Pipe Penetrating Radar Technology Takes a Test Drive in Denver
June 8, 2012
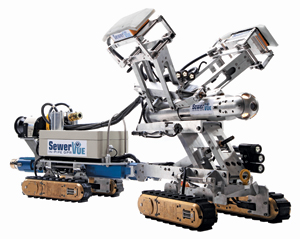
Located on the south side of Denver, the 9.8-mile Harvard Gulch interceptor serves a portion of the City and County of Denver, as well as several small sanitation districts. The interceptor ranges in size from 8 to 48 in., consisting mostly of reinforced concrete pipe (RCP) and vitrified clay pipe (VCP). It was originally constructed in the 1950s and was partially replaced with larger RCP pipe in the late 1970s due to capacity restrictions. In 1983, the ownership and responsibility for the operation and maintenance was transferred to Metro Wastewater Reclamation District (MWRD). Due to the changes of ownership, only limited information is available about the original construction of the interceptor.
The known problems on the Harvard Gulch Interceptor, as with many of MWRD’s concrete pipelines, include significant level of corrosion, cracking issues and root penetration in the concrete pipe segments. The rehabilitation efforts on this interceptor started in 2008 with CIPP lining and is planned to continue in the future. To measure the magnitude of the problems and for operational and financial optimization, accurate interceptor condition assessment is crucial and the timing of rehabilitation and overall asset management is critical. As part of MWRD’s ongoing evaluation of advanced pipe condition assessment technologies, MWRD contacted SewerVUE to carry out a pilot project to demonstrate the capabilities of its patent-pending pipe penetrating radar inspection technology.
Pipe Penetrating Radar
Pipe penetrating radar is the underground in-pipe application of ground penetrating radar (GPR). As the radar pulse travels through a pipe some of the energy will be reflected and refracted by any sharp change in material properties, such as at the interface between pipe material and air, soil or water. The greater the difference in the material properties, then the greater is the amount of energy reflected back. These reflected waves are detected by a receiving antenna and are recorded. This process is repeated as the robot mounted antennas are moved along the pipe to build up an entire profile. This continuous data collection allows the PPR system to be a cost-effective method and to become a valuable information provider in pipe condition assessment. Using high frequency, high-resolution antennas the maximum signal penetration depth can be as much as 5 ft beyond the pipe wall with resolution as small as 1/8 in.
The SewerVUE Surveyor that was used in Denver is the first commercially available multi-sensor inspection (MSI) robot that uses visual and quantitative technologies (CCTV, LIDAR and PPR) to inspect underground pipes. This fourth generation PPR pipe inspection system is mounted on a rubber-tracked robot and equipped with two high-frequency PPR antennae. Radar data collection is obtained via two independent channels in both in and out directions, providing a continuous reading on pipe wall thickness, rebar cover and locating voids outside the pipe.
Inspection & Results
The 880-ft long pipe segment of 27-in. RCP selected by MWRD engineers for the pilot project was inspected in a few hours while the pipe remained in service. Jeff Maier, P.E., engineer in charge of MWRD’s wastewater pipeline condition assessment and rehabilitation program, including the evaluation of new technologies, was pleased with the results of the demonstration. “The SewerVUE PPR system provided accurate information on the Harvard Gulch Interceptor pilot project that we verified by measuring and analyzing concrete cores that MWRD physically extracted from the pipe wall itself earlier in 2011. The PPR provided useful information about the remaining pipe wall thickness, rebar, and what was happening behind the pipe in an efficient, non-destructive and cost effective manner.”
The inspection data were processed using Pipe Penetrating Radar Data Interpretation Application (PP-RADIAN), SewerVUE’s proprietary radar processing software. The interpreted PPR data showed the pipe wall thickness, rebar cover and grouted sections of the pipe. The pipe wall thickness from the PPR survey matched closely (98 percent) to the core sample obtained earlier by MWRD personnel.
Summary & Conclusions
LIDAR results complement the visual and PPR data and are provided as foldout views together with the foldout views of the CCTV and the interpreted PPR profiles. LIDAR results are color-coded: white marks no corrosion, while yellow and red colors mark increasing amounts of corrosion
The PPR results, along with the more prevalent pipe inspection methods, gave MWRD valuable information about the overall structural condition of the inspected pipe segments and helped provide non-destructive asset management information in a cost-effective way. The SewerVUE PPR technology demonstration was especially useful to MWRD because it not only provides the laser profiling of other pipe inspection systems, but it also includes the pipe penetrating radar component and ability to “see” into the pipe wall. In comparing results obtained from other evaluations, PPR has demonstrated early successes as a standalone pipe inspection system operated both in manned entry and remote robotic mode.
The integration of advanced pipe condition assessment technology into the MWRD pipeline condition assessment program will provide detailed supplemental inspection information in critical pipe segments where condition ratings are difficult to determine or where it is suspected that corrosion has significantly deteriorated the structural integrity, and consequently shortened the lifespan of these pipe segments. It is expected that advanced pipe condition assessment technologies will eventually be used on approximately 10 to 20 percent of pipe in the MWRD Interceptor System.
Csaba Ékes is the founder and president of SewerVUE Technology Corp., a company specializing in developing advanced pipe condition assessment technologies.