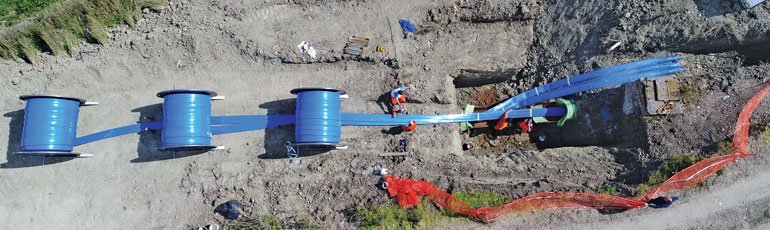
Pipe Relining in Palermo, Italy
The Nuovo Scillato water main is one of the main-drinking water conduits of Palermo, Italy and the coastal municipalities east of the city. Built in the 1980s to supplement and reinforce the old Vecchio Canale Scillato system (dating back to the late 19th century), it conveys water from four springs that issue from Mount Fanusi, near Madonie, at a variable flow rate of 500 to 1000 l/s, delivering an average annual volume of about 22 million m³ of water to users.
The conduit is made from DN 900 steel pipes with a total length of 62 km. It was designed to convey up to 1,000 l/s. As a result of seismic activity in 2003, the localities of Burgitabus (Cerda) and Scacciapidocchi (Termini Imerese) along the valley of the Imera Settentrionale River have experienced slow landslide movements, primarily affecting areas with outcrops of Argille Varicolori clay.
RELATED: Nova Scotian Contractor Opts for Primus Line Solution
Over the years this has led to repeated and increasingly frequent episodes of pipe damage that have resulted in service interruptions. The drought of the past two years and the problems with the Rosamarina dam, which supplies more than 30 million m3 of water annually to Palermo, has considerably reduced available water reserves. In January 2017, pending completion of the layout variant to avoid the landslide areas – a long job estimated to take at least two years – AMAP S.p.A, operator of the Integrated Water Service of Palermo, acted to head off a serious water crisis and asked Danphix Srl to devise a quick provisional solution to help restore the “Nuovo Scillato” aqueduct to full operation.
The sections requiring repair were pinpointed using previous knowledge of the condition of the pipeline and the ruptures in the two localities. A GPS survey of the current pipeline layout was then conducted, its underground positioning duly located by Geo-Radar detection. The data obtained showed the almost regular course of the DN 900 pipeline. The limited displacements involved meant that a hose lining installation was possible. In particular, the rehabilitation of a 1,030-m section in the Burgitabus area and 640 m in the Scacciapidocchi area was envisaged. An aerial survey was also carried out with a drone, which made it possible to obtain orthophoto maps of the two areas involved. The design solution had to take account of the flow rate to be handled, the operating pressures and the implementation time frame of the repair work. Being a provisional repair project, the immediate goal was to convey at least 400-500 l/s from the Scillato springs, thus allowing the recovery of an annual volume of about 15 million m³ – approximately 15 to 20 percent of the volume used by the city of Palermo system as a whole.
The choice of the hose lining technique in both sections of the pipe (rather than steel tube replacement, excluded both on account of past experiences and the time available) arose from the need to achieve an integral conduit flexible enough to absorb landslides. Regarding the pipe material to be used, and given the pressures (25 to 30 bar) and diameter requirements, a careful market study narrowed the choice down to the Primus Line, a special flexible pipe produced by German company Rädlinger primus line GmbH.
RELATED: Flexible Relining of Pipes with Primus Line Pressure
The Primus Line combines the flexibility and extreme lightness of the textile sheath with the strength of steel tubing. These properties are obtained by using seamless-woven aramid fiber (Kevlar) and a dual-component plastic coating applied to the sheath (proofed against fluid egress on the inside and abrasion on the outside). The diameters of the Primus Line System were chosen to suit the two repair sections: in the Burgitabus stretch, three Primus Liner DN 250 PN 30 were used, while in the Scacciapidocchi section the diameter of the three liners was increased to Primus Line DN 300 PN 25 on account of the lower pressures. To ensure the proper operation of the repair sections and their connection to the existing pipeline, five vent devices and four coupling caps were manufactured from specially shaped steel.
As a preliminary step, some civil works were necessary in order to prepare the work areas (opening of access lanes, excavations and baring of pipes, etc.) and to facilitate the construction of a stretch of about 120 m of HDPE DN 1000 pipe casing in Scacciapidocchi, where the old steel pipe had been replaced with a DN 400 pipe. From an operational standpoint, the works were divided into three sections: two of about 500 m in Burgitabus and a 640-m length in Scacciapidocchi. Access and control windows were created on the existing pipe at the start and end points of the single sections and at the positions of the five existing vents to be repaired.
After a video inspection and initial cleaning with tubular brushes, it was necessary in all three sections to work internally to remove the rough edges and burrs of the socket welded joints of the pipes. In addition, the video inspections revealed some critical areas of landslide damage in the DN 900. This necessitated the baring and realignment of the pipe, with the insertion of short butt-welded steel sleeves.
For each individual section, three Primus Liner were inserted in a single operation, with the three transport reels with the coiled liner positioned one after the other. The liners were securely fastened to each other with tape prior to the insertion into the existing pipe, with special care taken to keep them in a uniform position along the whole stretch. At the same time, the special steel parts for coupling and venting were manufactured; targeted quality control procedures were performed both during production and installation (for the couplings). PN 40 flanged manifolds were used for the joints between the Primus Line and the special steel vents and coupling pieces.
At the position of the vents, solid joints were installed between the new pieces and the DN 900 pipe by creating supportive steel structures, welded to the existing pipe so that in case of a landslide, the tube would not come into direct contact with the steel parts. The outcome of the preliminary air leakage test confirmed the correct position of the tubes inside the existing pipe, subject to some necessary adjustments.
Pressurized water was then pumped into the repaired parts, with the subsequent cleaning and disinfection of the conduits. The “Nuovo Scillato” water main is now back in operation. The preliminary civil works for the relining began on 24.02.2017, while the supply and installation of the Primus Line began on March 15, 2017. Work is to be completed on Dec. 12, 2017.
In terms of hydraulic engineering, this is the most important rehabilitation project ever performed with trenchless technology in Italy.
Ing. Arnold Cekodhima is CEO of Danphix Srl. Ing. Heiko Manzke is international account manager at Rädlinger Primus Line GmbH.