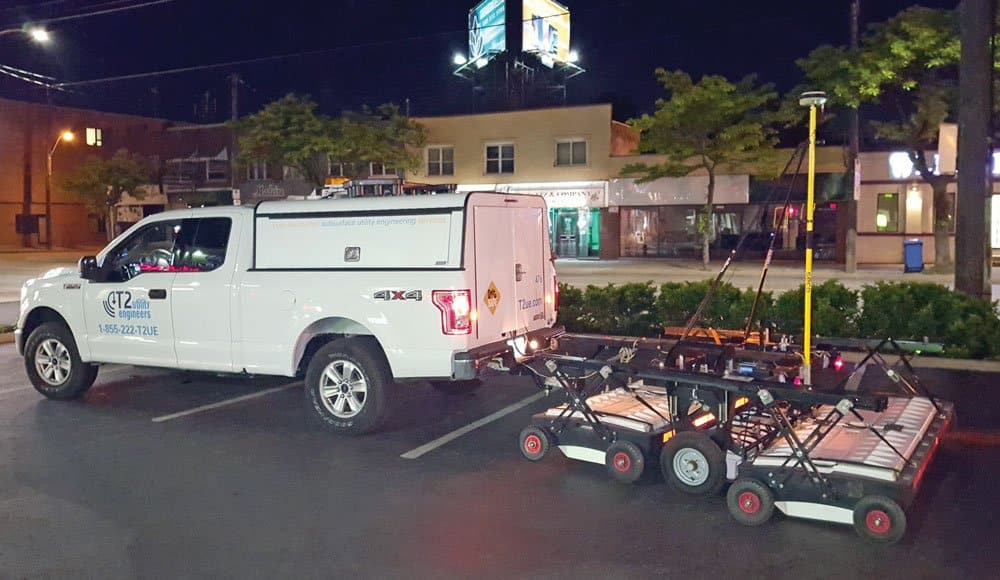
Innovations in Mapping Underground Infrastructure on Light Rail Transit Projects
Managing utility relocations typically presents one of the largest risks associated with delivering major capital infrastructure projects. Understanding the locations of all utilities, both above ground and subsurface, using an efficient utility coordination process is the essential first step in managing utility risks.
The above ground utility infrastructure can be quite easily and accurately located and mapped through a topographical survey of the project area. However, accurately locating and mapping subsurface utilities poses a greater challenge. Over the past couple of decades Subsurface Utility Engineering (SUE), a discipline of civil engineering, has developed ways to tackle the challenges associated with locating and mapping underground utility infrastructure. SUE can utilize technical means (i.e. geophysical technology) and non-technical means (i.e. historical drawings and records) to gather the subsurface infrastructure information.
RELATED: SUE: It’s Not Just Utility Mapping
To ensure consistency and transparency in the SUE industry, the American Society of Civil Engineers (ASCE) developed the “Standard Guideline for the Collection and Depiction of Existing Subsurface Utility Data” (ASCE 38-02), which describes a dependable system to classify the quality of the subsurface utilities mapped on engineering drawings. Based on the importance of accurate utility mapping, this article will briefly highlight the conventional SUE technologies (i.e. electro-magnetic (EM) locating equipment, ground penetrating radar (GPR) and closed-circuit television (CCTV)) and specifically discuss the innovative SUE technologies (i.e. Panoramo Manhole Scanner, Light Detection And Ranging (LIDAR), CCTV with side launch camera, Stream Multi-Channel Ground Penetrating Radar (MCGPR) and 3D Modeling).
These innovative technologies were employed to gather utility data and then map the subsurface information on two large current transit project for Metrolinx in Ontario, Canada.
In addition, this article will delve into the utilization of the SUE information to create accurate 2D maps and 3D models of the subsurface infrastructure and the application of the SUE information to manage the utility risk through effective utility coordination during the planning and design phases of the light rail transit (LRT) projects.
The LRT Projects
In September 2008, Metrolinx — the provincial transit authority in Ontario — launched a regional transportation plan, “The Big Move,” which is a 25-year, (CAN)$50 billion plan for a coordinated, integrated transportation and transit system in the Greater Toronto and Hamilton Area (GTHA).
Two projects that formed part of “The Big Move” were the Hurontario (HuLRT) and Hamilton (HaLRT) LRTs. The proposed HuLRT project will be a 22-km, north/south, LRT line that will be located along Hurontario Street between Brampton’s Gateway Terminal in the north and the Port Credit Go Terminal in the City of Mississauga in the south. It will feature 22 stops throughout the 22 km. LRT line. The proposed HaLRT project will be a 14-plus km, east/west, LRT line that will travel along Main Street, King Street and Queenston Road. It will feature 17 stations from Eastgate Station in the east, through downtown Hamilton to McMaster University in the west. Both the proposed HuLRT and HaLRT routes will be located on existing, utility-congested road corridors. The proposed routes required a progressive Subsurface Utility Engineering (SUE) program to accurately locate and map the subsurface infrastructure. To accomplish this locating and mapping challenge a progressive SUE program was implemented utilizing standard and innovative SUE technologies.
SUE Investigation
The technical advisory team hired T2 Utility Engineers (T2ue) as part of the team for the two projects. T2ue used a progressive SUE investigation and followed the ASCE 38-02 principles on both the projects. Historical utility drawings and conventional geophysical technologies (i.e. electromagnetic pipe and cable locators, CCTV, GPR) were used as the initial tools in determining the horizontal and vertical alignments of the subsurface utilities along both proposed routes. To augment the conventional SUE geophysical technologies, T2ue implemented innovative SUE technologies to give greater certainty to the horizontal and vertical locations of the subsurface utility infrastructure. All utility alignments were surveyed and the information was extrapolated into a composite utility drawing that showed the existing utilities at the appropriate Quality Levels in accordance with ASCE 38-02, “Standard Guideline for the Collection and Depiction of Existing Subsurface Utility Data.” Test holes were conducted at critical locations using vacuum excavation equipment and allowed for precise x, y, z coordinates on key infrastructure.
RELATED: Trenchless After Hours: T2ue Extracurriculars Focus on Team Building
Each of the innovative SUE technologies that were implemented were chosen for specific reasons for locating and mapping the subsurface utility infrastructure. The following will describe the new technologies, why they were selected and their benefits to the SUE investigation.
Panoramo Manhole Scanner
Both projects contained hundreds of chambers (i.e. manholes). The equipment used to perform the chamber inspections on the two LRT Projects was the IBAK Panoramo SI 3D Optical Manhole Scanner. This equipment provided a 360-degree view of the manhole after the inspection. The 3D Optoscanner used two high-resolution cameras with wide-angle lenses, which enabled the scanning of the entire inside of a chamber in one single vertical run. This allowed for both condition assessment, as well as identification of chamber dimensions. The 3D point cloud deliverable will allow the end user to measure nearly any feature within the chamber. There were approximately 295 chambers inspected on one and 540 chambers on the second project.
Light Detection and Ranging (LIDAR)
The LIDAR technology optimizes light image objects. This technology acquires 3D Point Clouds from which realistic 3D models are produced. The data collected with the laser scanner was at survey grade when processed. This data was incorporated directly into the 3D CAD software. The advanced technique of laser scanning was used to survey critical chambers within the projects. This technique gave the project accurate information on the actual size and location of each chamber, which improved the utility coordination analysis of utility impacts on the projects.
Closed Circuit Television
CCTV technology has been around for several decades; therefore, it is not considered an innovation. However, in this case, it was not the actual technology that was innovative but rather the use of the CCTV with side launch camera technology that was the innovative approach. Prior to selecting the locations of the numerous boreholes that were required for the design of the LRT projects, T2ue first used CCTV to locate each sewer lateral then launched the CCTV side camera to map the location of the sewer laterals within the boulevard. After this critical sewer lateral information was identified, the non-conflicting borehole locations were then selected.
Stream Multi-Channel Ground Penetration Radar
MCGPR technology is a multi-sensor GPR array that allows for the collection of a large quantity of GPR data both simultaneously parallel and perpendicular to the direction of data collection. For the two LRT projects an IDS STREAM EM and C MCGPR were used. The STREAM EM uses 40 separate channels, with double polarized (VV and HH) antennas operating at dual 200 and 600 Mega Hertz (MHz) to cover wide surfaces in a single path. While attached to a vehicle, the STREAM EM can be towed along the road and can be used to pick up large quantities of data with little to no disruption to traffic. The data can then be post processed in the office and used to create 3D models of the subsurface infrastructure. The smaller MCGPR unit, a STREAM C, was used for the collection of GPR data in the boulevards. The use of this technology helped to provide additional information regarding not only just utilities, but also some additional hidden anomalies that would have been an unknown with conventional geophysical technologies. A unique feature of the STREAM EM and C is that a 3D model can be created from the output with minimal data processing.
3D Modeling
After compiling the SUE data, T2ue used a Bentley Power Geopak Subsurface Utility software product to generate the 3D models of the existing subsurface utilities for the two LRT projects. The 3D model used various textures and color transparencies on each of the utility alignments to depict the quality of the SUE data in accordance with ASCE 38-02. Some features of the 3D software, which are key to improved utility coordination on the two LRT projects, are a) its utility conflict detection feature, b) its compatibility with the “Microstation and InRoads” softwares utilized by the Technical Advisor Consultant, c) its ability to create 3D interactive PDFs of the model. Firstly, the “utility conflict detection feature” not only identifies intersecting conflicts but can also flag sub-minimum clearance (parallel) conflicts. This feature aids the utility coordinators in the performance of the utility conflict analysis. Secondly, the software’s “compatibility” with “Microstation and InRoads” was mandatory as these software programs were utilized on the two LRT projects. Thirdly, the 3D software has the ability to create interactive PDFs. This ability allows everyone associated with the project access to the 3D model without having the software installed on their digital devices. Not only staff in the office, but also staff in the field can have a 3D plan of the project that enhances their ability to perceive the utility impacts in the real 3D construction world.
Sample of 3D Model. Not only staff in the office, but also staff in the field can have a 3D plan of the project that enhances their ability to perceive the utility impacts in the real 3D construction world.
Utility Coordination
The 2D Composite Plans and 3D Composite Utility Model created from the SUE data for the projects were utilized by the project utility coordinators to create detailed conflict matrices. The matrices allowed the team to wisely select strategic test holes at critical locations to improve the accuracy of the subsurface utility infrastructure locations. Once all the test hole information was gathered utilizing a hydro vac methodology the composite utility plans/models were updated. Armed with accurate composite utility plans/models the utility coordinators performed utility impact analyses that resulted in updated, reliable utility conflict matrices. This utility impact analysis is an iterative process as the project design progresses through the Alternative Finance Project process. Having a utility information with greater accuracy was beneficial in the determination of the following:
- Utility relocation tasks required to be completed prior to the procurement of the successful proponent (Project Co.),
- Utility relocations tasks that could not be completed prior to the procurement of the Project Co. but are critical path tasks , and
- Utility relocations tasks that could not be completed prior to the procurement of the Project Co. but are not critical path tasks.
Conclusion
The management of utility relocations is one of the biggest risks on the projects. The creation of accurate subsurface utility drawings using a progressive SUE program following a creditable system of collecting and depicting subsurface utility data, such as ASCE 38-02, is fundamental in the proper management of the utility risk on these two projects. The use of innovative SUE technologies such as Panoramo manhole scanning, LIDAR, CCTV with side launch camera, MCGPR and 3D modeling, further enhanced the accuracy of the SUE data used to create SUE drawings and 3D models.
RELATED: Establishing Integrity in Subsurface Utility Engineering
Equipped with subsurface utility information acquired with the best SUE technologies, utility coordinators and the design team produced reliable utility documents for the projects’ contracts and will have a greater understanding of the true utility impacts on these large transit projects as they progress through the project phases.