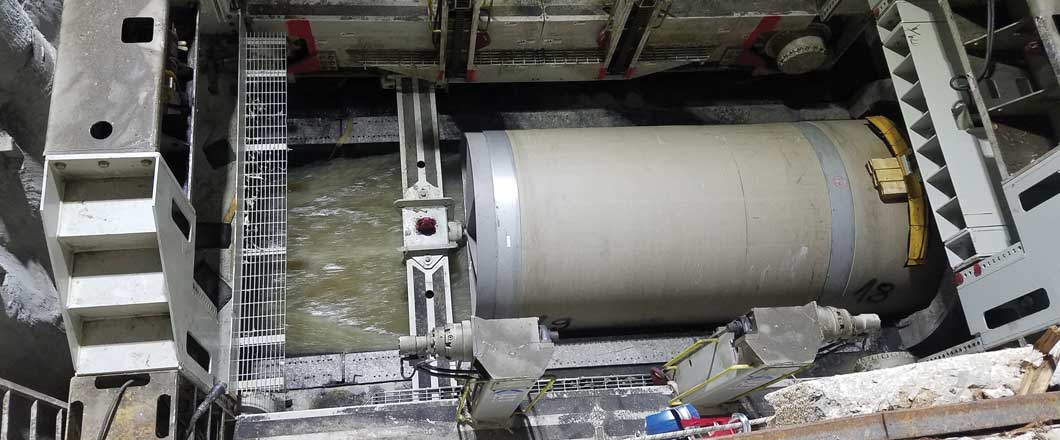
Sliplining the Q Line South in Israel
The Igudan Q Line South project in the Mediterranean Sea coastal town Bat Yam is the first and largest Israeli wastewater project of its kind. The project is competently executed using the first Akkerman sliplining system to land on international soils.
In recent years, central Israel, referred to as the Dan Region, has experienced a revitalization causing rapid population growth, and capacity concerns for its 40-year-old wastewater infrastructure. The region’s wastewater pipelines and treatment facilities are owned and managed by the Dan Regional Association for Environmental Infrastructure (Igudan).
Igudan’s inspections of the Q Line revealed signs of significant deterioration and the potential for a service failure in recent years. They considered several technologies for the restoration before landing on sliplining as the preferred method.
Sliplining is the pipe rehabilitation method of inserting a new liner pipe inside a failing pipeline to prolong its lifespan. The restoration improves the host pipe’s structural integrity and has the potential for long installation lengths at a rapid production rate. Slip line renewal possesses all the inherent benefits of trenchless pipe installations – reduced number of access shafts, minimized surface disruption, with a cost-effective price tag.
E.R. Itshaky, founded by Ezra Itshaky in the 1960s, served Tel Aviv and the surrounding area with civil engineering services for 40 years before Ezra’s son Yaki entered the business in 2002. Under Yaki’s leadership, the company expanded its service portfolio to include heavy civil water and wastewater infrastructure construction services. Today they are known as E.R. Itshaky-Microtunneling Israel.
RELATED: Sliplining in Edmonton – EPCOR Project Rehabilitates Groat Road Sewer
Project Challenges
Being an innovator in a specialized field comes with much responsibility for choosing the most suitable approach to the project. “Central Bat Yam is a very populated area, so the traditional way of digging for pipe installation was not feasible on this project,” Itshaky explains. “Moreover, due to a dense existing underground infrastructure, we could not consider adding new line by pipe jacking, so the only way was to use the existing line and implement it with the sliplining method,” he furthers.
Itshaky states, “The 10-ft (3-m) length and 78-in. (2,000-mm) diameter of each section required equipment suitable for high jacking forces and execution under streaming sewage. The uniquely designed Akkerman SLS100 sliplining system complies with these two main parameters.”
The Sliplining Solution
The Akkerman SLS100 system performs pipe installation in live sewers without service disruptions and bypass pumping. It’s an all-in-one pipe jacking system for rehabilitating live sewers that can accommodate up to 102-in. OD pipes using spacers and frame extensions. The equipment package includes a modular sliplining frame, a power pack for powering the modular frame’s hydraulic motors and auxiliary functions, and a pipe-specific thrust ring, all controlled by an operator using a wireless remote controller.
RELATED: Sliplining in Urban Areas
The system facilitates controlled pipe lowering into the access shaft using hydraulically linked pipe elevators. A drawbar-mounted thrust ring meets and engages with the pipe for axial advancement into the host pipe. The system’s retention winch and gripping pipe system assist in counterbalancing live flow force and neutralizing the flow buoyancy to keep the pipe string compressed during installation.
All operator functions are controlled through the LCD screen wireless remote controller, including main drive speed, bidirectional travel, pipe elevators, pipe clamps, drawbar, winch, and Estop functions. The display shows jacking tonnage and load sense pressure. Remote live data logging transmits through a modem in the power pack available via VPN and customized web dashboard.
Rimon Ofek-Atrim purchased the Akkerman sliplining system to tackle the Q Line South project and as an equipment solution for anticipated future projects. E.R. Itshaky Ltd, with its skilled team and vast experience in similar works, was nominated as the expert to perform the work.
Construction/Outcome
The Q Line South project required sliplining with three diameters of GRP pipe, 70 to 78-in. ID (1,800 to 2,000-mm) in several lengths up to 10-ft (3-m). With a 4,970-ft (1,515-m) total installation length, about 60 percent of the work would be performed in live flow. Itshaky reports that the Q Line South is the first of its kind in Israel and calls it the largest sewer line installation while still underflow.
“The live flow slip line work could only be executed in a limited time window when the sewage stream level is under 50 percent of the pipe diameter,” he says. They were restricted to two-hour construction intervals in the wee hours of the morning, with a one-hour break to alleviate pent-up flow from a valve-controlled reservoir. When flow returned to a more manageable volume, slip line construction proceeded for another two hours.
RELATED: REHAB WINNER – Sewer Rehabbed Using Design-Build & Sliplining
Limited open space along the Q Line meant the potential for ideal locations for the two access shafts had to be minimally invasive.
Directly under a park, positioned between apartment complexes was an optimal area to access the infrastructure with minimal disturbance to area residents. The first access shaft was 1-ft (5.4-m) wide by 32-ft (9.7-m) long to accommodate the SLS100 modular frame on its floor at 24 ft (7.3 m) deep.
The first wet run, 492-ft (150-m) in length was initiated from the park access shaft against the wastewater flow. Before sliplining began, the crew ran a prover through the existing pipeline to clear debris and cut the top half of the concrete pipe in the access shaft. Crew inserted the first pipe GRP segment into the host pipe on March 8, 2022.
Akkerman field technicians traveled to provide equipment operation training for the first section. Even with the learning curve, the crew achieved a six pipe per hour production rate and completed this first run in six, five-hour shifts.
After mobilizing the equipment to the second access shaft, Itshaky crew set up for the second slip line. Also in live flow, this section would rehabilitate a 1,980 ft (600 m) of the Q Line. The section was completed in mid-April in a week’s time. They experienced production rates as high as 45, 8-ft (2.5-m) pipe per shift.
The last and longest section for replacement, 2,510 ft (765 m) culminates with a 492-ft (150-m) curved section and emerges inside a deep, multi-level shaft that adjoins several other utilities. Curved sliplining alignments are possible by utilizing short pipe segments to form the curvature and positioning the access shaft at the end of the curve.
“Due to the Israeli regulation to protect underground water pipes which are adjacent to sewage, the last section is being performed in two stages in a dry environment. The first stage was pipe jacking as a protection layer and the host pipe, and the second was sliplining into the new jacking pipe,” Itshaky describes.
As of August 2022, all live flow sections were complete following the original project timeline. E.R. Itshaky crews are achieving an installation rate of up to 400-ft. (120m) per shift.
The Q Line runs 2.85-mile (4.6-km) in its entirety, and the contractor anticipates the opportunity to renew by sliplining another section equivalent in length to the Q Line South project.
“Sliplining with the Akkerman SLS100 system technology helped us to complete this challenging project efficiently and effectively. E.R. Itshaky is proud to have successfully introduced this new technology to Israel for the benefit of Igudan, and further trenchless options in the urban area,” Itshaky concludes.
Laura Anderson is the internal communication director of trenchless equipment manufacturer Akkerman.
Photos courtesy CKL Photography