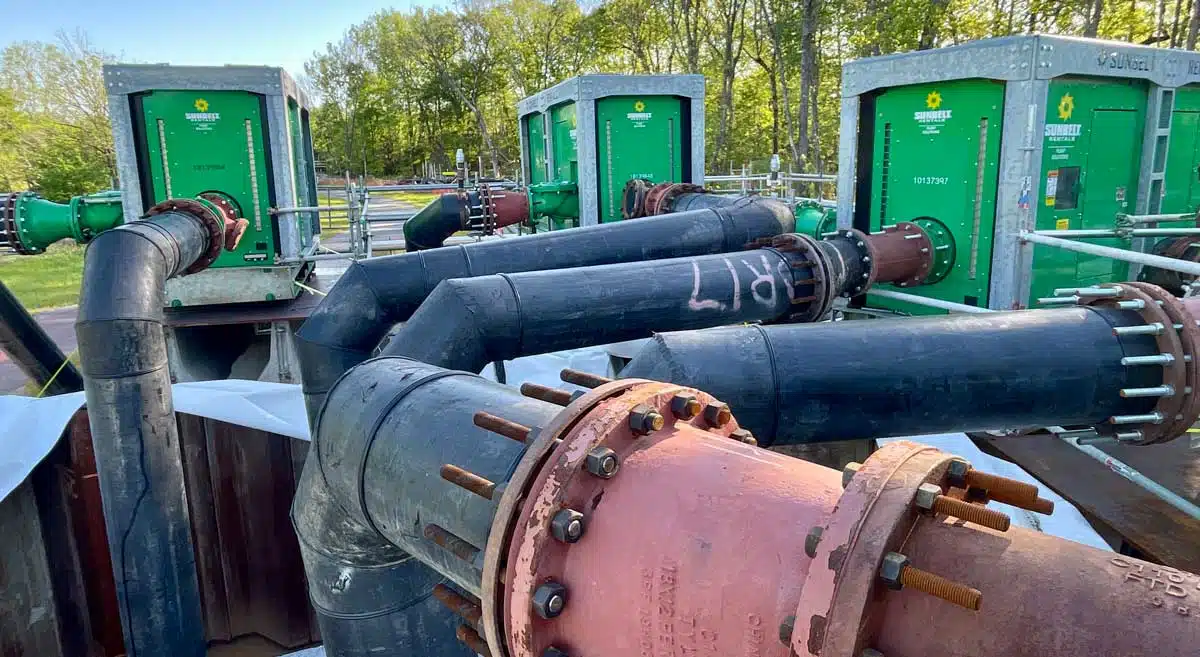
Navigating Challenges and Building Bridges – Pre-Design Preparation Critical to Sewer Bypass Success
During fall 2019, a major city in the Southeast was in the process of planning and designing a substantial sewer rehabilitation project. The objective was to rehabilitate 2,700 ft of 78-in. sewer pipe using the cured-in-place method.
This project presented several formidable challenges in terms of access. The project site had the potential for flooding, and the sewer easement itself posed additional difficulties as it passed beneath a busy four-lane NCDOT parkway, traversed a bustling mall parking lot, crossed a two-lane road, and continued along a newly paved walking trail within an active greenway.
During the design phase of many sewer rehabilitation projects, the focus tends to be primarily on the access areas directly impacted by the scope of the rehabilitation. However, for the rehabilitation to take place there is a high probability the diversion of the sewer will impact the community outside of the rehab scope. Therefore, it is critical to pull back and consider the broader picture. Every community strives to avoid congested roads, blocked driveways, detours, inaccessible businesses, or closed parks.
Recognizing the potential challenges for this project, the City and design engineers took a proactive approach by involving experts early in the design process to set realistic expectations for executing the temporary diversion. This foresight allowed the project team to identify access issues in advance and create a comprehensive plan for the bid documents. The plan detailed key access areas, methods for crossing major roads, and right-of-entry strategies to minimize the impact on the community and local businesses.
Scoping the Project
The primary goal was simply to divert the flow for the cured-in-place lining process. The suction structures chosen to bypass the flow were positioned near a creek prone to flooding. The bypass piping route required the pipes to ascend an embankment, cross the four-lane DOT parkway, navigate the mall parking lot, cross the two-lane road, and finally traverse the greenway to reach the downstream manholes near the treatment plant. The bypass pumps had to generate enough pressure to convey 57 million gallons per day through 4,600 lf of piping. In addition, a pressurized 36-in. force main tied into the 78-in. line, necessitating another separate bypass design. Lastly, given the sewer line’s proximity to the creek banks, flood mitigation measures were crucial to protect the pumping system and prevent inflow into the sewer line during extreme weather events.
Detailing the Sewer bypass Challenges
The primary project challenge was the route for the sewer bypass piping — across a state DOT controlled major parkway. The project team considered — and rejected — several options for the bypass discharge pipe to cross the parkway. A typical solution is trenching — a shallow road cut for the bypass pipes with a road plate over the cut. Given the mild temperatures in the southeast, pipes rarely freeze, therefore water lines are placed without much cover. In this case, the existing utilities were simply too shallow to allow adequate depth to place the 24-in. bypass discharge piping.
Another possibility called for a jack-and-bore process to install large steel casing for the bypass pipes to go beneath the existing utilities. Since the alignment of the bore was in the same right of way as the existing 78-in. sewer, it was noted the 78-in. sewer was tunneled out of solid rock. This increased the chances of jack and bore failure if rock was encountered, thereby driving up cost for the owner. Additionally, the placement of the bore pit in the parking lot would have negatively impacted the mall.
The road crossings were not the only challenge. The City required the suction points and all bypass pumps to be protected from flood waters of the creek to an elevation that was higher than the 100-year flood plain in case of hurricanes or tropical storms while still providing access to the pump watch personnel for fueling, operations and maintenance.
The City, engineers and Sunbelt Rentals discussed and resolved the challenges even before the project went to bid. This way, the specifications would provide clarity to the contractors bidding on the project by including all the required elements for the access and the bypass.
Bridging the Route
A previous siphon sewer rehab project in Montgomery, Alabama, inspired the solution for crossing the North Carolina DOT roadway. The Montgomery project required the use of bridges to cross multiple waterways for the bypass pipes. They were efficient and relatively easy to deploy. This led the team to the initial design for a temporary aerial truss bridge on towers to support the 90,000 lbs of the three 24-in. HDPE pipes, while still providing the vehicle clearance required by the DOT.
The pipe traveled up and over the parkway on a 135-ft aerial bridge which provided close to 20 ft of vehicle clearance. The piping then traveled through the mall on right-of-way easement, which required water-filled barriers to protect the above ground pipe, along with several trenches and temporary road plates to bury the pipe for unimpeded vehicle access to the mall. The team opted to build another 100-ft aerial bridge to avoid another difficult road cut to which allowed the three discharge pipes to cross a two-lane road. After that, the pipe ran down the east side of the greenway on its way to the discharge manhole. Extensive composite matting was utilized to protect the newly paved greenway from pipes and equipment, including heavy trucks and resin tankers.
At the discharge point, the three 24-in. pipes converged into a 36-in. common discharge manifold, and a 36-in. HDPE elbow facilitated the transition into the downstream manhole. This reduced the need for additional modifications to the discharge manhole besides a cone pull.
Flooding Protection and Remote Monitoring
To keep the pumps above the creek floodplain, Sunbelt Rentals used steel road plates and concrete jersey barriers to elevate the pumps 6 ft above grade. To protect the suction location, the existing lid of the downstream suction vault was removed, and a 6-ft wall of steel sheeting and a waterproof membrane was installed to prevent potential flood waters from infiltrating the sewer.
Additionally, another challenge of elevating the pumps 6 ft above grade was the need for safe access. Accessing pumps with ladders was not an efficient option. As a solution, Sunbelt Scaffolding Services constructed scaffolding around both elevated suction locations which allowed for safe access for the Pump Watch Technicians to operate, fuel and maintain the pumping system.
From the suction point, all pumps conveyed flow using a common manifold and discharged through three 24-in. SDR26 HDPE lines. Flow meters were installed on each of the main 24-in. discharge lines and several pumps were connected to Sunbelt Rentals PumpSentri. The pumps’ performance and the system flow were continuously monitored using PumpSentri technology, providing real-time data through a remote dashboard to which all the project stakeholders had access.
Force Main Challenge
Managing the 36-in. force main posed another challenge. Initially, the plan involved routing the force main through the three 24-in. discharge lines. However, due to increased friction and head loss from the bridges, it was determined that the existing pump station might struggle to overcome the additional pressure. Fortunately, a pig launch retrieval station with a valve near the force main discharge offered a solution. Sunbelt Rentals used a single 24-in. HDPE pipe to redirect the force main to a manhole downstream of the first suction location, allowing the flow to be conveyed back upstream to the two bypass suction structures.
Valuing Foresight
The project required 13,200 lf of 24-in. HDPE pipe, and 10 high-volume 12-in., 325-hp primary pumps, with eight serving as primary and two on standby to achieve the design flow of 57 MGD. To ensure effective operation, two technicians were on-site to perform Pump Watch maintenance and refueling of the diesel pumps.
Throughout the project’s duration, the temporary sewer bypass system operated flawlessly. While under full bypass, the city personnel observed degradation in the downstream suction structure and decided to repair it while the bypass system was still in place. Once the rehabilitation of the 78-in. sewer was completed, the pumps at the downstream manhole were removed. The 36-in. force main was reinstated, and the upstream bypass system facilitated the diversion needed to complete the manhole repairs. This approach resulted in significant cost savings for the city, utilizing the existing partial bypass system and the already operational discharge pipe.
The successful delivery of this complex project was made possible through the diligent planning and ingenuity of the design team, coupled with the speed and efficiency of the prime contractor. By involving temporary diversion experts early in the process, the project’s sewer bypass challenges were addressed proactively, resulting in reduced risk, cost and impact on the community.
Ladd Gould is national strategic customer manager at Sunbelt Rentals Inc.