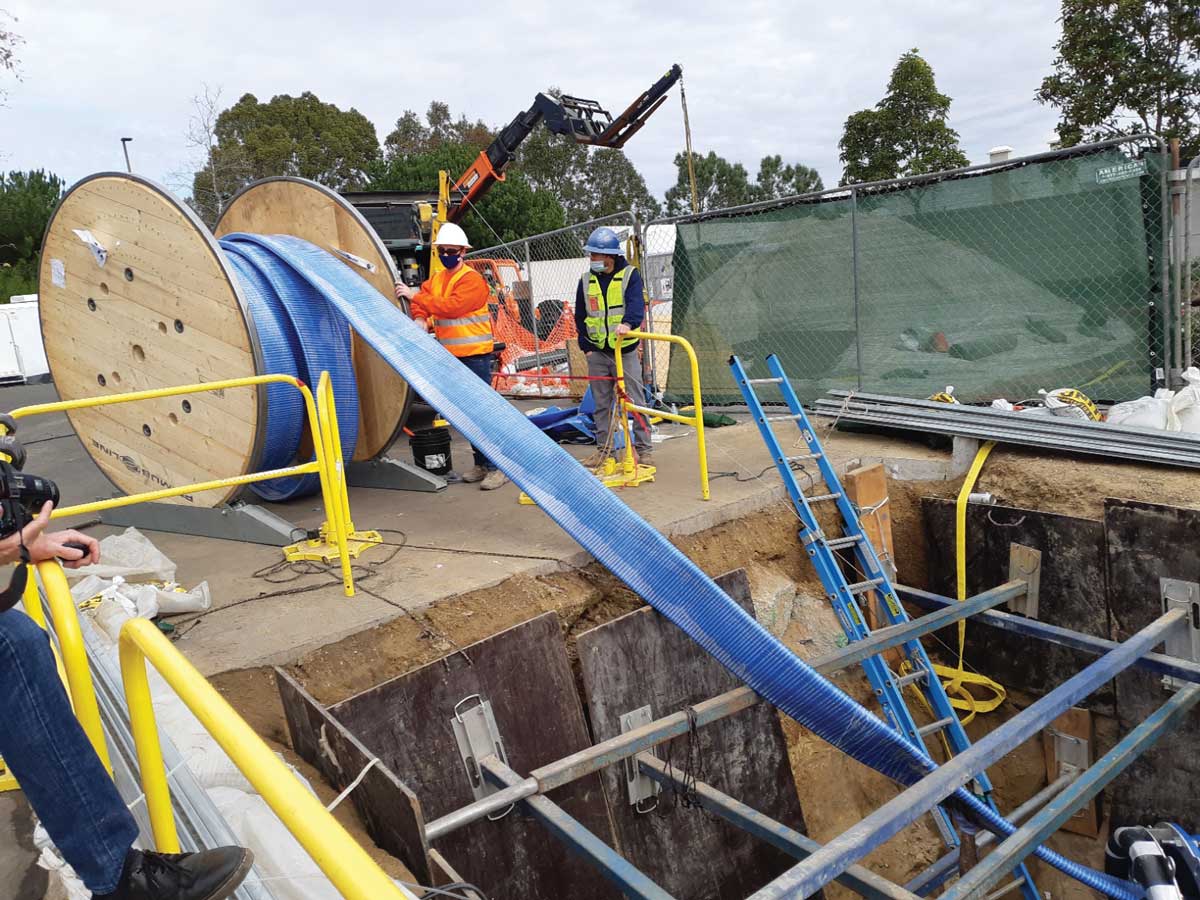
Primus Line Marks 10 Years in North America, Sees Immense Potential for Growth
The story of the growth of the trenchless industry is that of problem solving through innovation. And the story of Rädlinger primus line GmbH is no different.
For more than 20 years, the company has marketed and sold its proprietary flexible fabric reinforced pipe (FFRP) rehabilitation solution across the globe. Company leaders see the pressure pipe market as being immense, especially in North America, where Primus Line is marketed in the United States by Raedlinger Primus Line Inc. and in Canada by Raedlinger Primus Line CA Inc.
“Honestly, for us, it’s been growing exponentially,” says John Moody, director of sales for the United States and Canada. “With these pipes in the ground that are over 50 years old and have reached their maximum lifespan, you simply can’t ignore them anymore. They’re all ticking time bombs. They have got to be addressed and you’ve got to find a financially feasible way to do that.”
That’s where the Primus Line rehab products come into play. While not a silver bullet, as Moody notes, the products help minimize the social and environmental impact of projects whether it be sewer, water or oil and gas.
“The timing for us was kind of perfect coming to the United States and Canada,” he says. “We’re not out to just put the product in everywhere we can. That’s not the goal of Primus Line. The goal of Primus Line is to, obviously, be a competitive product, but also to help solve the issues that are in front of the engineers and system owners today relative to pressure pipes.”
To better understand the product, and how it came to be, it’s important to look at the company’s roots and how the company entered into the world of trenchless technology, becoming a leader in the rehabilitation of pressure pipes — how Primus Line sees the future of this growing market sector.
Where it Began
Rädlinger primus line GmbH and its international subsidiaries can be traced to Josef Rädlinger Sr. purchasing a manufacturing company that made looms to manufacture fabric hoses in the late 1980s. The purchase was made to complement work being done by his construction company in Germany.
According to company history, the loom manufacturing business in Cham in the Upper Palatinate in Bavaria in Germany — where Primus Line is manufactured to this day — was a byproduct of an acquisition made by Rädlinger to complement its own construction business with the manufacture of excavator attachments. This company became Rädlinger Maschinen- und Anlagenbau GmbH (now Rädlinger Maschinen- und Stahlbau GmbH). However, the company continued to produce and perfect looms for fabric hoses at the time. The looms were so good that it was possible to weave aramid fibers — a difficulty with looms that Rädlinger solved. The company also produced gas pressure regulating systems, which brought it into contact with companies in the gas industry and discovered the potential for high-quality hoses.
That started a process of working with a gas company to develop pressure pipe rehabilitation technology for gas systems that allowed them to navigate bends and turns and complete long pulls with minimal excavations.
Moody notes that system owners across Europe, and in Germany in particular, were keen on using minimally invasive technologies to repair their underground infrastructure because there are still WWII-era ordinances left in the ground.
“They really had the need for this technology to be developed but it didn’t exist. The gas company [Verbundnetz Gas] and Rädlinger came together, developed an R&D team and they co-produced this liner, Moody says. “They were the first client and customer for [what would become] Primus Line. Very quickly the company realized the implications of it for different adaptations for the water and sewer rehab market. They started testing these different things out with pilot projects for different municipalities in Germany, and it all went very, very well.”
After several years of fine tuning the product and completing rigorous pilot testing, in 2001, Rädlinger formed Rädlinger primus line GmbH to market this new FFRP rehabilitation solution across Europe.
After successes on their home turf, Rädlinger looked westward with the establishment of Raedlinger Primus Line Inc. in North Carolina in 2013 and Raedlinger Primus Line CA Inc. in Canada in 2018. International growth includes the founding of Raedlinger Primus Line Pty Ltd. in Australia in 2016 and Primus Line (China) Ltd. in 2019.
Today, Rädlinger primus line GmbH and its subsidiaries are still owned by the Rädlinger family and belong to Josef’s son, Werner.
Moody notes that the company’s leadership knew to grow the company it would have to move outside of Europe — and North America proved to be an ideal place to start. Not only was the United States one of the largest economic markets in terms of its aging infrastructure, but system owners were also looking for alternatives to cured-in-place pipe (CIPP) for burgeoning pressure pipe rehabilitation market.
“An external market study supported this assessment. Among other things, it determined the rehabilitation needs, which dimensions Rädlinger Primus Line could cover with its portfolio and which rehabilitation methods were known in the United States at the time,” says Moody. “Trenchless methods already existed. Their use in the rehabilitation of pressure pipelines, however, was just emerging.”
Anyone who has worked in North America knows that new products and technologies are not easily embraced, especially by risk-adverse municipalities. And that reluctance increases if the new product isn’t from North America.
Such was the case in 2013 when Rädlinger set up Raedlinger Primus Line Inc. in North Carolina. The company realized that growing Primus Line in North America would require a homegrown salesforce with regional expertise to educate the market and gain acceptance for the product. To help hasten its acceptance, the parent company applied for and received NSF 61 approval for the liner in water applications.
Its first orders came in 2014 and it also marked the completion of the company’s first notable project: the rehabilitation of approximately three miles of 70-year-old grey cast iron water pipes with different diameters on a military base in Mechanicsburg, Pennsylvania. That same year, Primus Line began to increase its visibility by attending trade fairs and conferences across North America.
At the end of 2015, realizing it needed to bolster its efforts, Primus Line brought Moody on board who manages the North America region as the director of sales today.
“The original challenge was the early adopters of the product. Nobody wants to be the first to try an unknown technology in their system. Getting small pilot projects was the first challenge,” says Moody. “The second challenge was to find installers that were a good match for the technology and really understood the applications and the process the Germans had spent years developing for internal acceptance and project approval.”
Moody acknowledges that some installers didn’t want to follow the specifications of the Primus Line engineering department, as it can be time-consuming. However, that weeded out installers who might not properly represent the Primus Line product. Leaving the company with what Moody refers to as, “The strongest group of installers any manufacturer could ask for.”
Setting Primus Line Apart
Setting the Primus Line product offerings apart from what is available in the marketplace for 6- to 20-in. pressure pipe rehab is its ability to be used in longer pulls — up to 8,000 ft in a straight line — and navigate bends/transitions in the pipe.
“We’re a standalone product and we’re unique in that aspect. When I say standalone, I mean that we don’t interact with the host pipe,” Moody says. “We simply use that host pipe as a conduit. Once we put our product in, we are taking on all the internal pressures, scour abrasion, all the hydrostatic loading, all the surge pressure and it’s not being transferred back to the host pipe.”
While system owners in the United States and Canada operate similarly, Moody notes that gaining acceptance of the Primus Line product in the United States was easier than in Canada. He chalks this up to the fact that the Canadian market was already introduced to a CIPP pressure pipe solution, and many were reluctant to veer from that.
“The U.S. market, with its engineers and pipe owners, seemed a bit more progressive in their thinking. They will consider all the options when deciding on what to put into critical infrastructure,” he says.
Such was the case when Primus Line was brought in to rehabilitate 18,000 ft of 6-in. processed water line at a major Houston oil refinery. The refinery put out an RFP for CIPP of the line and a Primus Line installer responded. They realized that, based on several factors, CIPP was not as practical as Primus Line for this project.
“He [the installer] got with us and we had our engineers look at it because with every project we do a feasibility review with our engineering team,” Moody says. “Our head of engineering looked at it and said, ‘this is, this is how we would do it.’ We discussed where the pits should be, length of the pull, the pull forces, etc.”
This approach meant that the installer was able to competitively bid on the project using Primus Line and the owner accepted the bid, based on the recommendation of this installer and because they saw it as a huge savings not only in money but in time.
According to Moody, Primus Line came in at approximately $1.5 million less than CIPP and the job was done in 30 days as opposed to CIPP, which would have taken longer. The project also marked one of the longest pulls of Primus Line to date.
“That project was challenging for many reasons like logistics, environmental and social impact concerns, too. In the end, it was a perfect project that was executed by one of our partners, Hill Services. They have embraced the product and use it in the industrial, as well as the municipal market,” Moody says adding that other installers have helped Primus Line achieve many milestones in the last decade. “Other partners, like J. Fletcher Creamer and Sons, Advantage Reline, as well as Insituform, have helped to instill confidence of the product in the market place.”
North American Impact
Since coming to North America, Primus Line has been able to take advantage of the perpetually growing pressure pipe rehabilitation market. Moody explains that while known here as a potable water rehab product, wastewater now takes up about 30 percent of its North American projects and about 15 percent are unique, one-off, projects where there really isn’t another viable solution.
“We end up being the solution that they didn’t know they needed but we were able to, you know, come in and solve their issue for them,” he says. “There are different examples and what limits us in these cases often is the knowledge of and understanding of how Primus Line operates within systems.”
To that end, the primary function of the Primus Line sales force is educating engineers and installers and empower them with knowledge of how the Primus Line system really works. Moody and his team are also actively working to develop an ASTM standard for FFRP pressure pipe rehab, as well as helping develop AWWA’s M28 standard to include the product.
That evangelical nature of the Primus Line salesforce got a boost two years ago when it was announced that Primus Line and MTC, an Aegion Company, partnered to distribute the Primus Line product in North America. This agreement will help bolster Primus Line’s growth in the Americas twofold.
“The two major benefits of this were that the largest rehabilitation company Aegion — which is the undisputed market leader — has made an educated decision to partner up with Primus Line, a Germany-based company, to take on the product in North America,” Moody says. “This is a massive endorsement as most engineers see them as a trusted partner and source of expertise while investigating solutions to their problems. We are not a silver bullet and cannot solve every engineer’s problem. That changes when you have experienced partners who can bring almost every type of solution to the table and will select the appropriate product for the project.”
He adds, “Having the product on the ground in the U.S. with MTC as the distributor and logistics coordinator means that lead times for delivery went from 15 weeks to five days, sooner in some cases. It’s a huge advantage for us.”
With decreased lead times and more projects on the horizon, Primus Line was prompted to add engineers to keep up with the demand for the product in North America.
And the sky is the limit as, “… We look forward to a time in the future where we will be producing the product in the United States,” Moody says.
Mike Kezdi is the managing editor of Trenchless Technology.