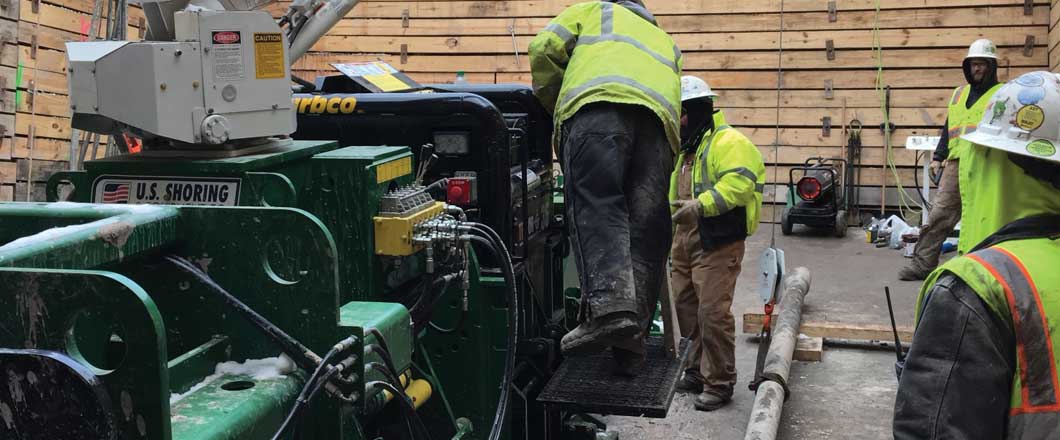
Product Profile – Barbco’s TriBor System
Horizontal directional drilling (HDD) is one of the most efficient, and accurate forms of drilling that contractors use today. But there are opportunities when this method can be combined with other boring technologies to provide a more efficient and cost-effective solution to an installation.
Barbco Inc. has been a longtime manufacturer of HDD drills but has also developed a different type of machine that does what is described above with its one-of-a-kind TriBor machine.
What Is the TriBor
As it name implies, the TriBor is a hybrid of three types of machinery: an auger boring machine (ABM), a guided boring machine (GBM) and a horizontal directional drill. Combined into one machine, it provides cost-savings, efficiency and versatility not seen in other boring machines.
Case in point is a project that called for the use of TriBor technology by contractor RJ Underground out of Kenosha, Wisconsin. The team from RJ Underground was tasked with installing return lines underneath a highway for a heating and cooling system. The system was being installed at Wisconsin’s Children’s Hospital, with a two-month deadline ending in December. With three unsuccessful attempts at this job from other contractors, the stakes were extremely high.
The job encompassed two, 1,000-ft long, side-by-side bores that were approximately 15 ft apart. Shoring boxes, slide rail and scaffolding were used to construct the 32-ft deep trench.
The crew began the job by drilling out with its 160,000-lb directional drill and continued pre-reaming up to 27 in. Heavy-duty 20-ft maxi rod sections were used.
After the desired size was reached, the crew from RJ Underground switched over to the TriBor 36 drill, which was sitting on 30 ft of custom-made track. The crew began to complete the next two ream passes utilizing the TriBor, beginning with the 32-in.pass.
Throughout this tedious process, the TriBor drill was connected to a massive reclaiming system that kept the mud extremely clean; it began with a pre-screen out of the pit, which accounted for a lot of the heavy clays. After it moved from one reclaimer to the next, it was then blasted down hole by a 500-gallon-per-minute pump.
After successfully reaming up to 32 in., the crew began using the last pass reamer, which was 42 in. This reamer was directly followed by the product pipe, a 32-in. high-density polyethylene (HDPE) line. This is a heavy duty, flexible, plastic pipe that has a high level of impermeability, making it suitable for high-pressure pipelines such as this one. In this case, the pipe was all fused together before they began to pull with the TriBor 36 drill.
Once the crew pulled one line, the TriBor was lifted up and moved over to complete the next pull.
When working on a job like this, contractors need reliability and efficiency. With temperatures dropping well below freezing, any halt in production can be devastating to the job. That being said, the TriBor drill was a key factor in the success of the RJ Underground crew on this project.
John Barbera is the marketing manager at Barbco.