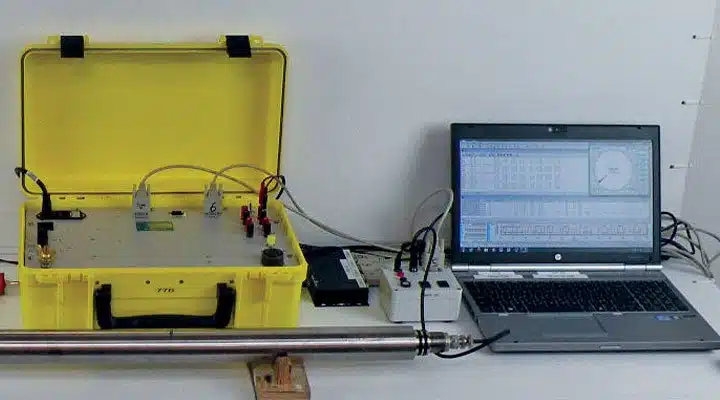
What’s Electro-Magnetic Technology?
EM Technology Brings Strong Reputation from Oil and Gas industry to Trenchless Operations
The use of Electro-Magnetic (EM) technology for the transmission of directional drilling information has been growing in the industry for many years. EM technology is now starting to find its way into the trenchless industry, but many observers are still skeptical of the performance and reliability of systems based on EM. With flexibility in operating environments and support for pressure monitoring, EM systems have matured into an important part of the directional drilling landscape. EM Technology is now being successfully used in the directional drilling industry across the globe for a variety of downhole operations.
EM Wireless Communication, How Does It Work?
The EM signal transmission is based on “drill-string-earth-telemetry.” The downhole system utilizes an insulation point in the drillstring commonly referred to as a ‘gap sub.’ This allows the drillstring to be used as a conductor, like a wire, to bring the signal to the surface. The surface equipment consists of a very sensitive volt meter and measures the voltage between the drillstring and the earth. This voltage is processed through a digital signal receiver that decodes the signal and displays information to the operator.
In a variety of conditions, EM has produced excellent results. The oilfield and coal bed methane industries have achieved measured depths of deeper than 5,000 ft on a regular basis and greater than 10,000 ft under ideal conditions. These systems can be used to transmit data from a wide range of sensors, making their application to a broad range of job types.
The Specifics Data Rates and Ranges
Common questions about EM technology include transmission frequency, data transfer rates and information update intervals. Most EM systems work in the extremely low frequency band, with transmission frequency between 4hz and 24hz. A well calibrated system would be able to match the baud rate to the transmission frequency, thereby producing a data rate as much as 24 baud.
EM system manufacturers have met industry needs by using an intelligent downhole processor that optimizes the most useful data to the operator before it is sent to the surface. The more data that is processed and analyzed by the system downhole, the more useful that data is at the surface. The system takes many sensor samples and transmits one high quality data stream via EM to the operator.
Why do some operations choose EM Systems?
The main advantage of the EM system is the cost savings and risk reduction in using wireless transmission instead of the setup and maintenance required traditional wired systems. In order to support wireless operation, the EM systems rely on batteries for independent operation downhole. The power consumed by operating the sensor and EM telemetry can be significant. An intelligent EM system makes serious efforts to minimize battery consumption to maintain operations downhole. As a result, manufacturers have optimized energy use to power only the sensors during sampling and transmitters only during signal transmission. A standard feature of EM systems is an optional sleep mode when the tool is left in the ground overnight or during periods of rig maintenance while in hole.
Under easy to use power conservation methods, one battery often lasts between three and seven days of operation depending on the system configuration. Batteries are available in a variety of sizes and capacities to support specific job needs and can be stored safely on the job site until needed.
Even though the utilization of EM technology is well known in the oilfield, the information available about job history in the typical trenchless market is not widely available. As this technology generates data from successful jobs it will be important to share this information across the customer base to further generate the confidence in the technology
What drilling sensors are compatible with EM systems?
The EM telemetry can be adapted to any sensor type. The duty cycle, transmission rate, data selection can be tailored to any specific sensor to meet the job requirements. EM tools can also be equipped with flash memory and configured so that all measurements made during the downhole operation and be retrieved when the tool is brought to surface. In some cases, it is even possible to sample the data at a rate higher than available for transmission and then send the data to the surface at the available transmission rates in a batch mode.
The intelligent EM system can select from a wide variety of sensors and adapt to EM operations with the standard magnetic directional sensors available in the industry. This allows for normal dead reckoning guidance and since these sensors are the same sensors commonly used in wired systems, the same algorithms can be applied on the surface. It is important to understand the separation of tasks between the sensor that takes the measurement, and the transmission method that sends the data to the surface.
EM Systems and Pressure Sensors
An excellent application for EM telemetry is for pressure monitoring in real time. EM telemetry has long been used in Drillstem Test (DST) in the oilfield and the application to reaming and pullback in the trenchless industry is a natural evolution. An EM system equipped with a pressure sensor can constantly monitor pressure and allow the operator to react immediately to pressure loss. In many jurisdictions, operators can be subject to significant compliance or liability costs if drilling fluids are lost in operation. Governments and municipalities around the globe are in various stages of considering mandating pressure monitoring regulations for trenchless drilling operations.
Accuracy and Compatibility with Non-EM steering methods
Concerns about the accuracy of EM telemetry data have been addressed by the industry. Vibration and unanticipated magnetism present challenges to the readings of all sensor based directional drilling systems. EM tool manufacturers have addressed this known issue by cross-referencing measurements in the on board processor and flagging the operator if any discrepancies in measurement occur.
EM tool manufacturers and operators can configure a system with DC Coil Integration, offering an independent way to verify steering in real time. While unexpected changes in the earth’s composition or unknown items in the drill path may throw off one system, running both systems simultaneously can cross reference results to offer the best possible picture.
The capabilities of EM technology have been proven to be cost-effective and reliable over decades of use in the oilfield. Over the past thirty years, the technology has continued to evolve and become even more cost effective to operators. As the trenchless industry demands more precision and cost efficiency, EM steering systems continue to serve as a powerful tool to get the job done.
James Harrison is president of Boregyde Inc. and Kasey Gardner is dean of the Behavioral Social Science Division at Sacramento City College.