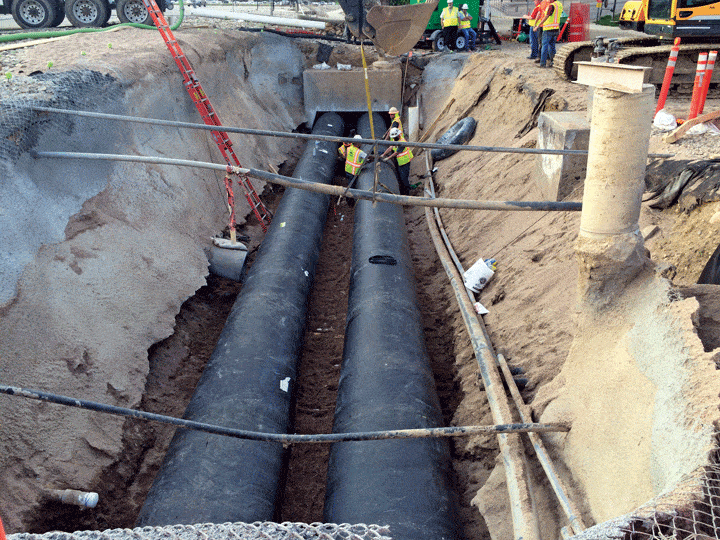
Sliplining Used to Rehab Collapsed Pair of CMP Pipes
October 21, 2015
In mid-May 2015, a large corporation in the Boulder, Colo., area experienced a serious situation on its property when a pair of 48-in. elliptical corrugated metal pipes (CMP) collapsed in the immediate vicinity of many critical utilities.
The pipes were located at the very end of the stormwater system that handles all of the stormwater for the west side of the property. The pipes were connected to an existing concrete collection vault then ran 120 ft with the last 40 ft under an access road before discharging to an open stormwater ditch.
When the pipe collapsed, it interrupted site stormwater drainage during an unusually wet Colorado spring creating severe flooding on the property. Without a quick repair, the company was looking at significant ongoing costs for temporary measures and the possibility of severe damage to underground infrastructure systems. The company asked Fluor, one of the world’s largest engineering and project management companies, to find a solution to the emergent situation.
“Part of the problem was that a section of the pipe itself ran under an existing access road that had critical utilities running through it. The prospect of digging up and replacing that section of the culvert was costly. So, we started looking for options to sleeve the pipe, but found limited solutions for oval pipe,” explained Fluor project coordinator Jim Smith.
The pipes were connected to an existing concrete collection vault then ran 120 ft with the last 40 ft under an access road before discharging to an open stormwater ditch.
The project team looked at the possible solutions to the complicated problem and decided to go with Snap-Tite, an intelligent, cost-effective rehabilitation system. It uses lightweight, flexible and durable high-density polyethylene (HDPE) pipe to rehabilitate, and often outperform, corrugated metal. Fluor found that HDPE has tremendous advantages over concrete and corrugate metal replacement or repair. The Snap-Tite system segments could be “snapped” together, creating a water-tight seal at all joints.
Another concern with lining the pipe was a reduction in flow rate through the pipes. “We found that by sliplining the culverts with Snap-Tite, we actually increased the flow rate,” Smith said. The system’s joints are machined on the end of PE 3408 high density polyethylene pipe. The result is a water-tight joint whose inside and outside diameters are the same as those of the pipe.
Each of the pipes run approximately 120 ft through the affected area. Fluor was forced to excavate an area 80 ft long and 20 ft deep to remove the unsalvageable corrugated metal pipe and the remaining 40 ft of pipe stayed under the access road. Removing the remaining 40 ft of CMP under the access road was not an option. The drainage water needed to be continuously pumped away from the site of the damage and the underground utilities. That process was costing the company upward of $20,000 per day. This collapse needed to be fixed and fixed quickly.
“Once Snap-Tite received the order, they quickly processed the pipe in their Kingman, Arizona plant and delivered it to the site in Colorado,” said Russ Wosk, Snap-Tite’s regional manager. Fluor then tasked one of their contractors, Trautman and Shreve to install the new Snap-Tite pipe.
Because the existing corrugated metal pipe was elliptical shaped, Snap-Tite provided oval pipe to slide into the existing pipe under the access road. Snap-Tite then created a custom length of pipe that was ovaled only halfway. The remaining length was left the standard round and continued through the open-cut section. All of this work was done fairly quickly using a standard track hoe. Concrete contractor Thorcon tied the pipeline into the concrete vault with a poured concrete collar. Thorcon also completed the grouting process for the liner inserted under the access road. They mixed concrete and water to create a very flowable mix which they then pumped into the annular space between the existing CMP and the new Snap-Tite liner pipe.
“This process is used to not only fill and seal that annular space, but it also fills all the holes and voids that exist in and behind the existing CMP. It is these holes and voids that have played a major part in the failure and collapse of the existing pipe,” explained Wosk.
It was also very important make sure all the stormwater coming from the drain in the adjacent parking lot was directed into the new HDPE pipeline. “Because the large area in between the driveway and the vault had been excavated, the drain pipe from the parking lot was also exposed,” Wosk said. “They needed to be able to tie in this 24-in. concrete pipe to the new Snap-Tite HDPE pipe.”
The process was relatively simple. The contractor cut a hole in the side of the Snap-Tite at the location of the incoming concrete pipe. He then took a small length of solid wall HDPE pipe with a slightly larger ID than the OD of the concrete pipe and slid it on the concrete pipe. He then matched the new piece of HDPE up to the hole on the Snap-Tite and used a process called Extrusion Welding to permanently attach it. This allowed all the drainage from the parking lot to now be captured and flow out to the storm water ditch.
The entire event from the collapse to the time the pipe was rehabilitated and buried took a little under six weeks. Snap-Tite was able to provide onsite support throughout the entire process. “It was extremely positive and working with Fluor was terrific,” Wosk noted.
Chelsea Rabideau is public relations coordinator at ISCO.