The Advantages of Rock Drilling with Pneumatic Hammers
November 22, 2011
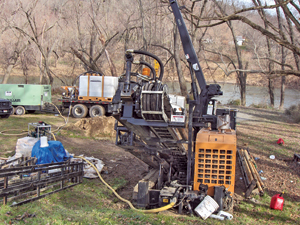
This method was highly beneficial for the contractor drilling the rock, because the first contractor had already spent valuable time, effort and resources on the bore — i.e. the potholing is finished, the depth where the contractor will encounter rock was already established and the initial pilot hole was bored — saving the rock subcontractor precious time and money.
A new trend in rock drilling that has grown in interest is a contractor that drills both dirt and rock on the same project. If rock is encountered, these contractors simply convert their drill into rock drill in the field while the drill is sitting on an attempted dirt bore that is now a designated rock bore. The preferred method of use in this situation is a DTH — a steerable down-the-hole (DTH) percussive hammer.
A DTH system can be adapted to most directional drills in a relatively short period of time. The benefits for a project in which the drill has been converted into a rock drill are numerous. For example, on some cross-country runs, the drilling location is usually off the unbeaten path where it can at times take a day just for the contractor to get the equipment to the site. The contractor can have more time invested in moving the equipment in and out of the jobsite than actually drilling. With DTH technology, once the contractor hits rock during the bore, it’s just a matter of connecting the compressor to the drill and putting on the steerable hammer.
Other benefits of DTH technology include that the system only requires a small amount of water — hundreds of gallons vs. thousands — if using a compressor, which in turn equals less mud to clean up and less time getting water. Also, there is less ground disturbance because the same drill will be doing the dirt and the rock, which in turn makes it more cost-effective for the subcontractor and the prime contractor. On a job where the dirt drill has been converted to a rock drill, the subcontractor does not waste days on a bore he cannot do, and the prime contractor doesn’t waste time and money lining up another drill to handle the rock portion of the bore.
Some other key benefits for running a percussive hammer are that anchors are not required to stabilize the drill, which helps greatly when starting a bore around existing utilities. It is highly recommended not to anchor the drill because this can be used as an indicator as to what type of hole the driller is actually making. If the drill is moving around while steering or rotating, and the rotational torque gauge on the drill is reading low torque, this would indicate that the driller is over thrusting the hammer, therefore not letting the hammer do its job. If the torque gauge is high, this would indicate that the driller is out-running the cuttings, not getting the cuttings out of the bore hole and would need to trip out to clean the hole. There is also less wear and tear on the drill while drilling rock because the drill is usually at low idle and the hammer is doing all the work.
Running a hammer requires a minimal amount of rotational torque, not like rotary drilling where high thrust and high torque are required to cut the rock. The benefit of the low torque is that the hammer tends to stay on course and drill a straight hole, which in turn means less time steering to keep the tool on course.
For the contractor wanting to be on the cutting edge in the rock drilling industry, this new technology is recommended. Below is a good example of a contractor that has used DTH technology.
Southeast Connections
Southeast Connections (SEC) specializes in rock drilling and has completed solid rock bores in excess of 1,300 ft and up to 32 in. in diameter in some of the hardest formations in the Southeast. SEC’s preferred method for all of its HDD installations in rock is by means of pneumatic hammers, because SEC believes that provide the best technology for rock drilling. SEC HDD superintendent Doug Simmons has used nearly every method to pilot and ream rock on the market today and believes that nothing else offers the advantages that pneumatic hammers do.
For SEC, as well as every other contractor, time is money on any project. The production rates that SEC experiences with pneumatic hammers vs. mechanically-driven or fluid-driven motors out produce by more than 2 to 1. Simmons says SEC has seen installation time drop to the point that allows SEC to be hard to top on project bids unless its competitors are using the same technology.
Another key advantage that pneumatic hammers offer SEC is the drastic reduction of drilling fluids used on a project. On some projects, SEC has completed pilot bores up to 1,000 ft with a mere 250 ft of fluid — just enough fluid to keep the transmitter cool is all that is needed. This offers a key environmental advantage for customers with more sensitive projects, Simmons says.
One of the most concerning issues for contractors on projects with rock is the increased wear and damage to down hole tooling, as well as the drill rig itself. Using hammers, SEC has found that with most of the work being performed down hole by the hammer, the rig and tooling becomes the means to just guide the hammer to the point of where it performs the work, Simmons says. While the aspects of tooling life are still primarily affected by bend radius and proper drilling fluids, any advantage and increased longevity is welcome.
While every method to cut rock has advantages and disadvantages, for SEC, it has found the most productive and cost-effective means that available to the industry today. In a way, Simmons says that pneumatic hammers are HDD’s best kept secret to date.
Cary Cooper is owner and president of Hardrock HDDP Inc., based in Winder, Ga.
Comments are closed here.