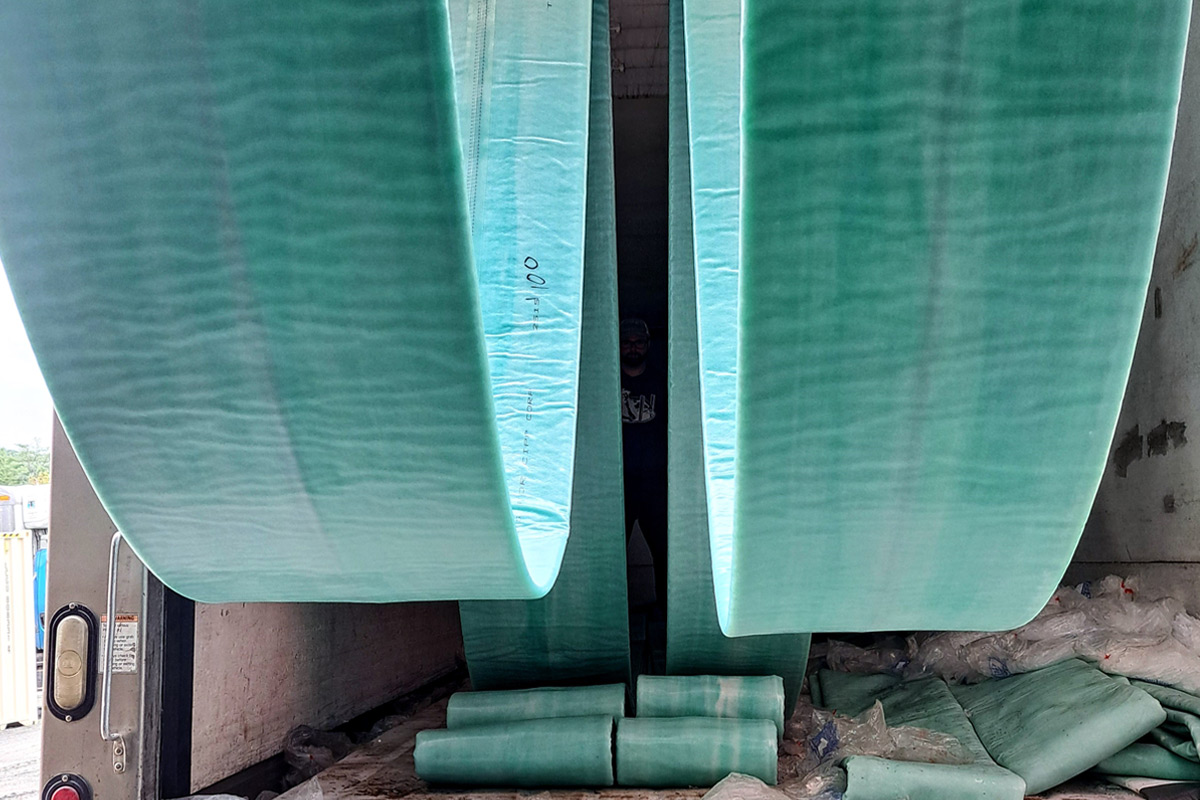
What to Keep in Mind when Handling CIPP Resins
Proper resin storage is an often-overlooked practice in cured-in-place pipe (CIPP). It is easy to take for granted that the resin will stay liquid until initiated and heated. However, proper handling and storage are necessary to avoid issues.
Let’s start with a basic understanding of what resin is. Polyester resins are made by reacting phthalic acid and polyols to form a liquid made of long molecular chains called an alkyd. The polyester alkyd would solidify at room temperature, so a reactive diluent, typically styrene, is added to keep the resin fluid at room temperature.
During cure, heat or light break the initiators apart to form free radicals, which are highly reactive molecules. The free radicals form bonds between the polyester and styrene in a chain reaction where each bond formed from a free radical creates a new free radical, propagating the reaction. The polyester and styrene combine to form one macromolecule, which solidifies the resin. Vinyl ester resins have a similar chemistry to polyester resins.
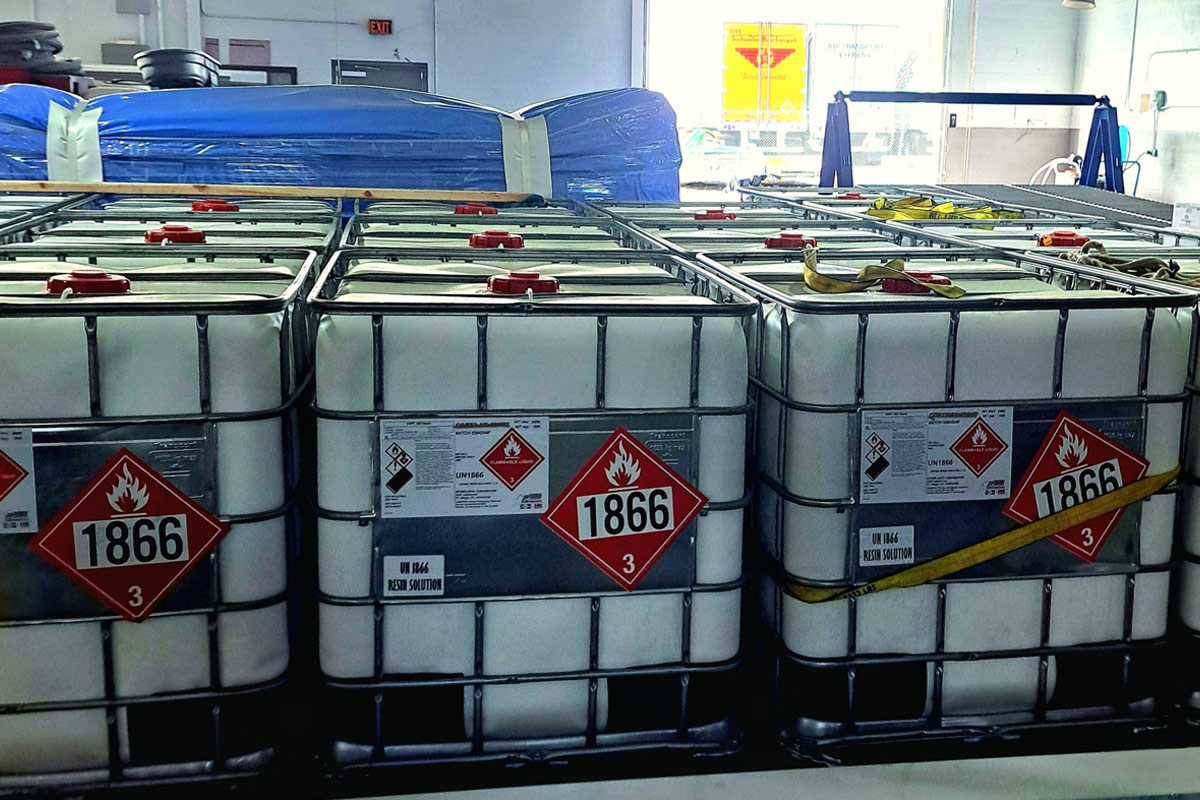
This is ideally how resins work. However, free radicals can also form spontaneously. It is infrequent, but if it happens enough, the same chain reaction can start, resulting in gelled resin.
CIPP Resin Stability
The two largest factors that affect resin stability are heat and time, which are interdependent. Time gives the resin more opportunities to form free radicals and heat speeds up the process. Heat is like a fast forward button. Resin stored at a higher temperature will have a fraction of the shelf-life of resin that is kept cool.
When speaking of heat, an important concept to understand is heat history. This is a profile of all the heat that the resin has experienced. This is important because heat exposure cannot be undone. Cooling the resin down will slow the formation of new free radicals, but the ones already formed do not go away. Like a leaky bucket, you can try to slow the leak, but the water that has already leaked out is gone.
The first thing to look at when storing resin is avoiding excess heat. This does not mean the resin needs to be kept at -20F, but avoiding temperatures above 80F is good practice. Ask yourself, do your tanks have cooling coils? Do you store the resin outside and exposed to the sun? Is there a heater or exhaust near your resin containers? These are some ways heat can infiltrate your resin.
The second way to mitigate these threats is to use your resin in a timely manner. Inventory management is important. If you get a new shipment of resin, hold off on using it until you have finished using the old resin. “First in, first out” is a common saying in the food industry, and it applies here too. Also, make sure not to overstock resin.
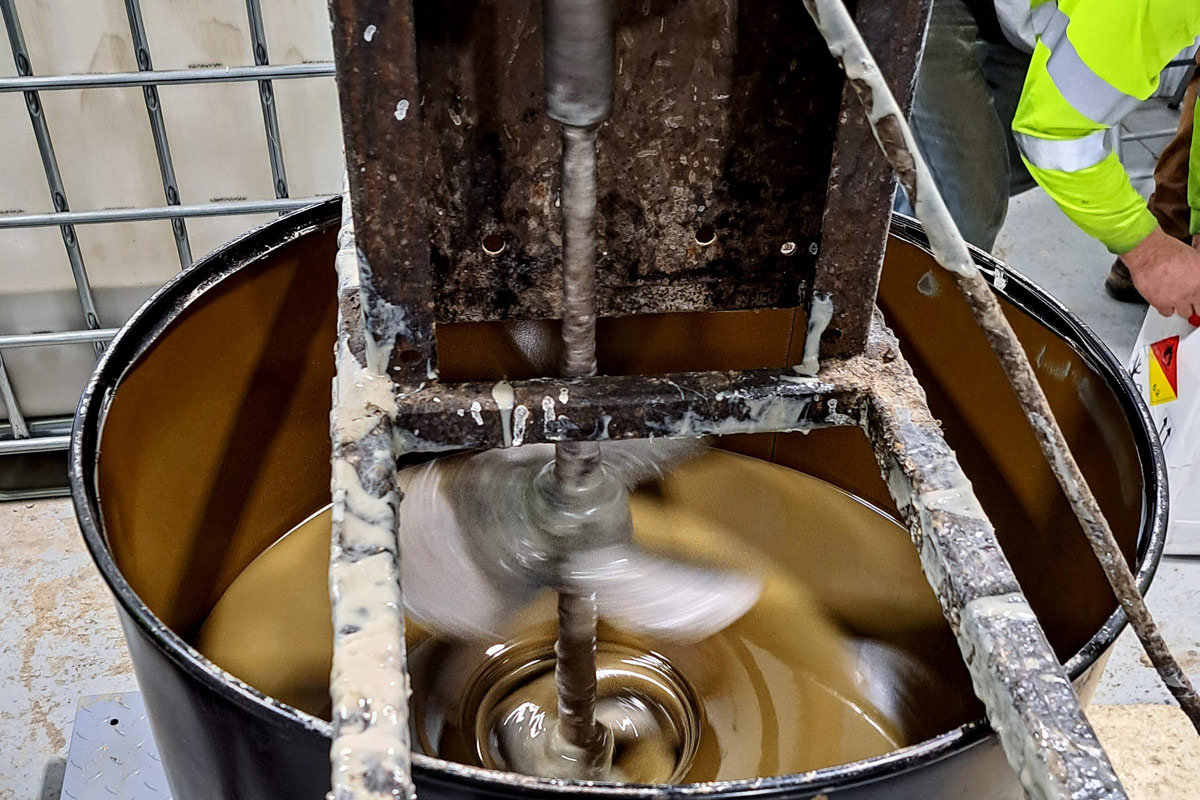
Gelled resin is not the only concern when storing resin. Stagnation can cause fillers to settle and localized gelation to occur. Tanks may not be uniform in temperature. Without agitation, resin around hotter sections of the tank will age faster than the rest of the tank. Mixing keeps the resin temperature uniform.
Mixing also keeps fillers in suspension. Enhanced or filled resins can settle over time forming a cake layer at the bottom of a tank. This layer can build up and solidify causing blockages and requiring cleaning, which can be expensive. Tanks should have mixing blades or recirculators to prevent this. Drums and totes will not have constant mixing, so they should be mixed with an industrial mixer prior to use.
It is also important to keep your resin sealed when not in use. This keeps styrene vapors enclosed. It also keeps moisture and contaminates from getting into the resin.
Once the resin has been initiated, it becomes more sensitive to heat, and more care is needed to control the resin’s heat history. Before pumping the resin, check to make sure the dry liner is not hot. After wet-out, cool down the liner quickly. A liner stacked tightly acts as a solid mass of resin, which takes time to cool down. Stacking ice between the layers will speed up this process.
It is often assumed that once the liner is in the refrigerated truck, it is cold enough, but this is not necessarily the case. The temperature inside the truck is not uniform. Liners touching the walls will be exposed to the temperature outside the truck. The cooling unit may also build up heat even as it puts out cold air.
The liner needs to be installed in a timely manner. The catalyzed stability can be extended by keeping the liner cold, but it is not worth testing the extent of this with a wet-out liner. Heat exposure that you were unaware of could have shortened the catalyzed stability. It is best to avoid long-term storage of a liner no matter how cold it is kept.
Care is needed during installation, as well. The liner should be kept out of direct sunlight. This includes UV-cured liners. While the outer foil reduces light contamination, it may not block all of it. Be careful not to let the liner sit on hot asphalt either.
By managing your inventory and avoiding heat contamination, the resin should remain fluid and ready for use for the extent of its shelf-life. Monitor your facility for any changes that may introduce heat, and make sure the oldest resin is used first. For additional information, contact your resin supplier.
Bill McElroy is product manager-CIPP at Interplastic Corp.
Latest Posts
- Maximizing HDD Tooling Longevity – Inspection, Maintenance and Replacement Tips
- Beneath the Frost: Trenchless Technology for Winter Resilience
- NCDD Completes HDD Intersect Under the Roanoke Sound
- Epoxytec Announces Winner of Manhole Photo Contest
- Watts Announces 2025 Backflow Hero Award Recipients