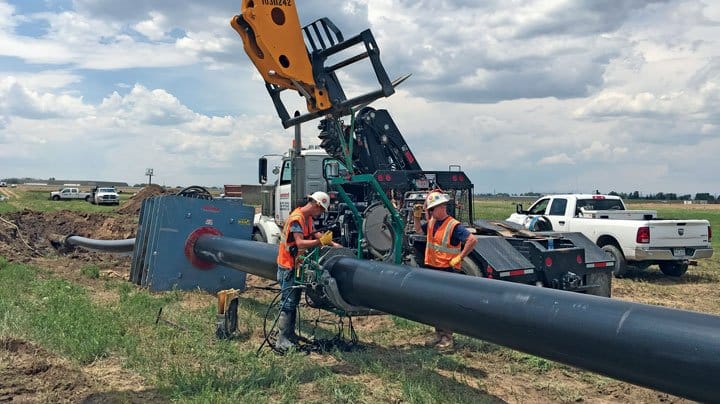
Water Relining in Laramie, Wyoming
Older pipelines can pose a host of issues for potable water infrastructure. Assessment of a 20-in. coal tar-coated, internally lined, steel drinking water transmission pipeline built in the mid-1940s in Laramie, Wyoming, resulted in the need for rehabilitation.
While the coating posed no health risks according to the Wyoming Department of water quality, after nearly 70 years of service, the client sought to rehabilitate the line to create a barrier between the coal tar coating and the city’s drinking water.
RELATED: Project of the Year 2017 Rehabilitation Honorable Mentions
Located along Highway 230 on a right of way regulated by the Wyoming Department of Transportation (WY-DOT), the pipeline transports water from Laramie’s water treatment plant down to the city below, losing roughly 2,000 ft of elevation along the way. Any solution Laramie would use to rehabilitate the line would require WY-DOT approval and permitting. Because of scheduling challenges posed by seasonal flow variation and the 18-mile length of the line, the city expected the project would need to be completed in three phases over three years.
Given the variety of possible solutions available, along with permitting challenges, the city sought complete design-build proposals for various trenchless options. Design-build proposals allowed the city to objectively evaluate the technology, installation plan, permitting challenges, disruptiveness, schedules, cost and value of each alternative. After evaluating proposals for solutions that included pipe bursting, sliplining, CIPP and full replacement, the Tite Liner system was selected. Provided by United Pipeline System, an Aegion company, the Tite Liner system is a tight-fitting compressed fit thermoplastic lining system suitable for new or existing pipelines.
When compared to the other alternatives, the Tite Liner system offered multiple advantages. Because the original pipeline required no additional structural reinforcement and could support external loading, a thin HDPE liner would provide sufficient internal loading support at a relatively lower cost. In addition, unlike other alternatives, the Tite Liner system can be installed without removing the existing coating since it relies on a compressed fit and does not have to bond to the host pipe. The system requires minimal cleaning and the installed system often results in increased flow characteristics.
The Tite Liner system can be installed without removing the existing coating since it relies on a compressed fit and does not have to bond to the host pipe.
The Tite Liner system uses a thermoplastic pipe liner that has a larger outside diameter than the inside diameter of the pipe it protects. On a typical installation, a winch cable is sent through a section of the host pipeline and attached to the liner pipe. The winch pulls the liner pipe through a roller reduction box that temporarily compresses its diameter.
This temporary radial reduction provides sufficient clearance for the liner to be pulled into the pipe. Once the liner is pulled in and the tension is released, it expands to create a tight fit against the inner wall of the pipe and end terminations are attached.
RELATED: Palm Beach, Florida Goes Trenchless to Renew Force Main Along Intracoastal Waterway
Although the client had previously used Aegion’s InsituMain CIPP product to rehabilitate some other water pipelines, this project marked the first time the city used a compressed fit thermoplastic liner solution. Not only would the solution provide a tight-fit liner for the city’s drinking water supply, United Pipeline Systems was able to rehabilitate all 18 miles in one phase and in a fraction of the time the city originally estimated.
Installation Overview
The project was completed in 46 separate installation sections, including several continuous sections in excess of 3,000 lf. The contractor also performed 14 lateral connections. These existing lateral services were tied into new freestanding high-density polyethylene (HDPE) DR13.5 reducing tees.
After installation of the liner, pressure testing was done on the line to confirm the Tite Liner system met design requirements.
RELATED: 12 Must Read Trenchless Features
A challenging project due to proximity to an active highway and roads, the project was completed on time and on budget in 18 weeks. During installation, United worked with the community to ensure minimal traffic disruptions along with zero safety incidents.
The owner noted, “It was great to work with Sean Borris and the team at United and we hope to work with them again in the near future.”
Jayne Shepherd is senior marketing communications specialist at Aegion Corp. Sean Borris is project manager at United Pipeline Systems.