SPR Spiral-Wound Pipe in Stendal, Germany
August 24, 2011
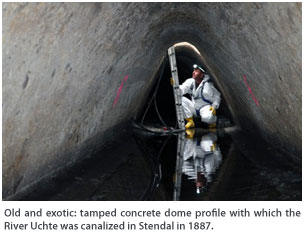
The latest rehabilitation of the “canalized Uchte” in Stendal by specialists from the Brehna office of KMG Pipe Technologies GmbH shows that even exotic profiles with large nominal diameters can be rehabilitated by this method.
Historic Structure in Stendal
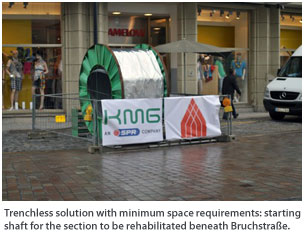
the River Uchte, which used to flow openly through Stendal town center, was “tamed” by canalizing the water course. For this purpose, a dome profile sewer with a crown height of 1.74 m and bottom width of 1.50 m was built in the present-day alignment of Bruchstraße. The sewer was constructed in tamped concrete on a brick foundation – a technology applied to many structures at that time. After 130 years of continuous use, however, these structures are fraught with the same problems: The integrity of the concrete is weakened, the walls are becoming porous and no longer watertight, their surface is disintegrating and they are becoming unstable.
Unusual Structural Design
Trenchless Was the Solution
A key consideration in opting for the trenchless rehabilitation method was the reliable restoration of the necessary stability of the old structure. After a careful technical analysis the authorities decided against short pipe relining and in favor of the SPR spiral-wound pipe lining method. This option was offered by the Brehna branch of KMG Pipe Technologies GmbH, a subsidiary of SEKISUI SPR, Schieder-Schwalenberg. The deciding factor in Stendal was that the spiral-wound pipe lining could be installed using the existing manholes – without the excavations usually needed for laying short pipes. Thanks to trenchless installation, the road resurfacing work was performed parallel to the sewer rehabilitation.
The Process
The SPR method is a cutting-edge version of spiral-wound pipe lining technology. The basic principle of SPR spiral-wound pipe rehabilitation is that the decayed sewer section is repaired using an endless PVC-U or HDPE profile strip (spiral-wound pipe).
The endless profile strip, wound on a drum, is fed into the sewer through an open manhole and joined by a spiral-winding machine installed in the sewer to form a pipe by a tongue and groove technique. Liners of practically any length can thus be created: As soon as one of the above-ground profile drums is empty, a new coil is joined onto it by the heated tool butt welding method. Apart from this short interruption, the SPR method permits continuous working.
Waterproofness and stability are, however, not the only structural benefits of the spiral-wound liner as a rehabilitation system. The spiral-winding process intentionally leaves a defined annular space between the SPR liner and the old pipe, into which a high-strength mortar is injected in a subsequent work stage. In addition, the annular space is walled off and cells filled at regular intervals. Ultimately, the SPR liner serves “only” as formwork for a new concrete inner shell of the old sewer and in the long-term it provides a reliable protective layer to shield the concrete structure from the effects of sewage and sewer atmosphere. Logically, the annular space is not minimized at the planning stage, but consciously defined according to static requirements. In the dimensioning of the SPR liner it is not a matter of “as little annular space as possible,” but “as much annular space as (statically) required.” Whether the resulting reduced cross-section is acceptable compared to the old pipe is a question of the hydraulic analysis necessary for each individual case in the course of planning. The extremely good friction coefficients of the new, smooth SPR liner have the positive effect that the reduction in diameter is already partially compensated for.
Intakes Open during Winding
Second Generation Material
Interest in the procedure is considerable. At an open viewing of the construction site in Stendal’s Bruchstraße from May 17-19, 2011, sewage experts from authorities and water boards including Kiel, Magdeburg and Erfurt were able to inform themselves of the possible uses of the SPR method in difficult situations. Among them were employees of the Berlin water utilities responsible for sewer rehabilitation. All of them took a critical look at the spiral-wound dome profile liner below ground. Meanwhile the construction site belongs to the KMG rehabilitation experts alone. They are confident that the contract will be completed on time by mid-July 2011.
This article was submitted by SEKISUI SPR Europe and KMG Pipe Technologies GmbH.