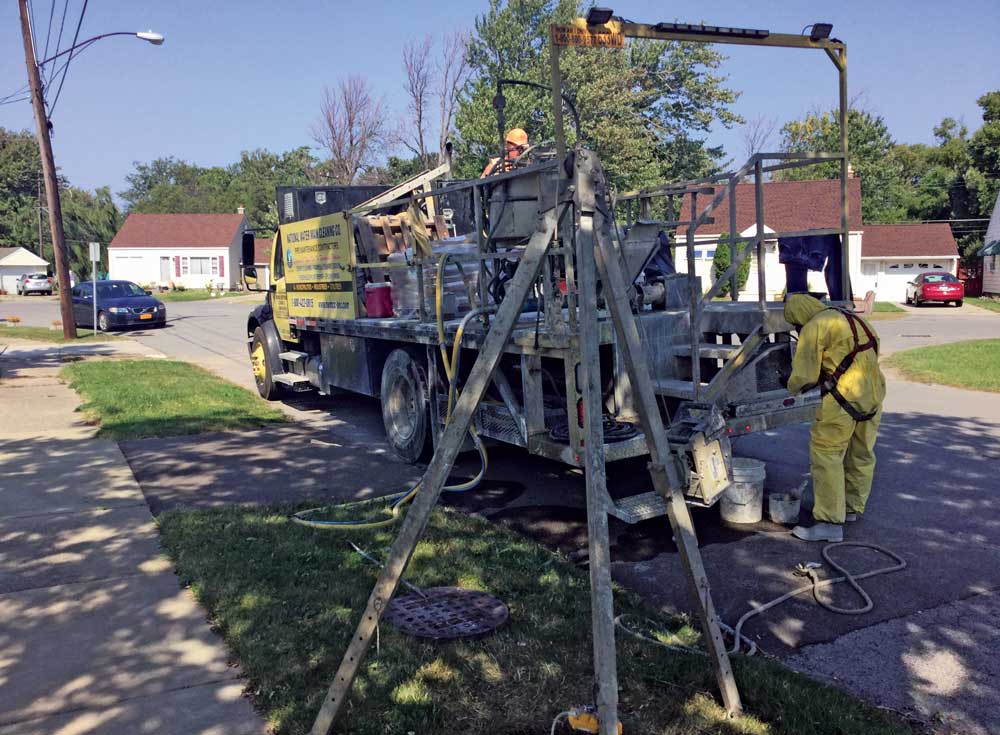
Manhole Rehabilitation Overview: Considering and Choosing Your Options
Many manholes were constructed primarily from brick or other masonry materials for both stormwater and sewer applications in the 1800s, but construction has continued using these methods unfortunately as recently as the late 1990s as well.
Brick manholes have a considerable risk of losing grout, thus providing an opportunity for infiltration or the bricks collapsing. Similarly, concrete manholes bring a risk of failing prematurely due to microbial-induced corrosion (MIC) from sewer gasses, specifically H2S.
RELATED: Vista, California Turns to High Strength Fiber-Reinforced Polymer Concrete to Rehab Culvert
Rehabilitating a manhole requires carefully considered decision-making because of the variety of options available in the industry right now. Before even choosing a rehabilitation product, however, the structure needs a proper condition assessment. NASSCO has developed a Manhole Assessment Certification Program (MACP) as the North American Standard for manhole defect identification and assessment.
An inspector meeting all OSHA safety standards, including Confined Space Entry (CSE), should, at the minimum, inspect the manhole according to MACP, but inspection methods can also include a camera, CCTV video or light detection and ranging (LiDAR) assessment. These methods can give companies or municipalities an accurate assessment of the condition of the manhole, which will lead to an easier decision of how it should be repaired.
Complete manhole replacement is a viable option for a manhole that is beyond repair. Replacements can be done by digging out the existing manhole and replacing it with a precast concrete structure or an HDPE insert.
For a manhole that can be repaired, there are typically three rehabilitation options: cured-in-place pipe (CIPP), spray- or hand-applied polymer linings or cementitious mortar linings.
To use a CIPP liner, there needs to be a hole that is large enough for the system to fit into; sometimes the chimney of the manhole must be removed to gain exposure to the largest diameter of the pipe.
Additionally, there needs to be a seal at the bottom of the manhole to ensure that there is no material getting between the CIPP liner and existing manhole as the joint between the two is made. A CIPP repair crew will take up more space and use more equipment than alternative methods and the ideal diameter for this type of repair would be larger than 36 inches, which will require an over-the-hole wet out and require more of an ecological footprint to complete the job. The restrictions of this repair method make it a viable, but not extremely common, option for manhole rehabilitation.
Spray- or hand-applied polymer linings include epoxies, polyurethanes or polyureas. An advantage of polymer linings—as well as CIPP liners—is that they are very chemically resistant if the liner stays fully intact. For the liner to stay fully intact, the system must dry perfectly, so there can be absolutely no water present on the interior structure of the system (the manhole itself). If the manhole needing repair has significant corrosion, there will be a need to build back the original shape of the manhole with a cementitious mortar. This additional work will produce a setback of several days as the cement cures to ensure that enough strength is built to support the repair, as cement needs moisture to cure.
Getting these polymer linings to perfectly dry is incredibly difficult. These systems are required to be spark tested to ensure that no pinholes exist within the liner. If a pinhole does exist, then the electrical rod used for the test will ground and produce a spark, which means that this liner is at risk of failing and not remaining as chemically resistant as intended and will require repair of the lining before being put into service.
After testing geopolymer mortar system GeoSpray, which did not crack, the town decided to specify the mortar on future manhole projects.
Though the inspection and installation methods can be difficult, if the installation goes as planned, then CIPP liners and polymer linings are an excellent, though more expensive, choice.
Cementitious mortar linings can be broken down into three categories: portland cement (OPC), calcium aluminates (CAC) and geopolymers. These linings can be installed quickly, and though they require stopping infiltration and cleaning the manhole, they do not require the structure to be completely dry. A surface-saturated moisture condition is preferred. OPC has a poorer resistance to MIC, while CAC and geopolymers have a high resistance. The key benefits for cementitious liners are that they are much easier to apply, lower in cost and have adequate chemical resistance in most situations. When looking at all available options for rehabilitation, an advanced cementitious mortar lining or spray-applied polymer lining, which excludes OPC, would be better choices. If polymer liners are installed properly, then they have excellent chemical resistance, but the cost is higher and the installation process is difficult. The best decision will depend on the condition of the manhole, the ability to dry the manhole and the total cost of the project.
RELATED: Short Project, Big Benefits
Case Study
The town of Cheektowaga had to consider its rehabilitation options for a series of manholes in extremely dry conditions. It chose an assortment of products and found that OPC and CAC were prematurely cracking only hours after installing the lining. After testing a geopolymer mortar system, GeoSpray, which did not crack, the town decided to specify the mortar on future manhole projects. A Milliken Infrastructure Solutions (MIS) representative reached out to the township’s design engineer to suggest the geopolymer mortar system, which is less sensitive to cracking in dry manhole conditions with about double the compressive strength and triple the flexural strength compared to OPC. The added strength and resistance to sulfuric acid corrosion that is often found in sanitary sewer systems gives the mortar a superior life cycle.
A pilot study was conducted using a truckload of geopolymer mortar to line about 700 vertical lf with technical assistance provided. The installation contractor, National Water Main Cleaning Company (NWMCC), power-washed the manhole, mixed the mortar and pumped it down into the hole to apply it with a handheld spray nozzle.
“GeoSpray geopolymer mortar has a noticeable product consistency and quality that my crew and I appreciated during the project,” said Dennis Sullivan, Vice President and General Manager of NWMCC.
The mortar went on quickly and easily and did not crack. The township was pleased with the pilot application and decided to continue specifying GeoSpray mortar on a 5000 vertical foot manhole project, which is currently undergoing installation.
“This product’s unique, user-friendly application characteristics lead to efficiency in the field,” said Sullivan. “These characteristics make it a preferred product on certain future projects.”