Sewer Nozzles — the Business End of Jetting
August 20, 2014
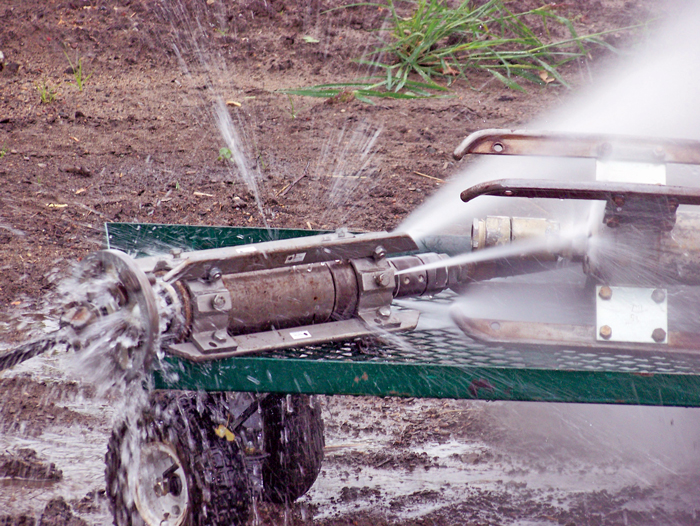
But it’s important to review jetting regimens periodically and carefully consider how they can be improved. Effective jetting not only saves money and time, it’s also a great way to avoid expensive flooding and overflow events.
In this article, I’ll be focusing on sewer nozzles — the business end of jetting.
We can divide all the available sewer nozzles into five basic types:
1) Basic Drilled Nozzles
2) Rotational or Spinning Nozzles (which can rotate fast or slow)
3) Bottom or Floor Cleaners
4) Specialty Nozzles (e.g., nozzles that function as rotary saws)
5) High Performance Nozzles (considered as a separate class due to advanced engineering and better performance—all of the above classes can be ‘high performance’)
I’ve been deeply involved in the sewer nozzle business for decades, so perhaps I should be up front about a significant bias I’ve developed — better engineered and higher performing nozzles are always worth the initially higher investment. They clean sewers better and faster, they get more out of your truly large investment in a jetter, and they reduce jetter wear so that jetting equipment lasts longer and breaks down less often. And that’s not just my opinion. The NASSCO Jetter Code of Practices clearly states that in most cases, Tier 3 (the top tier) nozzles are the best choice in terms of ROI, durability and performance.
Why Top Tier Nozzles?
The very people who developed the first jetting units (about 1950) also designed basic nozzles. Put simply, they were more concerned about the actual jetter than the nozzles, and the design they came up with — drilled jet orifices (simple straight-walled tubes) pointing backward at angles of about 25 degrees to the Jetstream — are still the standard.
But ironically, this basic design is a very inefficient way to make use of the powerful (and expensive) forces generated by jetters. Much later, hydraulic engineers applied the principles of fluid mechanics to create nozzles that preserved laminar flows from the jetter all the way to the final jet stream, so that the final stream of water was tighter, faster, and more powerful, while requiring lower psi from the jetter.
This makes a big difference. Consider the simple example of a stream or creek. If the stream is running quickly through a narrow passage, the rapidly flowing water will carry along fine silt and debris and leave a clean bottom. But if water is moving slowly through a wider passage, silt will be deposited and build up in the streambed. Likewise, jet streams that are tighter and moving faster will clean out sewers more effectively.
Similarly, rotational, bottom cleaning and specialty nozzles work a lot better simply due to better manufacturing and designs that incorporate well known principles of mechanical engineering and fluid dynamics — so called ‘conventional’ nozzles are still in use simply because they’ve been around for a long time. But really, there is no situation where they work more efficiently. The only remaining advantage of conventional drilled nozzles is a lower initial investment. In other words, they’re cheaper to buy. However, that advantage disappears completely when the economic advantages of better and faster sewer cleaning and less wear on jetting equipment are considered.
Much of improved nozzle performance comes down to better orifice design. And the number of orifices is also important, as is smoothness of interior nozzle surfaces, directional transitions and several more factors.
But operators can also make decisions, in the field, that improve jetting and nozzle performance. Let’s take a look at the importance of pressure when jetting at the nozzle end, not at the truck.
Perhaps counterintuitively, more pressure from the jetter does not equate to a more concentrated or more effective jet stream. In fact, when water passes through the hose at lower pressures and speeds, it’s more likely to stay ‘gathered’— that is, smooth laminar flows are more likely to be preserved all the way to the nozzle. At high speeds, water leaving the jetter is likely to expand and create turbulent flows as it progresses through the hose. And turbulence reduces jet stream effectiveness. So that’s one solid reason not to automatically use maximum jetting pressures — they’re ineffective.
A complicating factor is the drop in pressure from the jetter to the nozzle. Using charts and a basic formula, it’s fairly simple to calculate nozzle end pressure based on hose diameter, hose length, and starting pressure. Alternately, you can simply measure psi at the nozzle end, something our reps do routinely for customers, in the field with the actual equipment used. Knowing the relationship between jetter and nozzle-end pressure is important, because psi at the nozzle end is really the most important variable in your whole sewer cleaning set up.
Our field tests of actual nozzles, and our design research, suggest that nozzle end pressures should never exceed 900 psi — when pressure is higher, turbulent flows are created that decrease nozzle efficiency, slow down sewer cleaning (and require more passes) and cause pointless excess wear on jetters.
Of course, making good use of optimum pressures still requires well-designed sewer nozzles.
What Is a Well-Designed Sewer Nozzle?
NASSCO defines Tier 3 nozzles as having ‘good design’ that is up to 97 percent efficient.’ ‘Good design,’ in this case, means that the inside design of Tier 3 nozzles preserves smooth water flows from the hose to the sewer surface, while redirecting those flows at optimum angles for the particular cleaning task at hand. And ‘97 percent efficient’ means that nearly all of the concentrated pressure of the jetter is transferred to sewer cleaning. Practically speaking, good design means carefully engineered orifice profiles (not simple drilled holes), properly sized orifices and the right number of orifices. For example, larger orifices are usually better, if a smooth powerful flow has been preserved — the greater volume of water is more effective at carrying away debris.
NASSCO also suggests that replaceable orifices and durability are important features of Tier 3 nozzles — replaceable orifices (or orifice inserts) can extend the service life of your sewer nozzle almost indefinitely.
By contrast, the chief characteristic of Tier 1 and Tier 2 nozzles is ‘poor hydraulic design,’ lower efficiencies and shorter service life. And because they are less effective cleaners, lower tier nozzles will require more passes and more time (and labor) to clean sewers.
A final point is that using lower pressures means lower GPM, and thus less water is needed to clean sewers; this can greatly reduce the amount of time filling the water, or even help you avoid the expense of a separate water truck.
Ask!
When adding to your nozzle collection, be sure to prepare and ask a lot of questions. You should:
• Know the details of your system, including the nozzle end pressures you typically achieve.
• Have a specific sewer cleaning task in mind; clearing out fats, oil, and grease (FOG) is a lot different than cleaning fine roots, and your jetting crew should have the right nozzles available for conditions prevalent in your system.
• Ask for an onsite demo when considering Tier 3 nozzles.
• Ask about optimum hose end pressures for the nozzle you’re considering—if the manufacturer doesn’t know, that’s a problem.
Compared to the amount of your investment in jetters and other big-ticket items, sewer nozzles can seem like a minor detail and maybe a good place to save some money. But thoughtful investment in the ‘business end’ of your jetter arrangement can optimize every step of sewer cleaning, and give you cleaner sewers, faster, while using less labor and reducing wear on equipment.
Scott Paquet is president of NozzTeq Inc., Tier 3 sewer nozzle specialists.